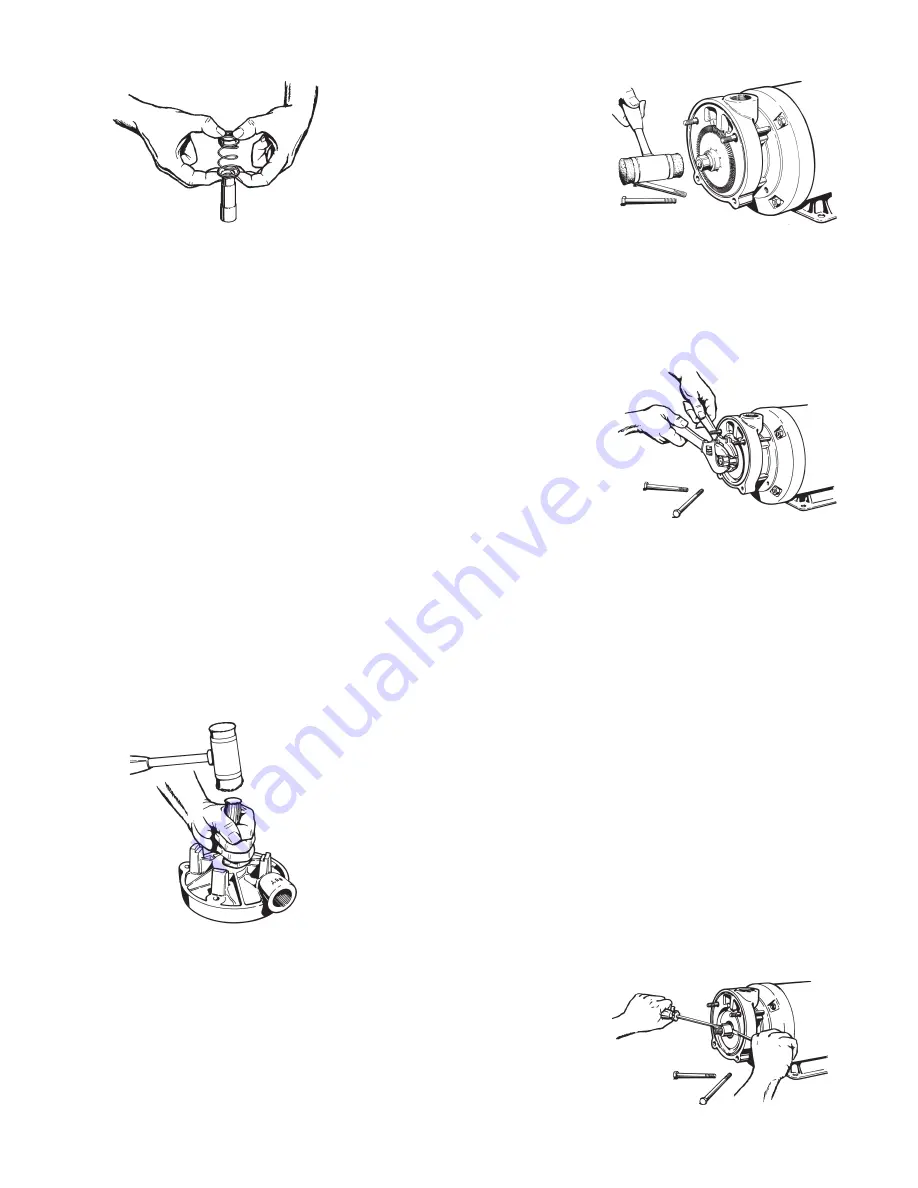
Figure 4-3
Section
T51 • E51
Page 509
Dated
February 2014
reassembly.
DO NOT attempt to
remove the seal using a screw-
driver or other sharp object.
Extensive damage to the shaft,
sleeve, or element could occur.
9. Before the motor bracket (#1) can
be removed, the four (4) “O”rings
(#8), located on the upper left and
right studs must be removed.
a. Gently tap on the back of the
motor bracket, alternating
between the left and right side,
until the motor bracket moves
approximately 1/4”.
b. Tap the motor bracket face to
move it back to its original posi-
tion.
c. Remove the “O” rings by sliding
them off the studs.
d. Slide the motor bracket straight
off. Do not attempt to remove
the motor bracket without first
removing the “O” rings (#8).
10.Remove the seat portion of the
seal, Refer to Figure 4-6.
d. Care must be taken with
the seats. They are often a
brittle material and are prone to
breakage.
It is
recommended
that a new replacement seat
be installed during reassem-
bly.
11.It is not necessary to remove the
locking collar (#14) on the motor
shaft unless motor repairs are
planned. Note the condition of the
setscrew in the collar and replce
if necessary. The two studs (#18)
may also be left in the motor face.
4C Disassembly (C15 and P15)
The following tools and equipment
are needed for disassembly of C15
and P15 units:
1. Soft plastic or wooden mallet.
2. 9/16” wrench or socket.
3. Two 10” or larger adjustable
wrenches.
4. Penetrating oil.
5. 1” wood dowel ( Approx. 6” long).
6. Thin blade screwdriver.
7. Two large blade screwdrivers.
8. Cealube G or similar glycol base
lubricant. (DO NOT use petroleum
products.)
To disassemble the pump:
Refer to Figures 4-11 and 4-12 for
reference to the numbered parts in
the disassembly below.
1. Remove all liquid from the pump.
2. Remove the two (2) 3/8” nuts
(#20), and the two (2) 3/8” X 4”
bolts (# 19) from the cover. (#2)
3. Remove the cover. In some
cases, light tapping with a plastic
or wooden mallet on the outside
diameter of the cover may be
required to loosen it from the
motor bracket. Care should be
taken if a screwdriver is needed to
pry between the cover and motor
bracket. Damage to the “O” ring
(#7) and/or impeller can result.
4. Remove the impeller (#11), refer
to Figure 4-7. The impeller is a
slip fit and, under normal condi
-
tions, can be removed by gently
tapping on the end of the shaft
sleeve with a mallet. Leave the
impeller key (#23) in place. Strik-
Figure 4-7
Figure 4-6
a. Place the motor bracket face
down on a flat surface.
b. Look into the opening in the
center of the bracket, you will
see a portion of the seat.
c. Insert the 1” dowel and, very
gently, tap the seat until it drops
out.
ing the sleeve too hard could
damage the seat or rotating ele-
ment.
5. Remove the impeller drive hub,
Refer to Figure 4-8. Two (2)
adjustable wrenches are used
to remove the impeller drive hub
(#14).
Figure 4-8
a. Adjust one wrench to fit over
the sleeve and engage the
impeller key. Adjust the second
wrench to fit the impeller nut
(#15).
b. Holding both wrenches, turn the
impeller nut counter-clockwise.
c. After the impeller nut is re-
moved, the impeller drive hub
can be removed.
d. The hub is keyed and can be
removed using two large bladed
screwdrivers.
e. Insert the blades of the screw-
drivers between the spring
holder on the rotating element
and the shoulder of the hub.
f. Holding the screwdrivers at
approximately 3 o’clock and
9 o’clock, push the handles in
toward the motor body, using
the motor bracket for leverage.
Refer to Figure 4-9. This pro-
Figure 4-9