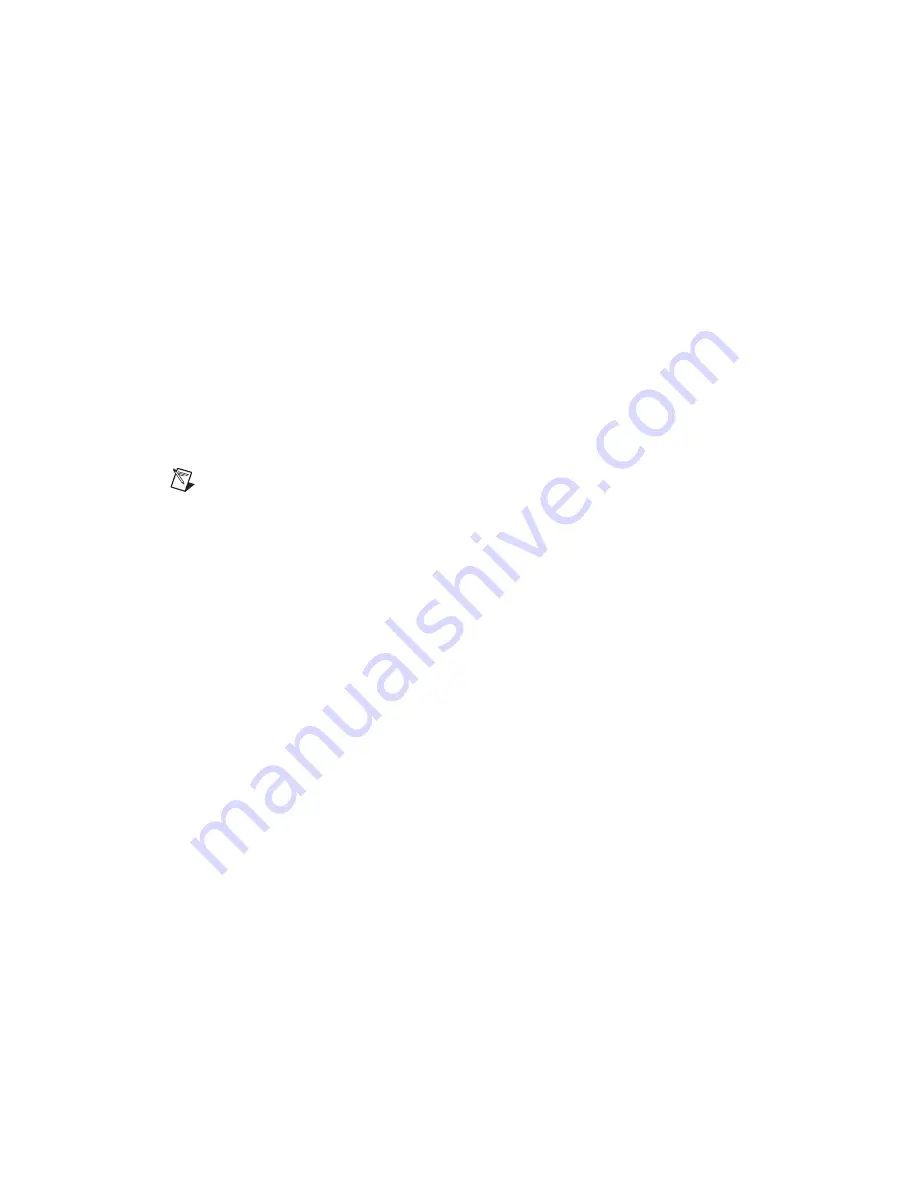
©
National Instruments Corporation
5
6703/6704 Calibration Procedure
Configuring Your Board in NI-DAQ
NI-DAQ automatically detects all 6703/6704 devices. However, to
communicate with the boards, they must be configured in NI-DAQ. The
following steps briefly explain how to configure NI-DAQ. Refer to the
board user manual for detailed installation instructions. You can install this
manual when NI-DAQ is installed.
1.
Turn off the power to the computer that will hold the board.
2.
Install the board in an available slot.
3.
When the computer powers up, launch the Measurement &
Automation Explorer utility.
4.
Configure the board device number.
5.
Click the
Test Resources
button to ensure that the board is working
properly.
Your device is now configured.
Note
After a board is configured with the Measurement & Automation Explorer, the
device is assigned a device number. This number is used in each of the function calls to
identify which DAQ device is to be calibrated.
Writing Your Calibration Procedure
The calibration procedure in the
section later in this
document provides step-by-step instructions on calling the appropriate
calibration functions. These calibration functions are C function calls from
the NI-DAQ driver that are also valid for Visual Basic programs. Although
LabVIEW VIs are not discussed in this procedure, you can program in
LabVIEW using the VIs that are named similarly to the NI-DAQ function
calls in this procedure. Refer to the
section for illustrations of
the code used at each step of the calibration procedure.
Often you must follow a number of compiler-specific steps to create an
application that uses the NI-DAQ driver. The
NI-DAQ User Manual for PC
Compatibles
details the required steps for each of the supported compilers.
Be aware that many of the functions listed in the calibration procedure use
variables that are defined in the
nidaqcns.h
file. To use these variables,
you must include the
nidaqcns.h
file in your code. If you do not want to
use these variable definitions, you can examine the function call listings in
the NI-DAQ documentation and the
nidaqcns.h
file to determine what
input values are required.