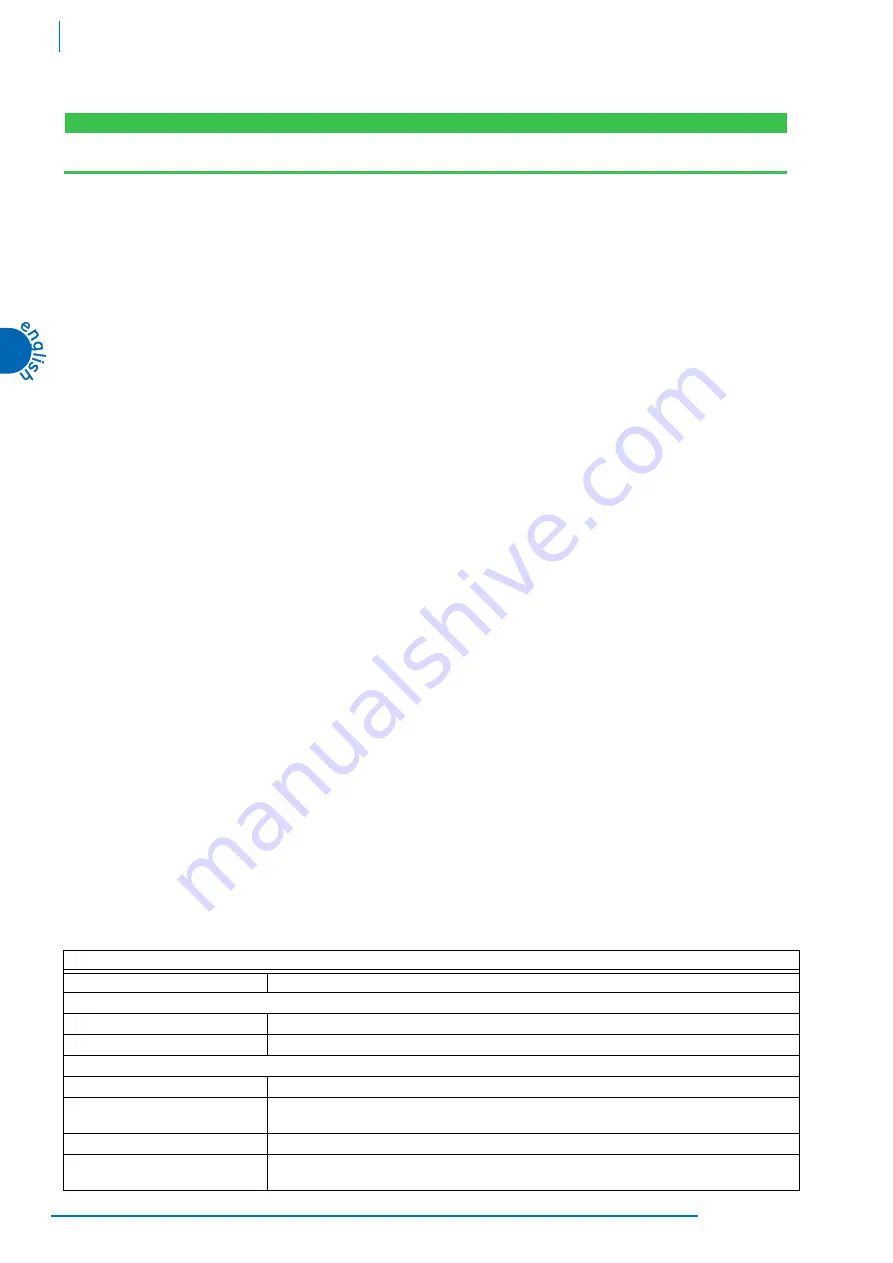
TAEevo M05-M10
4
The data inside this manual are not binding and they can be modified by the manufacturer without notice.
All rights reserved.
2.2.5 Maintenance and repair precautions
Maintenance, overhaul and repair work must be carried out by competent personnel under a qualified supervisor.
