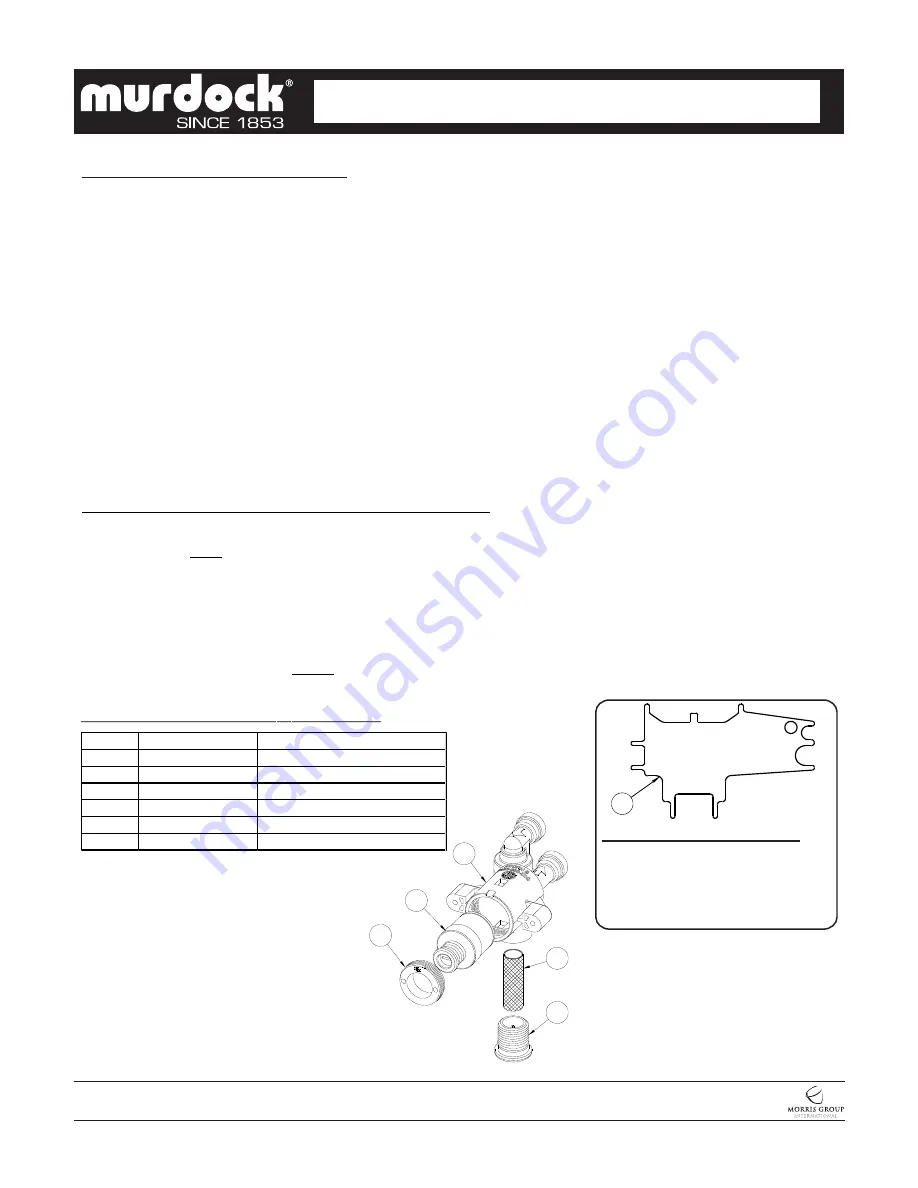
A152-VR-BF4
Page 17 of 20
Date:
10/28/2020
7021-023-001
MURDOCK MFG. •
15125 Proctor Avenue • City of Industry, CA 91746 USA
Phone 800-453-7465 or 626-333-2543 • Fax 626-855-4860 • www.murdockmfg.com
Member of
CARTRIDGE VALVE PARTS BREAKDOWN
3
2
1
5
4
1. Strainer Plug must be removed before Cartridge replacement and Strainer maintenance (no need to turn the
water off at the Angle Stop). Some residual water will drainduring Plug removal.
2. Clean Strainer as needed using clean water.
3. Cartridge Replacement - insert diamond end of the Universal Tool into Pushbutton, rotate 90 degrees and pull
firmly to remove the Button. Remove Cartridge Retaining Nut . Remove and replace Cartridge. When replacing
Cartridge, be sure to align the inlet and outlet Ports on the Cartridge with the Ports in the Valve Body.
—
NOTE: STRAINER SCREEN MUST BE IN PLACE FOR WATER TO FLOW.
CARTRIDGE REPLACEMENT/ STRAINER MAINTENANCE
Note: Use the Universal Maintenance Tool to perform the following:
-Button Removal
-Cartridge Retaining Nut
-Removal of P.E. Tubing from
Universal Maintenance Tool
Push-in Fittings
-Strainer Plug
6
ITEM #
PART NUMBER DESCRIPTION
1
7003-095-000
Valve Body Sub Assembly
2
7000-060-000
Valve Cartridge
3
7000-052-000
Retaining Nut
4
7003-864-000
Strainer, Auto Stop
5
7003-097-001
Strainer Cap
6
7003-194-199
Maintenance Tool
For Stainless steel units:
3.
Periodically remove fountain top and clean out in-line strainer.
CLEANING & MAINTENANCE GUIDE:
For Powder coated units:
Units should be cleaned using a mild soap solution with a sponge or cotton cloth.
Wipe down surfaces then rinse with clean water.
2.
Excess dirt or poor ventilation will cause the compressor overload protector to turn the compressor off and it
will cycle on and off with no cold water coming out of bubbler. Periodically clean with vacuum cleaner, air
hose or brush the condenser fins and cabinet ventilation louvers. In environments where dirt and dust is
more prevalent, clean more frequently.
1.
Motors have lifetime lubrication and do not require scheduled maintenance.
4.
Periodically remove access panel of cooler and clean out inline “Y’’ strainer
1. To Remove water spots or rust spots, stainless steel cleaner/polish on a cloth is recommended.
2. If there are stubborn spots or if you wish to treat a scratch, synthetic abrasive general purpose pads such as
scotch brite are recommended.
3. Stainless steel should be kept clean at all times. If a coating of stainless steel cleaner/polish is maintained,
stainless steel surfaces will retain their new, clean, polished appearance indefinitely.
CONTEMPORARY WATER COOLERS
I N S TA L L AT I O N / M A I N T E N A N C E I N S T R U C T I O N S
DRINKING FOUNTAINS