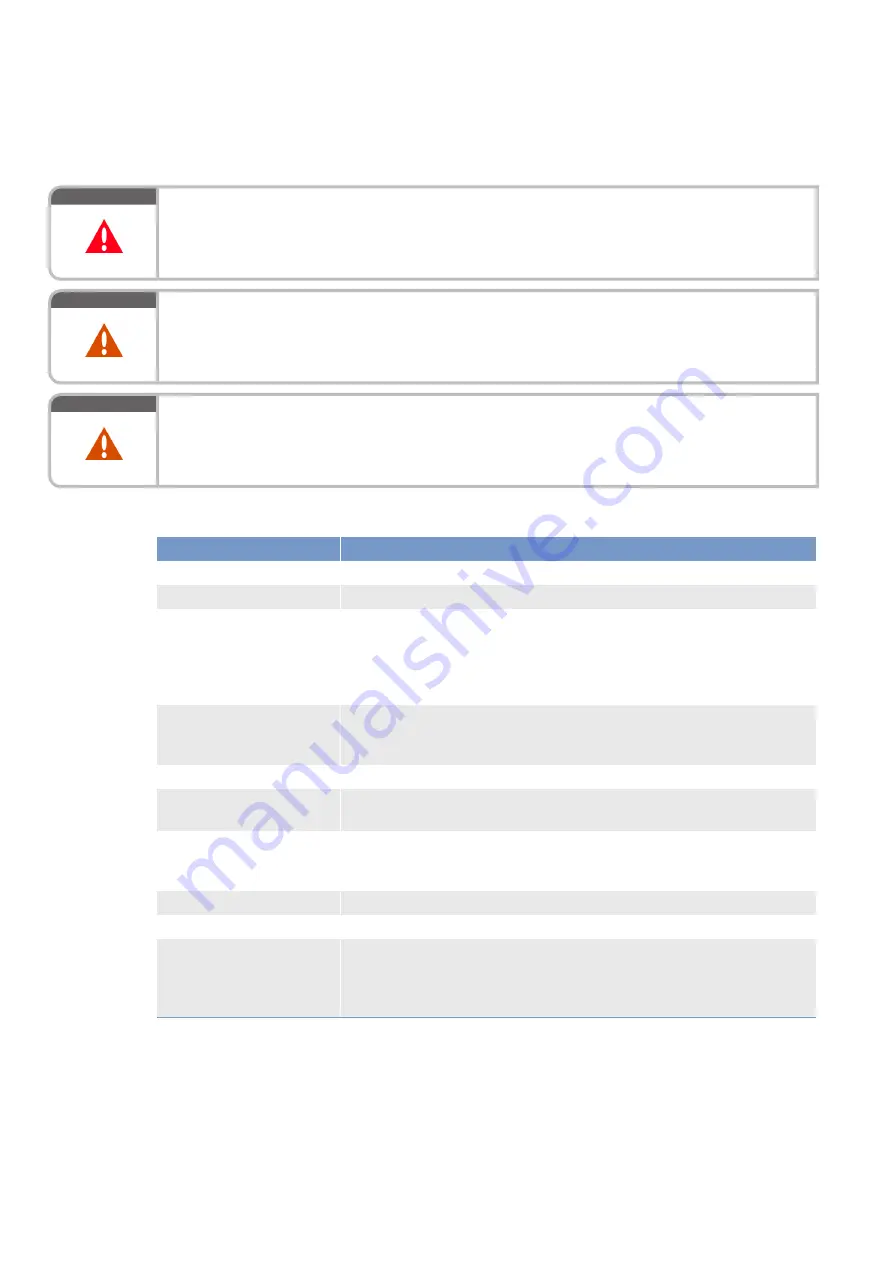
6.6 Operational monitoring
DANGER
Components are moving or rotating.
Risk of crushing, danger of parts of the body being caught or pulled in!
• Operate the engine at low load only. Keep clear of the danger zone of the engine.
WARNING
Exhaust gases are harmful to health and may cause cancer.
Risk of poisoning and suffocation!
• Keep the engine room well-ventilated at all times.
• Repair leaking exhaust pipework immediately.
WARNING
A high level of noise is produced when the engine is running.
Risk of hearing loss!
• Wear suitable hearing protection.
Operational monitoring
Item
Action
Control and display panels
Check readings of operational data (speed, temperature, pressures).
Engine oil
Check engine oil level (→ Page 177).
Engine under load
Engine at nominal speed
Check engine/plant and piping for leaks, repair leaky pipes with the engine
stopped (exhaust lines and turbocharger turbine housings may be red-hot. If
the maximum exhaust temperatures are not exceeded, no restrictions in en-
gine operation are required)
Check for abnormal running noises and vibration.
Fuel prefilter
Check reading on differential pressure gauge to ensure that maximum per-
missible value is not exceeded (→ Page 154).
Drain water and contaminants from fuel prefilter (→ Page 158), (→ Page 155).
Exhaust system
Check exhaust color (→ Page 85).
Intercooler
Check condensate drain(s) for water discharge and obstruction
(→ Page 169).
Air filter
Check signal ring position of contamination indicator (→ Page 173).
Replace air filter (→ Page 170) if the signal ring is completely visible in the
contamination indicator control window.
Engine coolant pump
Check relief bore (→ Page 192).
Charge-air coolant pump
Check relief bore (→ Page 215).
Compressed-air system (if
installed)
Check operating pressure on pressure gauge;
Always fill compressed-air tank to max. pressure;
Drain condensate from compressed-air tank, pressure drop must not exceed
1 bar.
76 | Operation | MS15060/01E 2018-12
TIM-ID: 0000073489 - 003