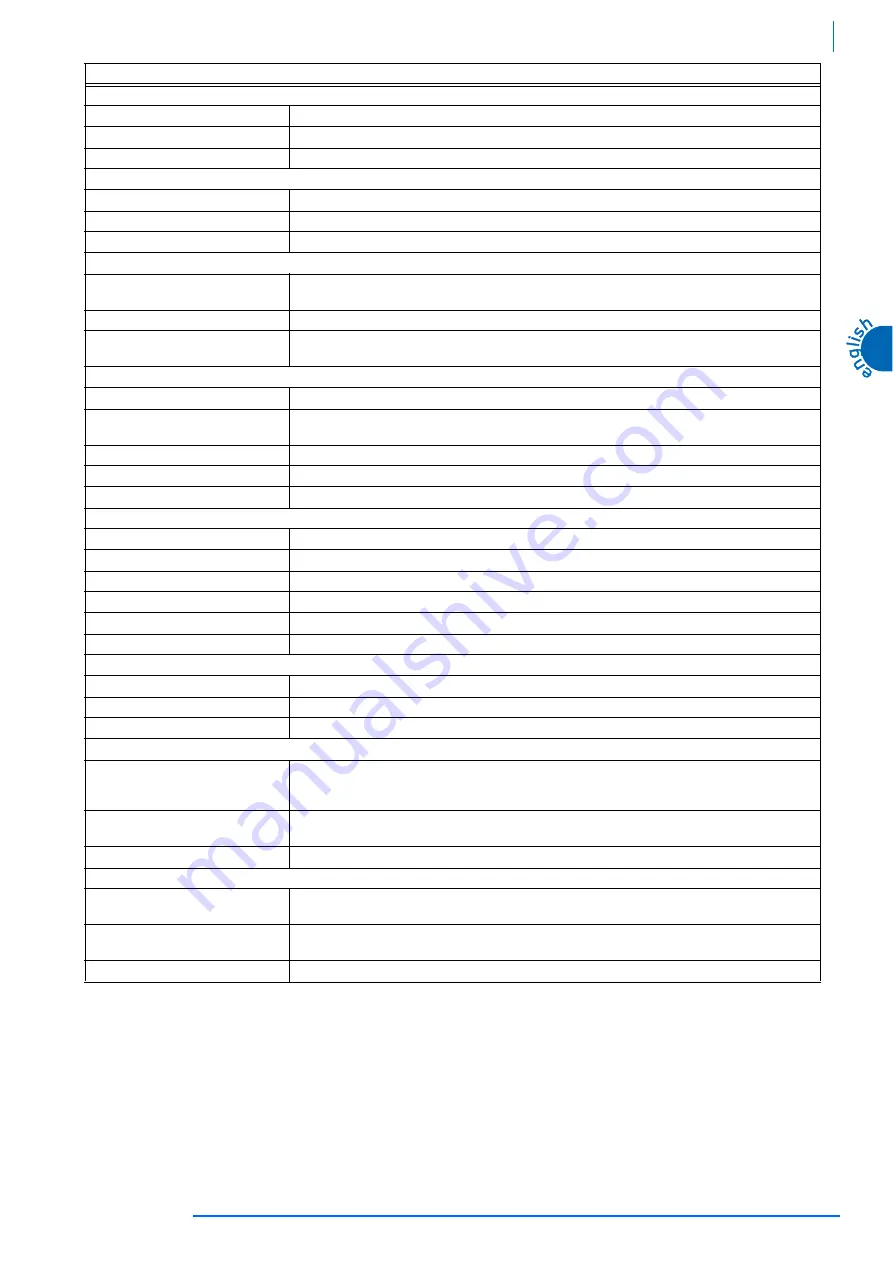
TAEevo M05-M10
5
MAINTENANCE AND OPERATING MANUAL
The data inside this manual are not binding and they can be modified by the manufacturer without notice.
All rights reserved.
FIRE-FIGHTING MEASURES
Means of extinction:
Any means
Specific dangers:
Pressure increase
Specific methods:
Cool the containers with water sprays
MEASURES IN THE EVENT OF ACCIDENTAL LEAKAGE
Individual precautions:
Evacuate personnel to safe areas. Provide adequate ventilation. Use means of personal protection
Environmental precautions:
Evaporates
Cleaning methods:
Evaporates
HANDLING AND STORAGE
Handling
technical measures/ precautions:
Ensure sufficient air change and/or extraction in the work areas
recommendations for safe use:
Do not inhale vapours or aerosols
Storage:
Close properly and store in a cool, dry well-ventilated place. Store in its original containers.
Incompatible products: explosives, flammable materials, organic peroxide
CONTROL OF EXPOSURE/INDIVIDUAL PROTECTION
Control parameters:
AEL (8-h e 12-h TWA) = 1000 ml/m3 for each of the three components
Respiratory protection:
For rescue and maintenance work in tanks, use autonomous breathing apparatus. The vapours are
heavier than air and can cause suffocation, reducing the oxygen available for breathing
Protection of the eyes:
Safety goggles
Protection of the hands:
Rubber gloves
Hygiene measures:
Do not smoke
PHYSICAL AND CHEMICAL PROPERTIES
Colour:
Colourless
Odour:
Similar to ether
Boiling point:
-43.9°C / -47.0°F at atm. press.
Flammability point:
Non flammable
Relative density:
1.138 kg/l at 25°C
Solubility in water:
Negligible
STABILITY AND REACTIVITY
Stability:
No reactivity if used with the relative instructions
Materials to avoid:
Alkaline metal, earthy alkaline metals, granulated metals salts, Al, Zn, Be, etc. in powder.
Hazardous decomposition products:
Halogen acids, traces of carbonyl halides
TOXICOLOGICAL INFORMATION
Acute toxicity:
(R32) LC50/inhalation/4 hours/lab. rats >760 ml/l
(R125) LC50/inhalation/4 hours/lab. rats >3480 mg/l
(R134a) ALC/inhalation/4 hours/lab. rats = 567 ml/l
Local effects:
Concentrations substantially above the TLV can cause narcotic effects. Inhalation of products in
decomposition can lead to respiratory difficulty (pulmonary oedema)
Long-term toxicity:
Has not shown any cancerogenic, teratogenic or mutagenic effects in experiments on animals
ECOLOGICAL INFORMATION
Global warming potential HGWP
(R11=1):
R125: 0.84 - R134a: 0.28
Ozone depletion potential ODP
(R11=1):
0
Considerations on disposal:
Usable with reconditioning
R407C