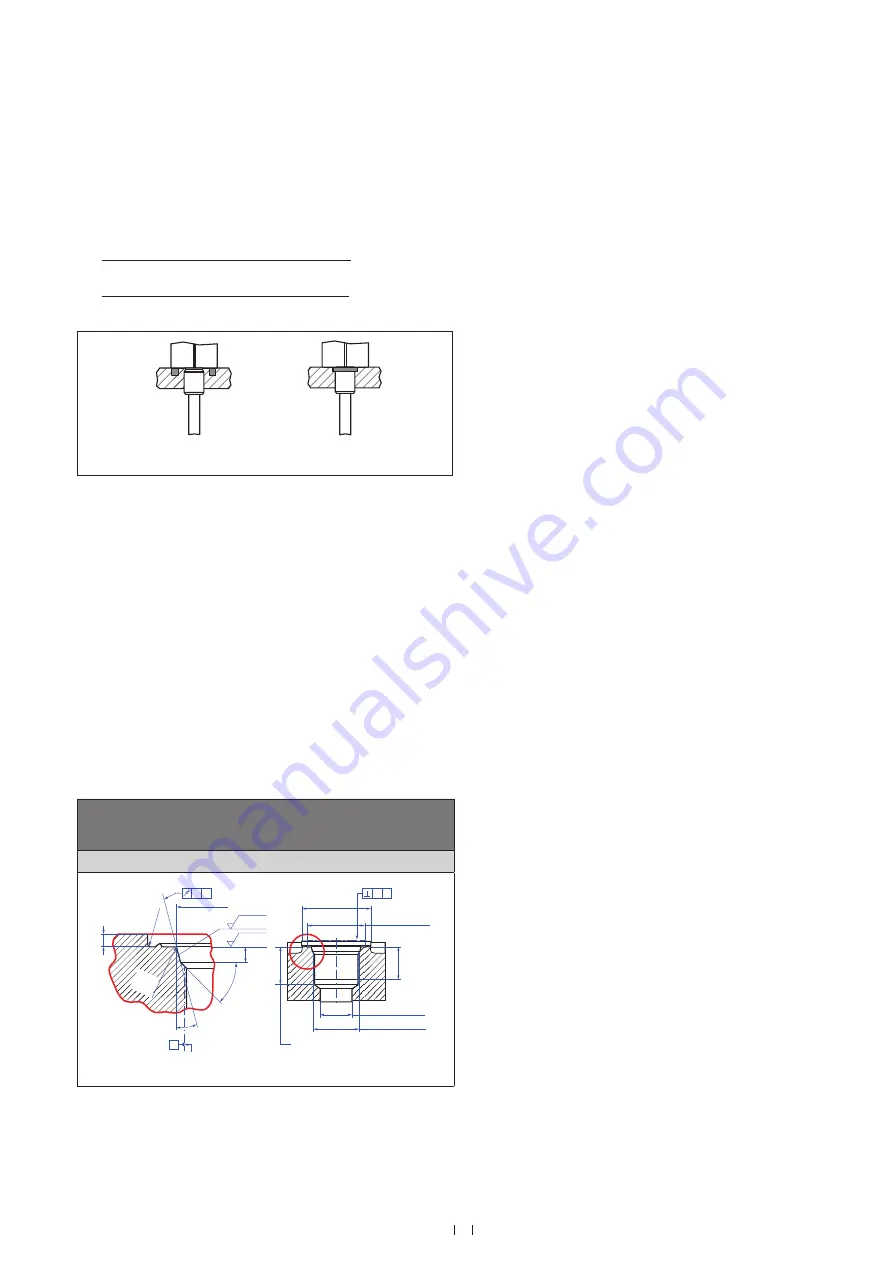
9
Temposonics
®
ET Analog ATEX / IECEx / CEC / NEC / CCC Certified
Operation Manual
Hydraulics sealing
There are two ways to seal the flange contact surface (Fig. 7):
1. A sealing by using an O-ring (e.g. 22.4 × 2.65 mm (0.88 × 0.1 in.),
25.07 × 2.62 mm (0.99 × 0.1 in.)) in a cylinder end cap groove.
2. A sealing by using an O-ring in the undercut.
For threaded flange (¾"-16 UNF-3A) »F« / »S«:
O-ring 16.4 × 2.2 mm (0.65 × 0.09 in.) (part no. 560 315)
For threaded flange (M18×1.5-6g) »M« / »W«:
O-ring 15.3 × 2.2 mm (0.60 × 0.09 in.) (part no. 401 133)
Fig. 7: Possibilities of sealing
• Note the fastening torque of 75 Nm.
• Seat the flange contact surface completely on the cylinder mounting
surface.
• The cylinder manufacturer determines the pressure-resistant
gasket (copper gasket, O-ring, etc.).
• The position magnet should not grind on the sensor rod.
• The piston rod drilling (≥ Ø 13 mm (≥ Ø 0.51 in.)) depends on the
pressure and piston speed.
• Adhere to the information relating to operating pressure.
• Protect the sensor rod against wear.
Fig. 8: Notice for metric threaded flange M18×1.5-6g based on DIN ISO 6149-1
Thread
(d
1
×P)
d
2
d
3
d
4
d
5
+0.1
0
L
1
+0.4
0
L
2
L
3
L
4
Z°
±1°
M18×1.5-6g
55 ≥ 13 24.5 19.8 2.4 28 2 ≥ 25.5 15°
All dimensions in mm
Ød
5
Ra 3.2
Ra 3.2
Pitch diameter
A
A
Thread
(d
1
× P)
Ød
3
(Reference)
A
Ød
2
Ød
4
(Gauging)
This dimension applies when
tap drill cannot pass through
entire boss.
≤ R0.4
R0.3 R0.1
Z°
45
° ±
5°
L
3
L
1
L
2
L
4
A
0.1
A
0.2
Notice for metric threaded flanges
In the case of threaded flange M18×1.5-6g provide a screw hole based on
ISO 6149-1 (Fig. 8). See ISO 6149-1 for further information.
Sealing via O-ring
in the flange undercut
Sealing via O-ring
in cylinder end cap groove
Summary of Contents for Temposonics E Series
Page 32: ......