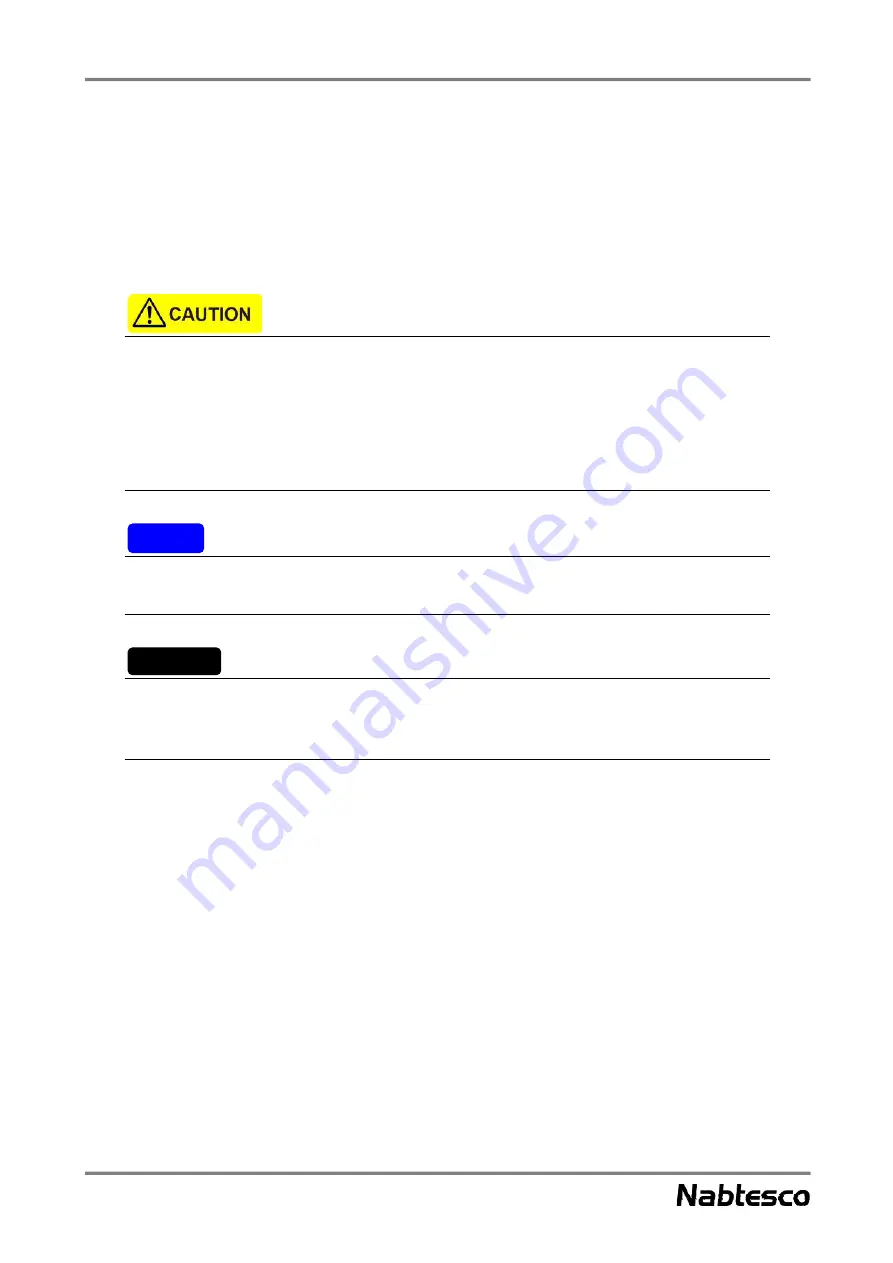
Chapter 4 Preparations for Installation
13
Unpacking
4.3.
Check the following points when unpacking.
• Before using this product, check the contents of the packing box and confirm that all the ordered items
are included.
• Check the top and bottom direction of the packing box and unpack it.
When transporting the reduction gear, take extra care so that it will not fall down or topple over. It
could cause injury to the workers or damage to the reduction gear.
Before using this product, check the contents of the packing box and confirm that all the ordered items
are included.
If an incorrect part is installed, it could cause injury to the workers or damage to the device in which
the incorrect part is assembled and the reduction gear.
If it is left upside down, it could cause damage to the reduction gear. (Refer to Fig. 4-3 for the
direction.)
The reduction gear is coated with rust prevention oil before shipping. Therefore, if it is used as it is, the
rust prevention oil could ooze from the bolt hole or flange mating face during operation. In addition,
the rust prevention oil makes the reduction gear slippery. Wipe it off as necessary before use.
Note
Important