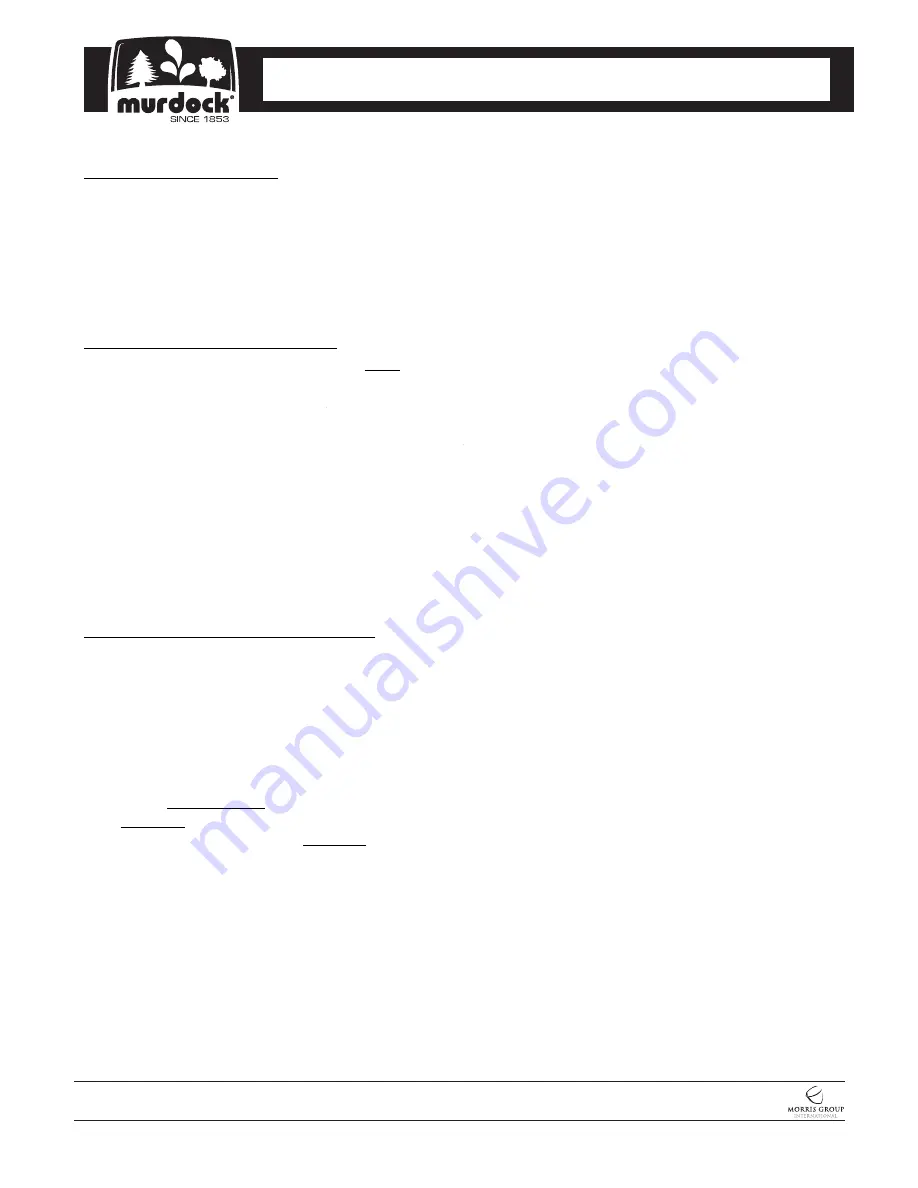
TROUBLE SHOOTING:
.
1. RESTRICTED OR NO WATER FLOW:
a. Ensure Water Supply service stop valve is fully open.
b. Verify minimum 20 psig supply line flow pressure.
c. Check for twist or kinks in spout tubing.
d. Check the water inlet “Y’’ strainer. Sediment from the main supply can get trapped in the
screen along with installation materials such as pipe dope and flux. The screen should be
cleaned and checked on a regular basis and replace if needed.
e. Flow control in solenoid valve outlet elbow clogged remove & clean.
SENSOR TROUBLE SHOOTING:
1. IF LIGHT WITHIN SENSOR DOES NOT FLASH ONCE WHEN USER IS WITHIN RANGE:
a. Verify 9VDC output of battery pack.
b. Replace defective batteries.
c. Sensor in “Security Mode” after 30 seconds of constant detection. Remove source of
detection and wait 30 second before checking.
d. Sensor is picking up a highly reflective surface. Eliminate cause of reflection and wait 30
seconds before checking.
2. IF LIGHT WITHIN SENSOR LENS FLASHES ONCE WHEN THE USER IS WITHIN RANGE:
a. Repair bad connection from sensor to solenoid.
b. There is debris or scale in the solenoid assembly. Remove solenoid, pull out plunger and
spring. Clean with scale remover solution.
c. There is debris or scale in center or two holes in convolution of the water diaphragm.
Remove and clean.
CLEANING & MAINTENANCE GUIDE:
For Powder coated units:
Units should be cleaned using a mild soap solution with a sponge or
cotton cloth. Wipe down surfaces then rinse with clean water.
For Stainless steel units:
1. To Remove water spots or rust spots, stainless steel cleaner/polish on a cloth is
recommended.
2. If there are stubborn spots or if you wish to treat a scratch, synthetic abrasive general
purpose pads such as scotch brite are recommended.
3. Apply stainless steel cleaner/ polish to the synthetic abrasive pads and carefully rub the
panel with the grain.
4. DO NOT use harsh chemicals, abrasive or petroleum based cleaners. Use of these will
void the Acorn warranty. DO NOT use abrasives on powder coated units.
5. Stainless steel should be kept clean at all times. If a coating of stainless steel cleaner/
polish is maintained, stainless steel surfaces will retain their new, clean, polished
appearance indefinitely.
6. Periodically remove access panel of cooler and clean out inline “Y’’ strainer
MURDOCK MFG. •
15125 Proctor Avenue • City of Industry, CA 91746 USA
Phone 800-453-7465 or 626-333-2543 • Fax 626-855-4860 • www.murdockmfg.com
Member of
7013-037-001
Revised: 07/26/18
Page 13 of 16
I N S TA L L AT I O N / M A I N T E N A N C E I N S T R U C T I O N S
Semi-Recessed Bottle Fillers