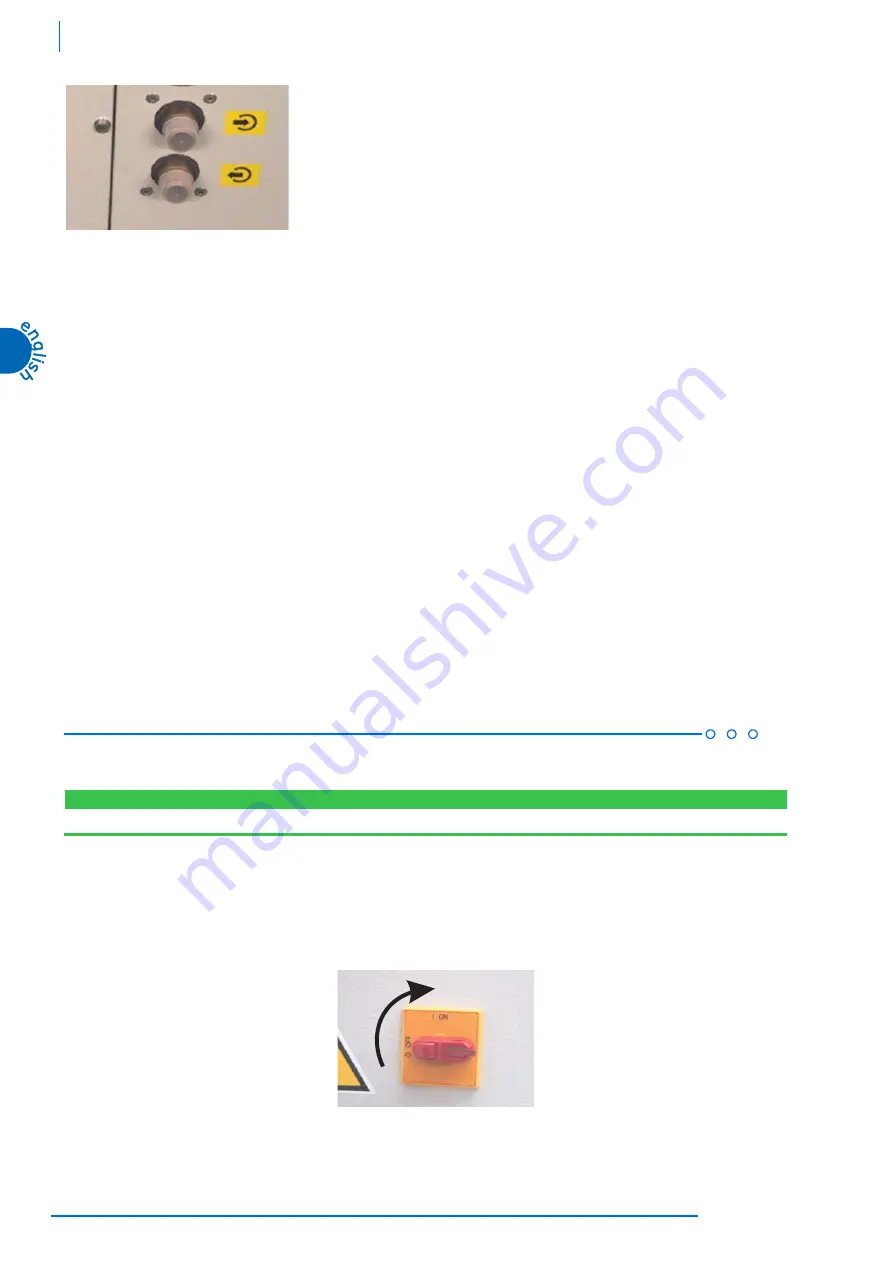
TAEevo M05-M10
10
The data inside this manual are not binding and they can be modified by the manufacturer without notice.
All rights reserved.
5 . 4 P l u m b i n g c o n n e c t i o n s
It is recommended to insert a filter of “Y” type on the water inlet connection, in order to stop
eventual impurities of water which could cause big damages to the pump.
1.
Connect the
chille
r to the water piping. See the overall dimension drawings for the size and
type of connections.
2.
Provide two cocks (inlet and outlet) to by-pass the machine for maintenance purposes without
having to empty the water circuit of the user.
3.
Fill the water receptacle by unscrewing the plug of the receptacle and filling the circuit with
water (for example using a hose connected to the cock) until the level in the receptacle is about
half-way up the slot. The filling of tank before starting-up the unit is very important as the pump
can not operate without water.
The receptacle used for filling the circuit acts as an open expansion tank. It is therefore necessary
to pay attention to the volumes and dimensions in play.
5 . 5 E l e c t r i c a l c o n n e c t i o n s
Check that the power supply voltage and frequency match the requirements of the unit as shown on the unit data plate and they are within the
tolerances given in the wiring diagram.
Ensure that the electrical installation complies with local wiring and safety regulations.
Check that there is a neutral line in the electrical installation and it is earthen in the transformer cabin (TN system in compliance with IEC 364 -
HD 384 - CEI 64-8) or that this is done by the electricity supply company (TT system).
The electrical supply cable must be connected to the electrical installation and pay attention to connect the neutral wire of the unit (indicated by
the appropriate colour) to the neutral wire of the installation.
The electrical supply cable must be the one supplied with the unit and/or indicated in the electrical wiring diagrams.
At the beginning of the electrical supply cable
1.
must be guaranteed a protection against direct contacts with a protection degree of IP2X or IPXXB at least;
2.
must be installed protection devices that:
• protect against overcurrents, the power supply cable and the cables not protected by the electrical plant of the machine;
(see information in the electrical wiring)
• limit the 17 kA peak short circuit current to its own nominal cut-off power when the short circuit current at the operation point is
higher than 10 kA effective;
• protect against indirect contacts on the unit, (such as short-circuiting between the phase and protection circuit) by cutting off the
supply automatically (see IEC 364 - HD 384, CEI 64-8);
Use a differential switch (normally with operation nominal differential current of 0.03 A)
• protect against phase failures where the electrical supply is three-phase.
For protection circuit dimensions, please refer to the data specified in the wiring diagrams attached (max. absorption, pick-up currents, cables
section).
C
HAPTER
6
S
TART
UP
ATTENTION
Before starting up or operating these units be sure that all personnel have read and understood the
“Safety”
section of this manual.
1.
Check that the machine's on/off valves are open.
2.
Check that the level of the liquid in the receptacle is at about the middle of the graduated scale.
3.
Check that the ambient temperature is within the limits indicated on the machine data plate.
4.
Check that the main switch is in the OFF position (“O”).
5.
Check that the power supply voltage is correct.
6.
Turn the machine main switch ON (“I”). The display lights on to indicate the presence of tension.
7.
The pump is not ready to start.
If with the first start-up,
there is a high ambient temperature and the temperature of the water in the hydraulic circuit is much higher than the
working value
(e.g. 25-30°C)
this means that the
chille
r starts up overloaded with the consequence of
possible tripping of the compressor