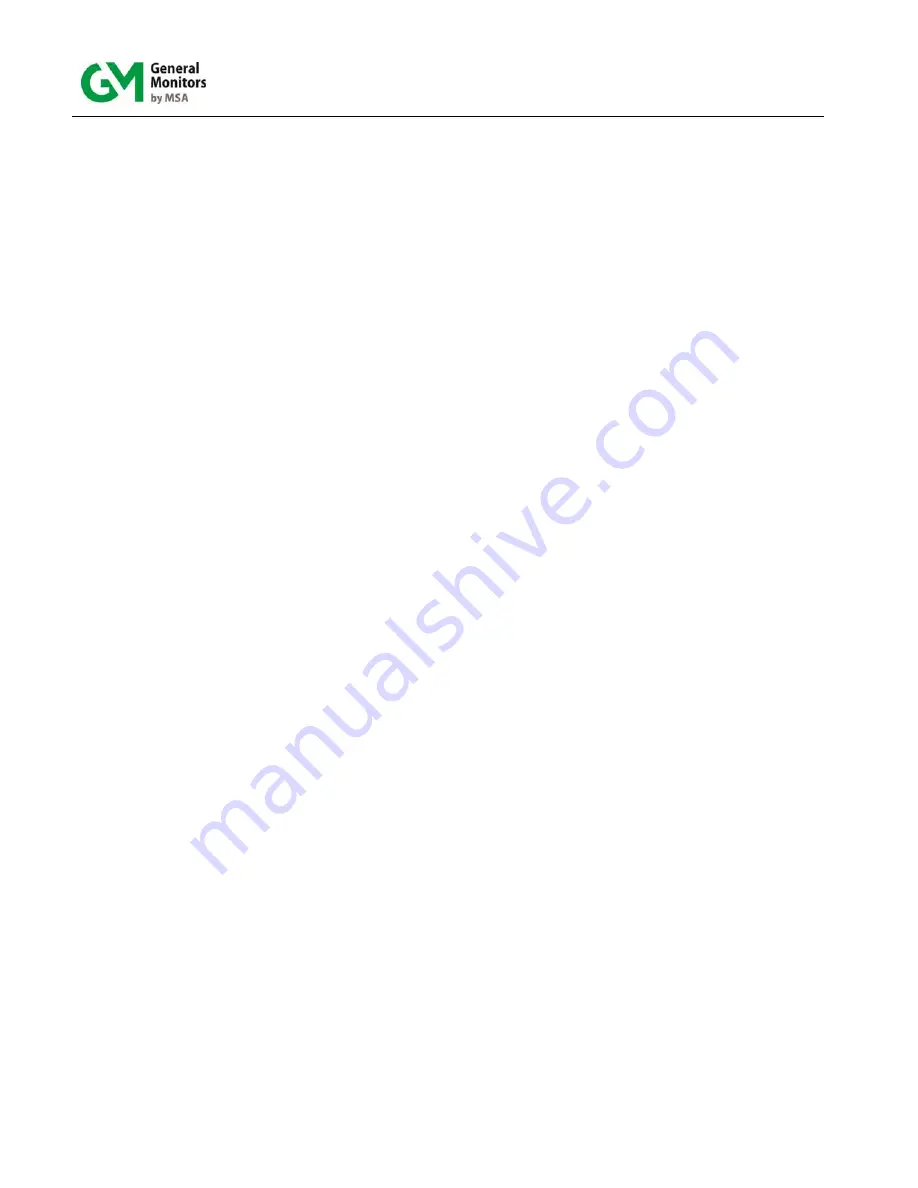
Model S4000TH
ii
Table of Contents
MODEL S4000TH .......................................................................................................................... I
INTELLIGENT SENSOR FOR ....................................................................................................... I
HYDROGEN SULFIDE GAS DETECTION ................................................................................... I
TABLE OF FIGURES .................................................................................................................. VI
TABLE OF TABLES ................................................................................................................... VII
QUICK START GUIDE ................................................................................................................. 1
Mounting and Wiring ............................................................................................................................... 1
Tools Required ........................................................................................................................... 1
Terminal Connections ............................................................................................................................. 2
1.0
INTRODUCTION .................................................................................................................... 4
1.1
Protection for Life ....................................................................................................................... 4
1.2
Special Warnings ....................................................................................................................... 4
1.3
System Integrity Verification ...................................................................................................... 5
2.0
PRODUCT DESCRIPTION ..................................................................................................... 7
2.1
General Description ................................................................................................................... 7
3.0
INSTALLATION ...................................................................................................................... 8
3.1
Receipt of Equipment ................................................................................................................. 8
3.2
Tools Required ........................................................................................................................... 9
3.3
Choosing Product Locations ...................................................................................................... 9
3.3.1
Remote Mounting of the Sensor from the Electronics ................................................ 10
3.4
Mounting and Wiring ................................................................................................................ 11
3.5
Terminal Connections .............................................................................................................. 13
3.5.1
Terminal Block TB1 – Sensor Connections ................................................................ 13
3.5.2
Terminal Block TB2 – Power and Signal Connections ............................................... 13
3.5.3
DC Power and Ground Connections ........................................................................... 15
3.5.4
Analog Signal Connections ......................................................................................... 16
3.5.5
Terminal Block TB3 – Relay Connections .................................................................. 16
3.5.6
European Union (EU) Approved Applications ............................................................. 17
3.5.7
Cable Termination in the Non-hazardous Area .......................................................... 17
3.6
Maintaining the X/P Integrity .................................................................................................... 18
4.0
OPERATION ......................................................................................................................... 19
4.1
Start-Up Checklist .................................................................................................................... 19
4.2
Start-Up .................................................................................................................................... 19
4.3
Relay Reset .............................................................................................................................. 19
4.4
User Selectable Options .......................................................................................................... 20
4.4.1
Model S4000TH User Menu Structure ........................................................................ 21
4.4.2
Sensor Range ............................................................................................................. 21