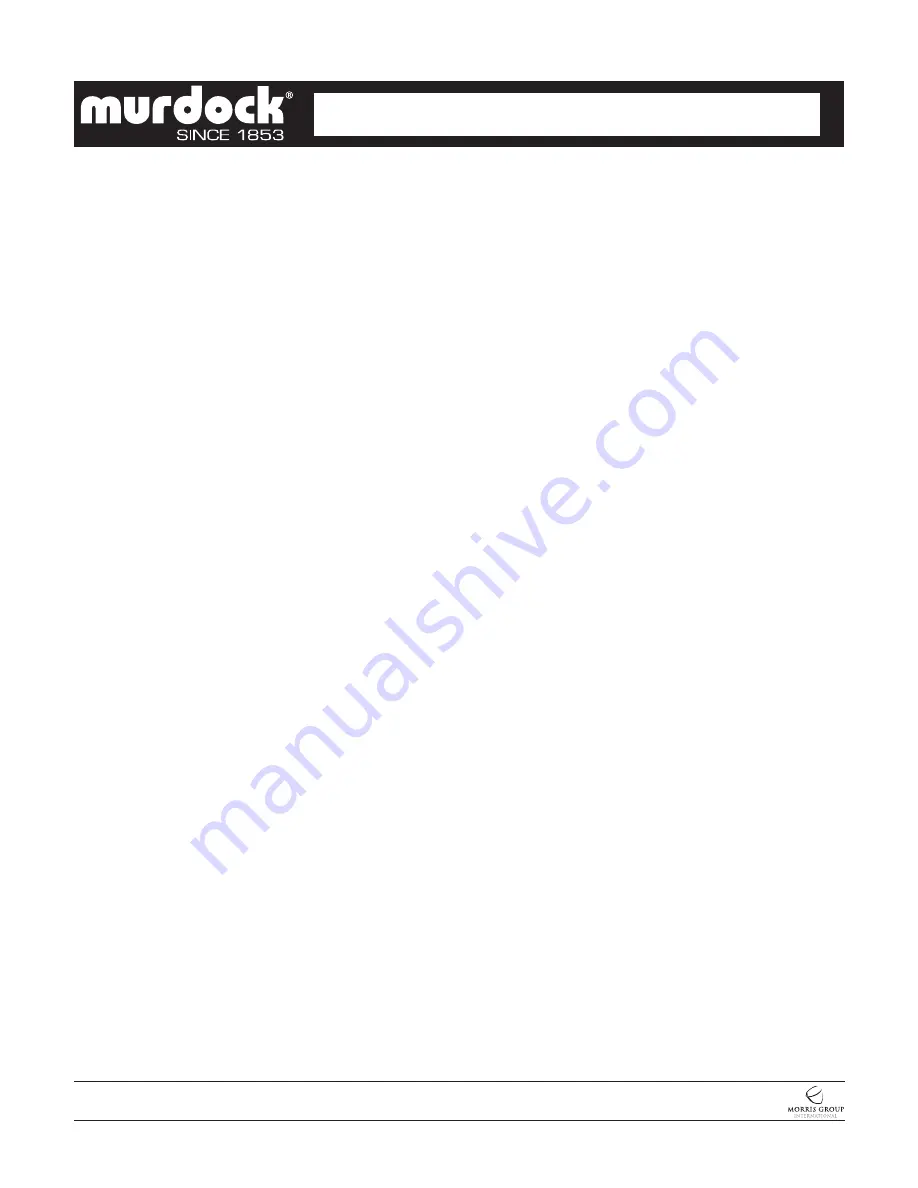
2. Compressor Does Not Run
a. Check the electrical receptacle for power and correct voltage. The incoming voltage
must be within 10% of the rated voltage on the serial nameplate.
b. The cold thermostat is accessible by removing the bottom access cover. If the cold
thermostat capillary bulb loses its charge or becomes kinked it will fail in the open position
causing a disruption of power to the compressor. Unplug the water cooler and using and
ohm meter check for continuity across the two electrical terminals on the thermostat. Install
a new thermostat if there is no continuity.
c. Check for loose wires within the compressor box. The incoming power leads must be
connected to the overload and relay.
d. If all components check positive for continuity then test the wiring harness plug for
continuity to see if there is a broken wire within the wiring harness insulation.
3. Compressor Runs – Water Is Warm
a. The most common cause for a water cooler to run without producing cold water is a loss
of refrigerant. The water cooler must be taken to a certified refrigerant technician for repairs.
b. Make sure the condenser fan motor is operative. The fan blade must turn freely to help
remove the heat of compression.
c. An incorrect refrigerant charge, restriction or defective compressor (not pumping) will also
cause the compressor to run without producing cold water. All these signs indicate a
problem within the refrigeration system and the water cooler must be checked by an
authorized service company.
4. Compressor Cycling On Overload Protector
a. A dirty condenser or a blocked fan will cause a high head pressure and frequent cycling of
the overload protector.
b. Check the incoming voltage to make sure it is within 10% of the serial nameplate rating.
c. A restriction or moisture in the system will also cause intermittent cycling. A certified
refrigeration mechanic should be contacted in this situation.
d. Change the overload or relay if defective.
5. Noisy Operation
a. Check to make sure the fan blade is rotating freely.
b. Make sure the water cooler is correctly mounted to the wall. Absence of the two lower
mounting bolts may cause excess noise and vibration.
c. Check the compressor mounting to make sure the pins and clips are not rattling. If the
compressor appears to be noisy internally, it must be replaced.
6. Restricted Or No Water Flow
a. Ensure water supply service stop valve is fully open.
b. Verify minimum 20 psig supply line flow pressure.
c. Check for twists or kinks in bubbler tubing.
d. Check the water inlet strainer. Sediment from the main supply can get trapped in the
screen along with installation materials such as pipe dope and flux. The screen should
be cleaned and checked on a regular basis and replace if needed.
e. The cartridge valve located in the water control assembly or bubbler can also become
clogged with foreign material. The cartridge valve can only be replaced and not repaired.
f. The water cooler may also develop a freezing condition in which the water will become
frozen inside the evaporator coil. This indicates a refrigeration problem or thermostat
failure in which case the water cooler needs to be checked by a
qualified technician.
A511.5
Page 5 of 9
RVA
05/28/21
7020-921-001
MURDOCK MFG. •
15125 Proctor Avenue • City of Industry, CA 91746 USA
Phone 800-453-7465 or 626-333-2543 • Fax 626-855-4860 • www.murdockmfg.com
Member of
CONTEMPORARY WATER COOLERS
I N S TA L L AT I O N / M A I N T E N A N C E I N S T R U C T I O N S
WATER COOLERS