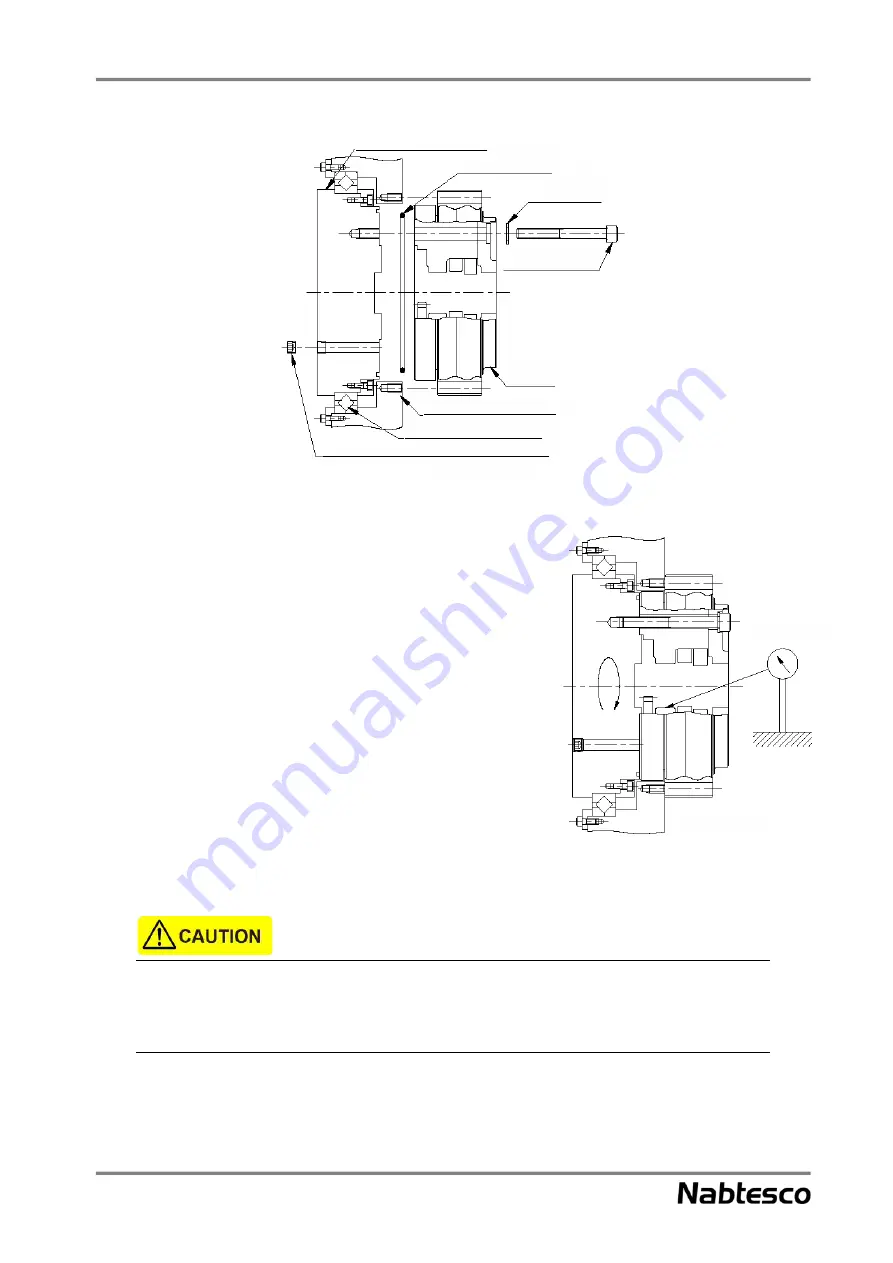
Chapter 5 Installation
43
• Check the installation accuracy of the reduction gear
Step 2
using a dial gauge.
• Turn the reduction gear from the shaft side by a turn
and check the deviation in the dial gauge reading.
Adjust the position so that the deviation is within 20
µm.
• For the case rotation specification, fix the dial gauge
onto the case installation component and rotate the
case installation component by a turn, and then check
the deviation. Adjust the position so that the deviation
is within 20 µm.
• Tighten the temporarily fixed hexagon socket head
cap screw with the specified tightening torque.
• Check again on the dial gauge that the deviation is
within 20 µm.
(Reference: “5.1 Bolt tightening torque”)
If the hexagon socket head cap screw is not tightened with the specified torque, the reduction gear
does not deliver the designed performance. In addition, it could cause injury and damage to the
customer’s device and the reduction gear.
Fig. 5-27
Shaft installation component
O-ring (I)
or liquid sealant
Hexagon socket
head cap screw
Serrated lock
washer
Reduction
gear
Case installation component
External load support bearing
Plug for tapped hole for injecting/draining grease
Fig. 5-28
Dial gauge