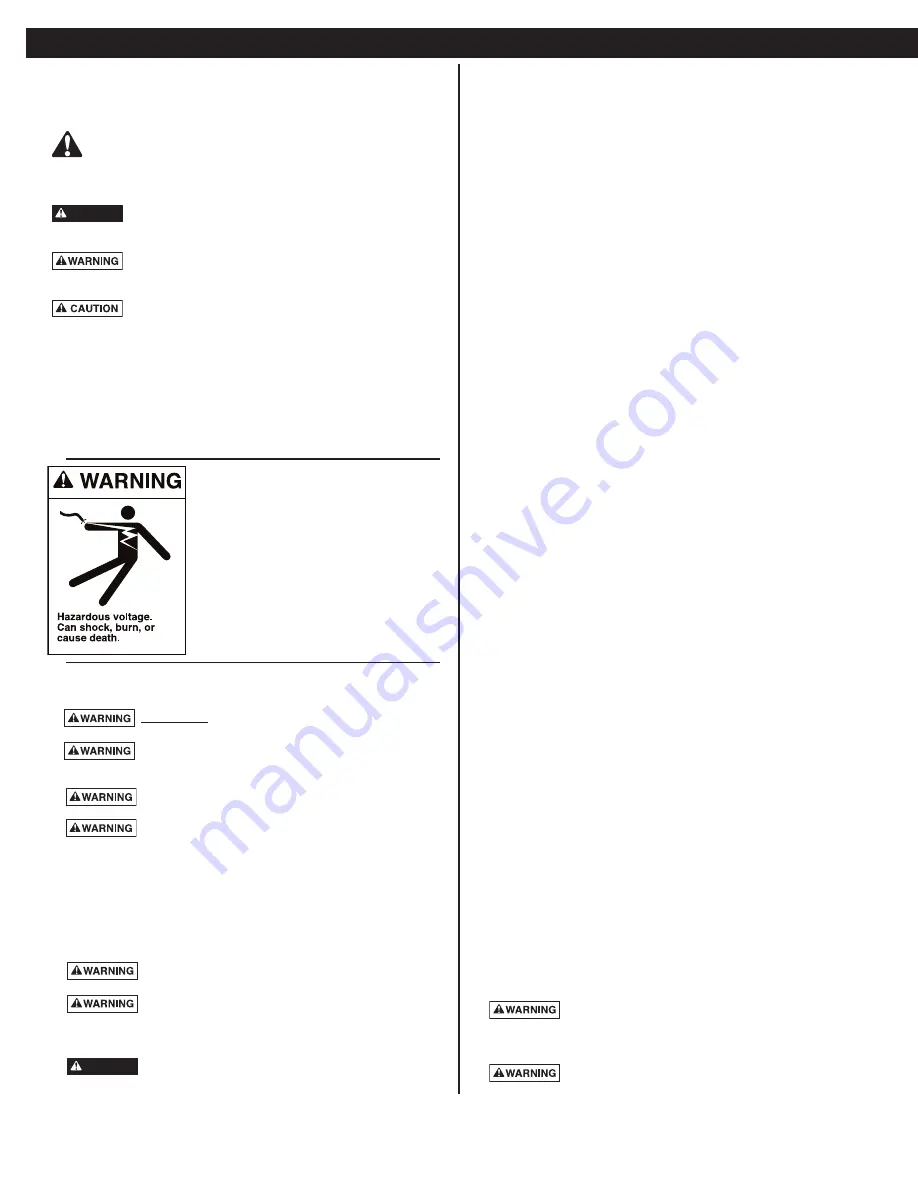
READ AND FOLLOW SAFETY
INSTRUCTIONS!
This is the safety alert symbol. When you see this
symbol on your pump or in this manual, look for one
of the following signal words and be alert to the potential for
personal injury.
warns about hazards that WILL cause serious
personal injury, death or major property damage if ignored.
warns about hazards that CAN cause serious
personal injury, death or major property damage if ignored.
warns about hazards that WILL or CAN cause
minor personal injury or property damage if ignored.
