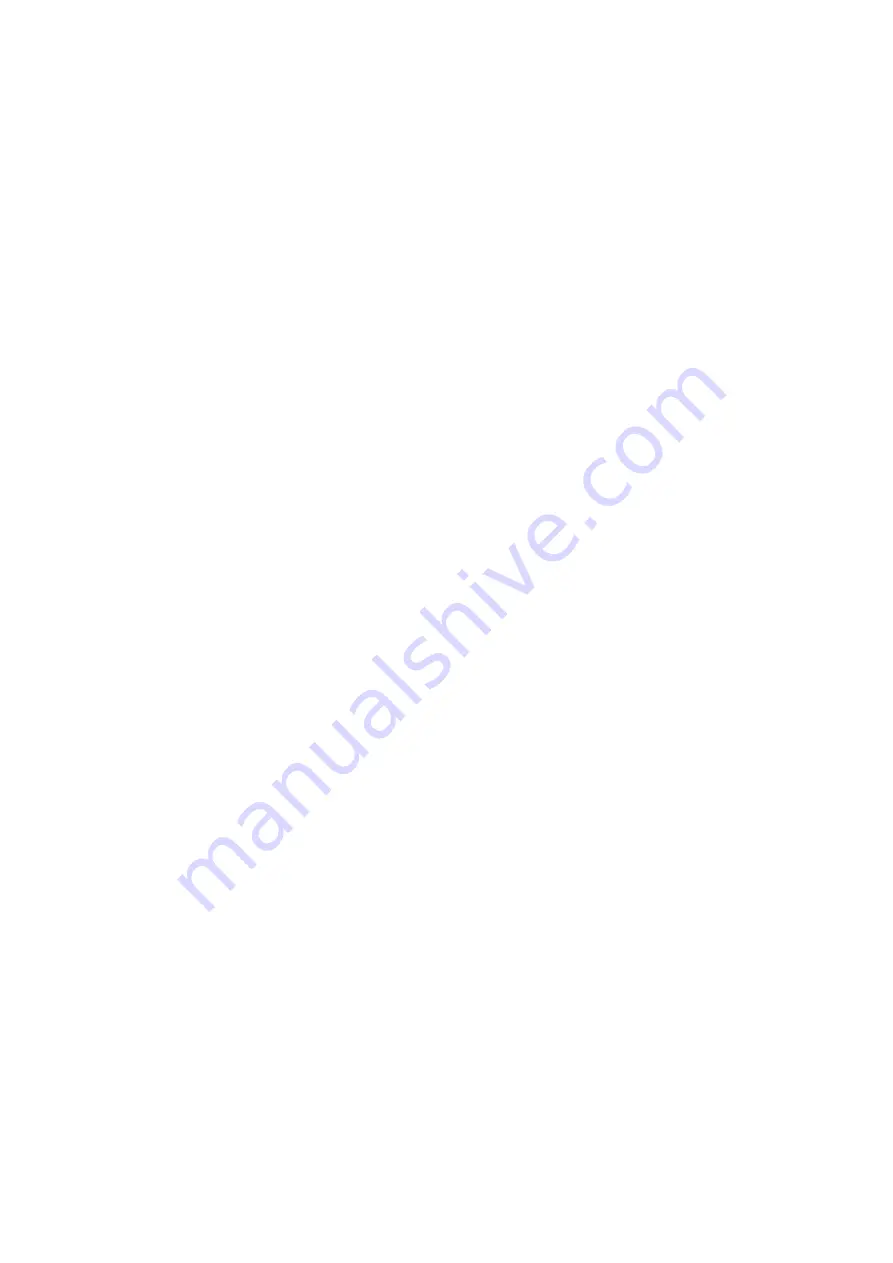
Contents
1. Safety and operation instructions
....................................................................................................................................
2. Product description and technology
.................................................................................................................................
3. Space requirements - conditions, design
3.1 Dimensions, tolerances...................................................................................................................................................
3.2 Chamfered edge for insertion..........................................................................................................................................
3.3 Pistion rod bore and depth..............................................................................................................................................
3.4 CAD-data, download........................................................................................................................................................
3.5 Installing the magnet.......................................................................................................................................................
3.5.1 Magnet with 2 distant washers...................................................................................................................
3.5.2 Magnet with 1 distant washer.....................................................................................................................
3.5.3 Installing the magnet..................................................................................................................................
3.6 Safety screw to DIN 913..................................................................................................................................................
3.7 Supporting long sensor pipes, sagging...........................................................................................................................
4. Mounting
4.1 Positionining of O- and backup rings..................................................................................................................................
4.2 Load-bearings geometries of sensor housing.................................................................................................................
4.3 Mounting in the cylinder..................................................................................................................................................
4.4 Handling connection cables during mounting..................................................................................................................
4.5 Mounting sensors using a Temposonics
®
M12 connector system..................................................................................
4.6 Mounting in the cylinder..................................................................................................................................................
4.7 Mounting sensors with cable or single conductor connection.........................................................................................
4.7.1 Mounting sensors with cable connection and cable gland...........................................................................
4.7.2 Mounting sensors with single conductor and third-party connector...........................................................
5. Cylinder handling after sensor installation
5.1 Washing and drying cylinders with installed sensors......................................................................................................
5.1.1 Sensors with Temposonics
®
M12 connector system..................................................................................
5.1.2 Sensors with connecting cable...................................................................................................................
5.1.3 Sensors with third-party connectors..........................................................................................................
5.2 Painting of cylinders............................................................................................................................................................
5.2.1 Electrostatic painting..................................................................................................................................
5.2.2 Cylinders with integrated sensors and Temposonics
®
M12 connector system...........................................
5.2.3 Cylinders with integrated sensors and connecting cables or third-party connectors..................................
6. Transport, intermediate storage
6.1 Mounting/dismounting cylinders on mobile hydraulics machines...................................................................................
6.2 Electrical and electrostatic effects...................................................................................................................................
6.3 Electrostatic effects.........................................................................................................................................................
7. Drawings
7.1 Dimensions of Temposonics
®
MH sensor
- with M12 connector system..............................................................................................................................
- with single wires...............................................................................................................................................
- with cable..........................................................................................................................................................
- with cable (till 03.2011).....................................................................................................................................
7.2 Dimensions of Temposonics
®
MS sensor
- with M12 connector system..............................................................................................................................
- with single wires...............................................................................................................................................
- with cable..........................................................................................................................................................
7.3 Dimensions of Temposonics
®
MT sensor
- with M12 connector system..............................................................................................................................
- with single wires...............................................................................................................................................
- with cable..........................................................................................................................................................
7.4 Dimensions of sensor magnets (position transducer) ....................................................................................................
7.5 Mounting sensors using Temposonics
®
M12 connector system (flange)........................................................................
7.6 Dimensions of turned parts made of M12 round material................................................................................................
3
4
5
6
6
6
7
7
7
8
8
9
10
10
11
13
14
14
16
16
16
17
17
17
17
18
18
19
19
20
20
21
22
23
24
25
26
27
28
29
30
31
32
33
34
Summary of Contents for Temposonics MH Series
Page 35: ......