ATTENTION
When disposing of parts and waste material of any kind make sure that there is no pollution of any drain or natural water-course and that no
burning of waste takes place which could cause pollution of the air. Protect the environment by using only approved methods of disposal.
If replacement parts are needed use only original spares.
Keep a written record of all maintenance and repair work carried out on the unit and auxiliary equipment. The frequency and the nature of the
work required over a period can reveal adverse operating conditions which should be corrected.
Use only refrigerant gas specified on the plate of the unit.
Make sure that all instructions concerning operation and maintenance are strictly followed and that the complete unit, with all accessories and
safety devices, is kept in good working order.
The accuracy of temperature/pressure measuring devices must be checked regularly; renew measuring devices when the measurement tolerance
is outside the specified range of values.
Keep the machine clean at all times. Protect components and exposed openings by covering them, for example, with clean cloth or tape during
maintenance and repair work.
Do not weld or carry out any operation which produces heat near a system which contains oil or flammable liquids. The systems which may
contain oil or flammable liquids must be completely drained and cleaned (with steam, for example), before carrying out these operations. Never
weld, nor modify in any way, a vessel which may be put under pressure.
To prevent an increase in working temperature and pressure, inspect and clean heat transfer surfaces (i.e. condenser fins) regularly. For every
unit establish a suitable time schedule for cleaning operations.
Avoid damage to safety valves and other pressure relief devices. Avoid plugging by paint, oil or dirt accumulation.
Precautions must be taken when carrying out welding or any repair operation which generates heat, flames or sparks. The adjacent components
must always be screened with non-flammable material and if the operation is to be carried out near any part of the lubrication system, or close to
a component which may contain oil, the system must first be thoroughly purged, preferably by steam cleaning.
Never use a light source with an open flame to inspect any part of the machine.
Before dismantling any part of the unit ensure that all heavy movable parts are secured.
When a repair has been completed, make sure no tools, loose parts or rags are left in, or on the machine.
All guards must be reinstated after carrying out repair or maintenance work.
Do not use flammable liquid to clean any component during operation.
If chlorinated hydrocarbon non-flammable fluids are used for
cleaning, safety precautions must be taken against any toxic vapours which may be released.
Before removing any panels or dismantling any part of the unit, carry out the following operations:
• Isolate the
chille
r unit from the main electrical power supply by disconnecting the cable from the electrical power source.
Lock the isolator in the “OFF” position with a lock.
•
Attach a warning label to the main isolator switch conveying: “WORK IN PROGRESS - DON NOT APPLY VOLTAGE”. Do
not switch on electrical power or attempt to start the unit if a warning label is attached.
Coloured tracers can be used in service-maintenance operations.
Inspect all refrigerant circuit joints including connectors, flanges, and more generally all critical points (open joints) in order to prevent possible
leakage of refrigerant gas.
2.2.6 Refrigerant gases
R407C is used as refrigerant in these units.
Never attempt to mix refrigerant gases.
To clean out a very heavily contaminated refrigerant system, e.g. after a refrigerant compressor burnout, a qualified refrigeration engineer must
be consulted to carry out the task.
The manufacturer's instructions and local safety regulations should always be observed when handling and storing high pressure gas cylinders.
2 . 3
S a f e t y s c h e d u l e
R407C
Denomination:
23% Difluoromethane (R32); 25% Pentafluoroethane (R125); 52% R134a
INDICATION OF THE DANGERS
Major dangers:
Asphyxia
Specific dangers:
Rapid evaporation can cause freezing
FIRST AID MEASURES
General information:
Do not give anything to unconscious persons
Inhalation:
Take the person outdoors. Use oxygen or artificial respiration if necessary. Do not administer
adrenaline or similar substances
Contact with the eyes:
Thoroughly wash with plenty of water for at least 15 minutes and call a doctor
Contact with the skin:
Wash immediately with plenty of water.
Remove contaminated clothing immediately