The label NOTICE indicates special instructions which are
important but not related to hazards.
MOTOR AND ELECTRICAL:
Carefully read and follow all safety instructions in this manual
and on pump.
GENERAL SAFETY – ELECTRICAL
1. Every time work is to be performed on a pump,
the power supply should be terminated at the breaker box.
2. Follow all local electrical and safety codes,
including the National Electrical Code (NEC) and the
Occupational Safety and Health Act (OSHA).
3. Replace damaged or worn cords immediately.
4. Ground motor before connecting to power supply.
5. Use extreme caution around an operating pump
and motor – it may be hot enough to cause serious burns.
GENERAL OPERATION – ELECTRICAL
1. Refer to motor nameplate to verify that supply voltage and
motor wiring is the same.
2. Verify motor phase against supply power phase.
GENERAL SAFETY – MOTOR
1. Disconnect the main power before handling the
unit for ANY REASON.
2. An operating motor can run between 250°F and
311°F depending on insulation rating. Never touch a motor
without first determining the housing temperature.
3. Keep pump motor ventilated to reduce damage due to heat.
4. Motor is not waterproof and should never be
submersed into any liquid.
5. Motor is designed to work with up to a 15 degree angle of
water impact. Do not allow water to spray directly onto
motor. External motor protection should be used to eliminate
environmental concerns.
6. To reduce the risk of electric shock, the motor must be
securely and adequately grounded. Refer to National
Electric Code (NEC Article 250 – Grounding) for additional
information.
7. When in doubt, call a licensed electrician. High voltage
can shock, burn or cause death.
WIRING CONNECTION:
ROTATION
1. When facing the suction tapping, all Munro pumps run in a
Counter-Clockwise (CCW) rotation only. Rotation from the
motor end perspective is Clockwise (CW) and is marked as
such on the motor nameplate. Tampering with, or reversing,
the rotation will damage your pump and void the warranty.
CHECK MOTOR ROTATION – 3 PHASE
1. A fractional second application of power should be applied to
all 3-phase motors to verify rotation of shaft as described
above. This is sometimes referred to as “bumping
the motor”.
2. Improper rotation can cause catastrophic pump failure
and voids the warranty.
3. Reversing two of the three power wires makes the motor run
in the opposite direction.
GENERAL WIRING INFORMATION
1. Refer to the connection diagram located on the nameplate
of the motor.
GROUNDING
1. Grounding the motor can be achieved by securing the
motor to a metal raceway system. Alternately a separate
grounding wire connected to bare metal on the motor
frame, or to the green grounding screw located inside the
motor terminal box, or other suitable means is acceptable.
(Refer to NEC Article 250 – Grounding for specifics.)
2. Verify motor grounding provision on the nameplate before
connecting any wires to the motor.
MOTOR PROTECTION
1.
Fuses and circuit breakers are used as a safety device for
the wire circuit. They do NOT offer motor protection.
2. Consult local or national electric codes for proper fuse
protection based on the motor data located on the motor
nameplate.
T HERMAL OVERLOAD
1. All motors must be thermally protected – either within the
motor or externally.
2. The internal overload is usually automatic and resets itself
once the temperature has dropped to a safe point.
3. Overload helps protect the motor from burnout from
overload of low voltage, high voltage and other causes.
4. Frequent tripping of the overload indicates motor or power
problems. Immediate professional attention is
recommended.
5. NEVER examine, make wiring changes or touch
the motor before disconnecting the electrical supply.
Thermal overload protectors automatically reset and can
close the electrical circuit without warning.
6. The overload should never be tampered with
or removed.
DANGER
Electric pump motors can be
hazardous if not properly installed.
Call a licensed electrician if unsure of
any electrical connection.
DANGER
10
Munro LP Series Pump
OPERATION & MAINTENANCE