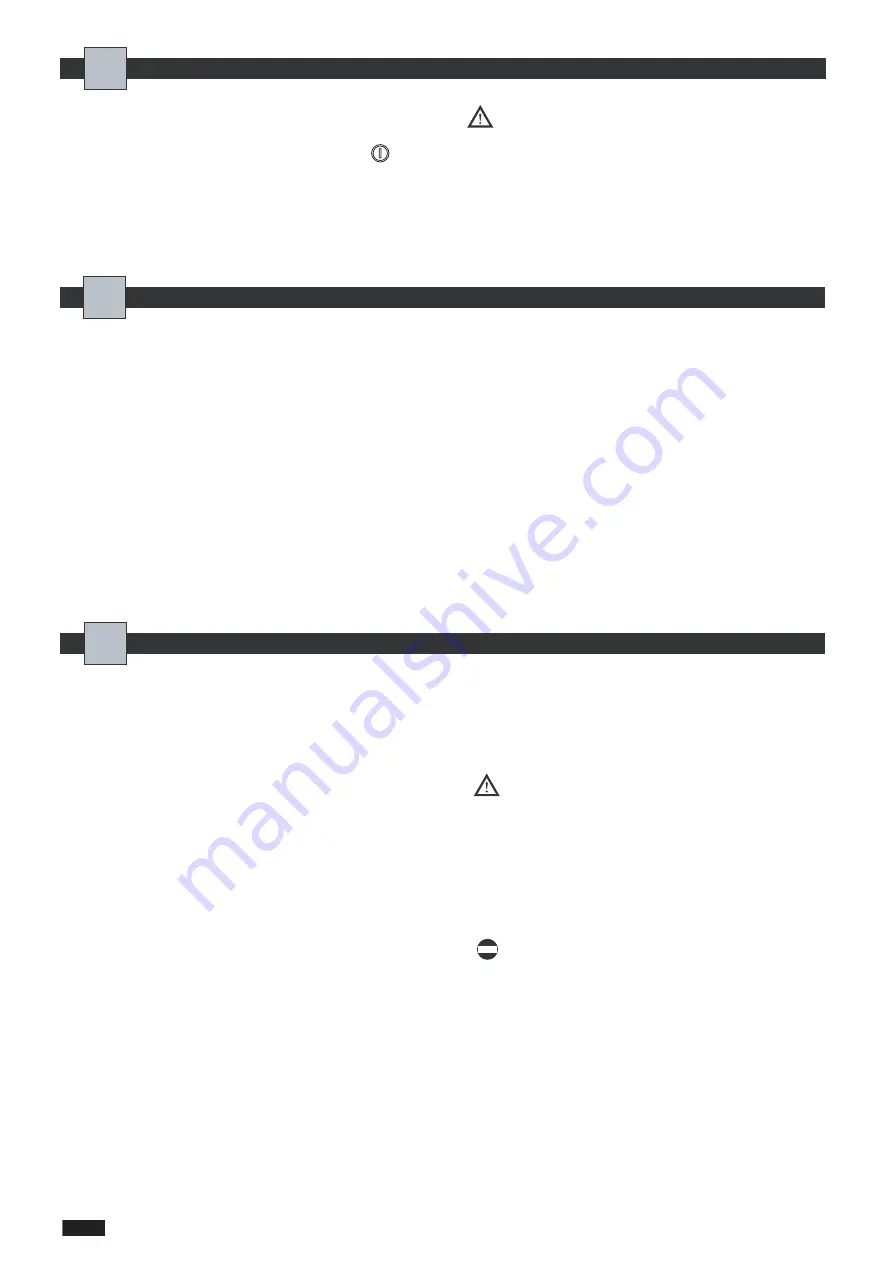
23
SHUTTING DOWN FOR LONG PERIODS
If it is previewed not to use the machine for long periods
After deactivating the chiller:
-Make sure the model is in the Power off model " ",
or alternatively disconnect the unit from the power supply.
-Make sure the remote control switch is closed (if present) .
-Close the water valves.
If there is a possibility that the outside temperature
may drop below zero,there is the risk of freezing.
The water circuit MUST BE EMPTIED AND SHUT
OFF POWER (when draining after heat pump
operation take care as the water may be hot)or
antifreeze must be added in the proportion
recommended by the manufacturer.
Never perform any cleaning operations before having
CHEMICAL WASHING
You are recommended to chemically wash the plate heat
exchanger after every 3 years of operation.
REFRIGERANT GAS CONTENT
The chillers are filled R410A refrigerant gas and tested in
the factory.In normal conditions,there should be no need
for the Technical Assistance Service to intervene to check
the refrigerant gas.However,over time,small leaks may
ROUTINE MAINTENANCE
Never perform any cleaning operations before having
disconnected the unit from the mains power supply.
If the supply cord is damaged, it must be replaced by the
manufacturer or its service agent or a similarly qualified
person in order to avoid a hazard.
Regular maintenance is fundamental to maintain the
efficiency of the unit both in terms of operation and energy
consumption.The Technical Assistance Service
maintenance plan must be observed,with an annual
service which includes the following operations and checks:
-Filling of the water circuit
-Presence of air bubbles in the water circuit
-Efficiency of safety devices
-Power supply voltage
-Power input
-Tightness of electrical and hydraulic connections
-Condition of the compressor contactor
-Efficiency of the plate heat exchanger heater
-Checking of operating pressure,superheating and
subcooling
-Efficiency of compressor heater
-Cleaning of finned coil (*)
-Cleaning of fan grills
-Cleaning of condensate drain pan (if installed).
(*) for “Heat pump” appliances,the checks are to be
performed quarterly.
For units installed near the sea,the intervals between
maintenance should be halved.
EXTRAORDINARY MAINTENANCE
A
A
A
disconnected the unit from the mains power supply.
Draining of the circuit,causing the unit to function poorly. In this
case, the leaks of refrigerant must be identified and repaired
and the refrigerant circuit refilled.Proceed as follows
- Empty and dry the entire refrigerant circuit using a
vacuum pump connected to the low and high pressure
tap until the vacuometer reads about 10 Pa.Wait a couple
of minutes and check that this value does not rise to more
than 200 Pa.
-Connect the refrigerant gas cylinder or a filling cylinder
to the low pressure line pressure gauge connection.
-Fill with the quantity of refrigerant gas indicated on the
rating plate of the unit..
-Always check the superheating and subcooling values.In
the nominal operating conditions for the appliance,these
should be between 5 and 10°C and between 4 and 8°C
respectively.
-After a couple of hours of operation,check that the liquid
indicator indicates circuit dry (dry-green)
In the event of partial leaks,the circuit must be
completely emptied before being refilled.
The R410a refrigerant must only be filled in the
liquid state.
Operating conditions other than nominal conditions
may produce considerably different values.
Seal testing or identification of leaks must only be
carried out using R410a refrigerant gas, checking
with a suitable leak detector.
The refrigerant circuit must not be filled with a
refrigerant other than that indicated on page 14.
The use of a different refrigerant may cause serious
damage to the compressor.
Oxygen,acetylene or other inflammable or
poisonous gases must never be used in the refrige-
rant circuit as they may cause explosion or poiso-
ning.
Oils other than those indicated on pages 14 must
not be used.The use of different oils may cause
serious damage to the compressor.