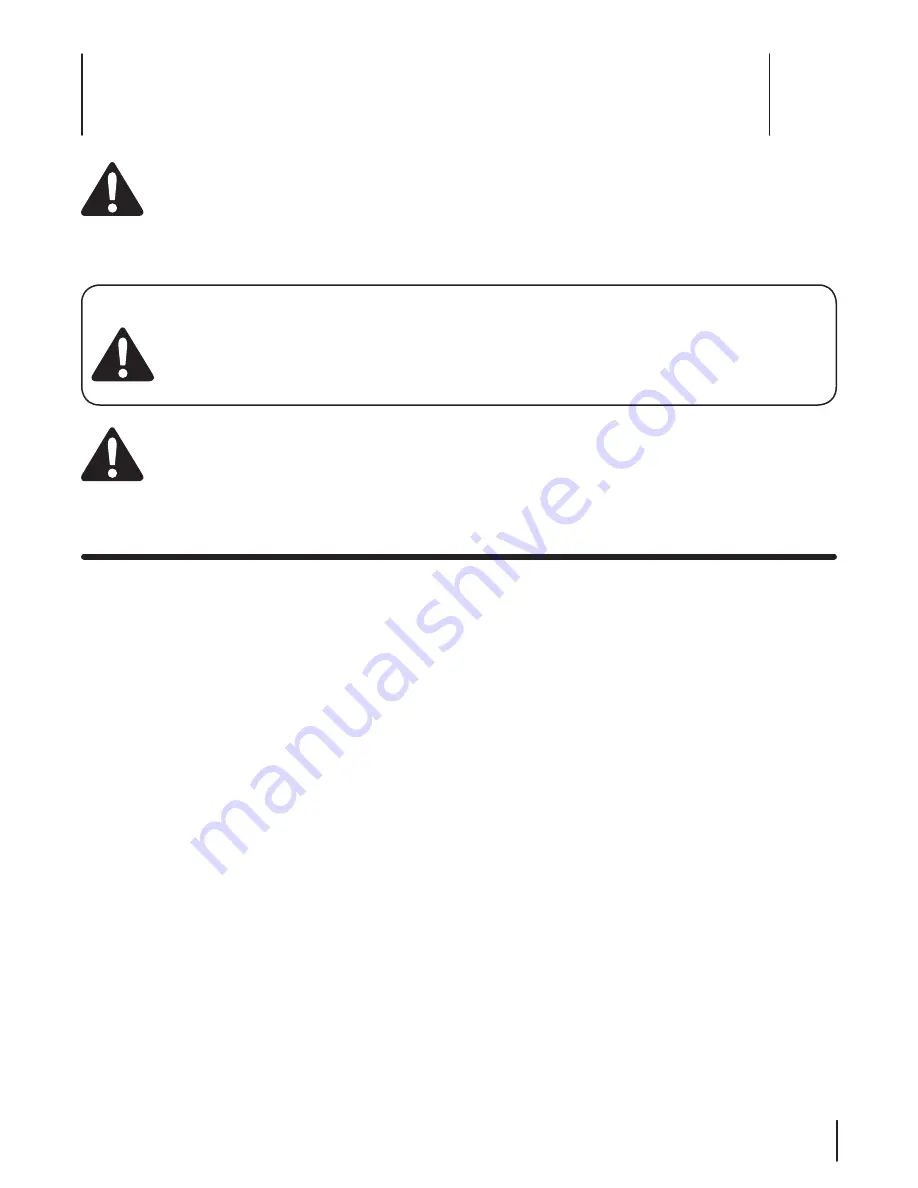
Important Safe Operation Practices
2
3
Training
1.
Read, understand, and follow all instructions on the
machine and in the manual(s) before attempting to
assemble and operate. Keep this manual in a safe place for
future and regular reference and for ordering replacement
parts.
2.
Be familiar with all controls and their proper operation.
Know how to stop the machine and disengage them
quickly.
3.
Never allow children under 16 years of age to operate this
machine. Children 16 and over should read and understand
the instructions and safe operation practices in this manual
and on the machine and be trained and supervised by an
adult.
4.
Never allow adults to operate this machine without proper
instruction.
5.
Keep bystanders, pets, and children at least 75 feet from
the machine while it is in operation. Stop machine if
anyone enters the area.
6.
Never run an engine indoors or in a poorly ventilated area.
Engine exhaust contains carbon monoxide, an odorless
and deadly gas.
7.
Do not put hands and feet near rotating parts or in the
feeding chambers and discharge opening. Contact with
the rotating impeller can amputate fingers, hands, and
feet.
8.
Never attempt to unclog either the feed intake or discharge
opening, remove or empty bag, or inspect and repair the
machine while the engine is running. Shut the engine off
and wait until all moving parts have come to a complete
stop. Disconnect the spark plug wire and ground it against
the engine.
Preparation
1.
Thoroughly inspect the area where the equipment is to
be used. Remove all rocks, bottles, cans, or other foreign
objects which could be picked up or thrown and cause
personal injury or damage to the machine.
2.
Always wear safety glasses or safety goggles during
operation and while performing an adjustment or repair,
to protect your eyes. Thrown objects which ricochet can
cause serious injury to the eyes.
3.
Wear sturdy, rough-soled work shoes and close-fitting
slacks and shirts. Loose fitting clothes or jewelry can be
caught in movable parts. Never operate this machine
in bare feet or sandals. Wear leather work gloves when
feeding material in the chipper chute.
4.
Before starting, check all bolts and screws for proper
tightness to be sure the machine is in safe working
condition. Also, visually inspect machine for any damage at
frequent intervals.
5.
Maintain or replace safety and instructions labels, as
necessary.
WARNING:
This symbol points out important safety instructions which, if not followed,
could endanger the personal safety and/or property of yourself and others. Read and follow
all instructions in this manual before attempting to operate this machine. Failure to comply
with these instructions may result in personal injury.
When you see this symbol.
HEED ITS WARNING!
DANGER:
This machine was built to be operated according to the safe operation practices in
this manual. As with any type of power equipment, carelessness or error on the part of the
operator can result in serious injury. This machine is capable of amputating fingers, hands,
toes and feet and throwing debris. Failure to observe the following safety instructions could
result in serious injury or death.
CALIFORNIA PROPOSITION 65
WARNING:
Engine Exhaust, some of its constituents, and certain vehicle components
contain or emit chemicals known to State of California to cause cancer and birth defects
or other reproductive harm.
Summary of Contents for 452J Series
Page 19: ...Notes 10 19 ...