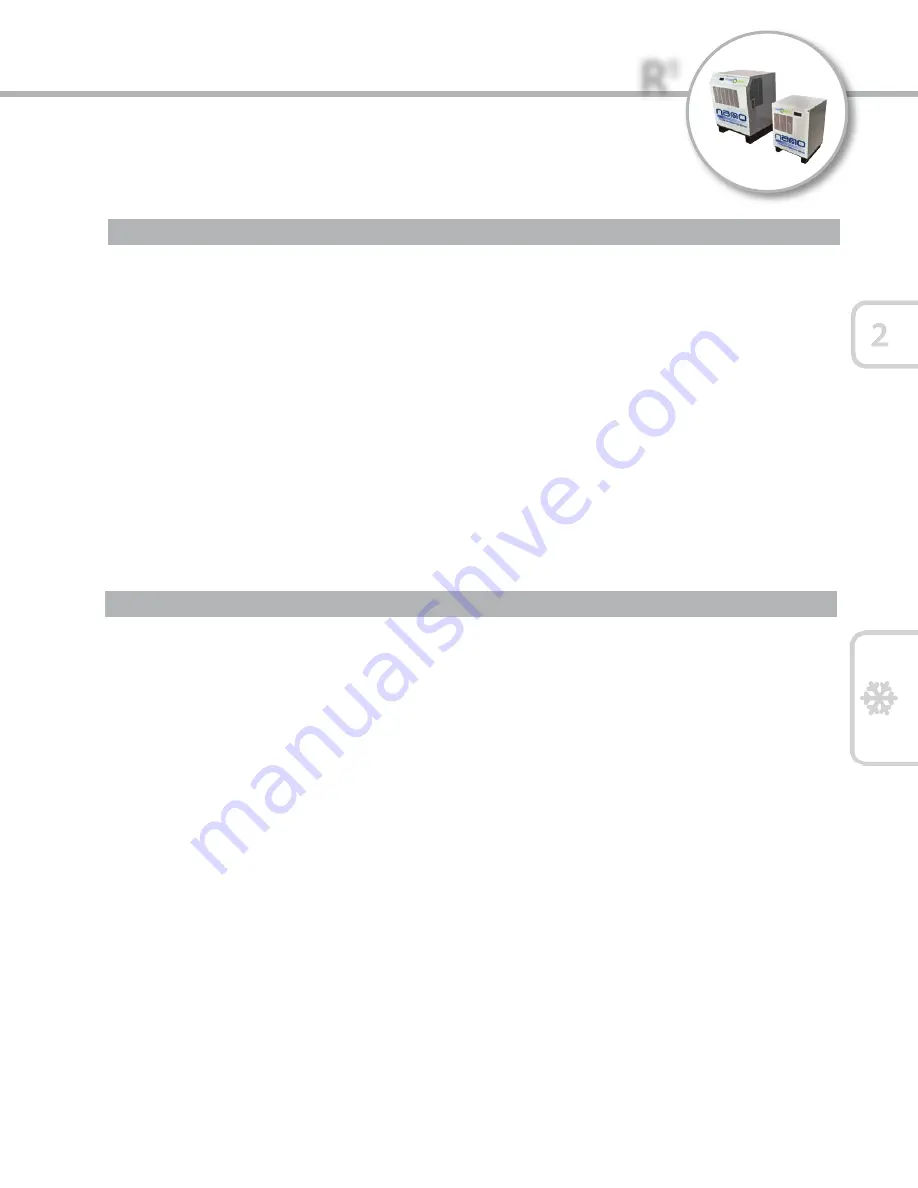
27
cycling refrigerated air dryer
R
1
Cleaning the drain Y-strainer*
General comments
The solenoid drain is protected by a strainer to prevent damage to the solenoid valve seals from metal parti-
cles or dust. This strainer must be cleaned 1 week after the first start-up and then once per month. If this is
not done, the strainer will clog and it will not be possible to purge the system correctly. Liquid phase water
will appear in the compressed air network.
Procedure
1. Close the manual valve on the purge (see the refrigeration/pneumatic circuit diagram).
2. Unscrew the strainer lock nut.
3. Withdraw the metal mesh, clean and refit.
4. Check the condition of the seal and replace if necessary.
5. Tighten the strainer lock nut.
6. Open the manual valve on the purge line.
*You must comply with the recommendations at the beginning of this chapter.
The solenoid valve must always be protected by a filter to ensure that solid particles do not prevent it from
opening and closing correctly. If particles do get through the filter and cause faulty operation of the solenoid
purge valve, it is must be dismantled and cleaned.
Procedure
1. Close the manual valve on the purge line (see refrigeration/pneumatic circuit diagram).
2. Disconnect the solenoid valve power supply.
3. Disconnect the solenoid valve from the pipework and clamp it in a vice.
4. Unscrew the coil lock nut and take it off the plunger.
5. Unscrew the plunger from the valve seat.
6. Check the O ring and the other components. Clean carefully.
7. Re-assemble the valve by reversing operations 1 to 5.
Do not over tighten the coil lock nut as this could prevent the valve from closing.
8. Refit the solenoid valve to the pipework, respecting the direction of the air flow indicated by an arrow on
the body.
9. Reconnect the power supply to the solenoid purge valve.
10. Open the manual valve on the purge line
*You must comply with the recommendations at the beginning of this chapter.
Solenoid valve maintenance
*
Summary of Contents for NXC 0020
Page 1: ...NXC series cycling refrigerated air dryer user guide...
Page 61: ...notes...
Page 62: ...notes...