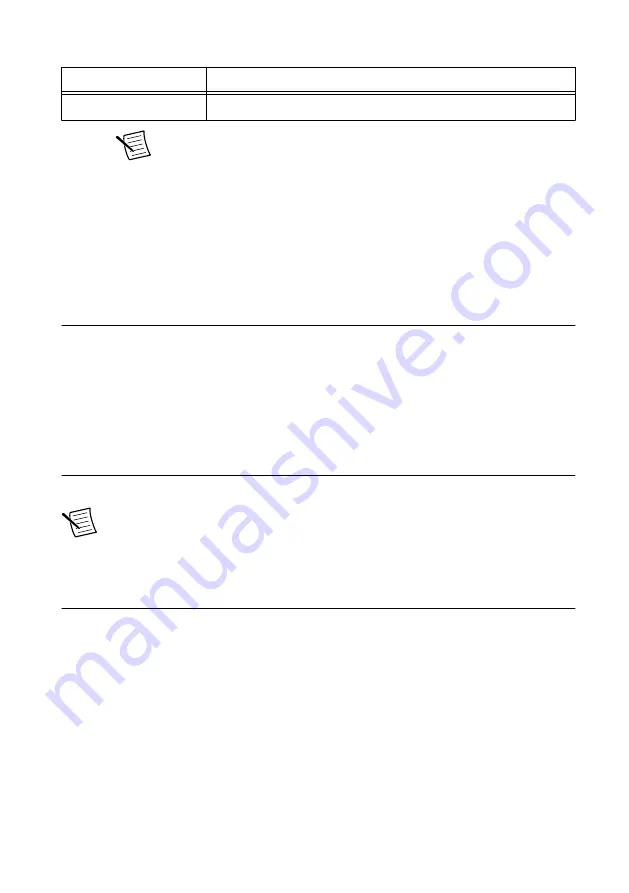
Table 5.
NI 9252 Adjustment Configuration
Physical Channel
Reference Value
cDAQ1Mod8/AI0:7
The actual value of the voltage output of the calibrator
Note
The module acquisition is started each time the adjust function is
called. There is a delay of approximately 550 µs from the acquisition start
until module data becomes available.
g) Set the calibrator to Standby mode (STBY).
h) Repeat steps d through g for each point in the array.
i)
Close the calibration session.
j)
Clear the task.
4. Disconnect the NI 9252 from the calibrator.
EEPROM Update
When an adjustment procedure is completed, the NI 9252 internal calibration memory
(EEPROM) is immediately updated.
If you do not want to perform an adjustment, you can update the calibration date and onboard
calibration temperature without making any adjustments by initializing an external calibration,
setting the C Series calibration temperature, and closing the external calibration.
Reverification
Repeat the
Verification
section to determine the As-Left status of the device.
Note
If any test fails Reverification after performing an adjustment, verify that you
have met the Test Conditions before returning your device to NI. Refer to the
Worldwide Support and Services
section for assistance in returning the device to NI.
Accuracy under Calibration Conditions
The values in the following table are based on calibrated scaling coefficients, which are stored
in the onboard EEPROM.
The following accuracy table is valid for calibration under the following conditions:
•
Ambient temperature 23 °C ± 5 °C
•
NI 9252 installed in slot 8 of an NI cDAQ-9178 chassis
•
Slots 1 through 7 of the NI cDAQ-9178 chassis are empty
6
|
ni.com
|
NI 9252 Calibration Procedure
Summary of Contents for NI-9252
Page 1: ...NI 9252...