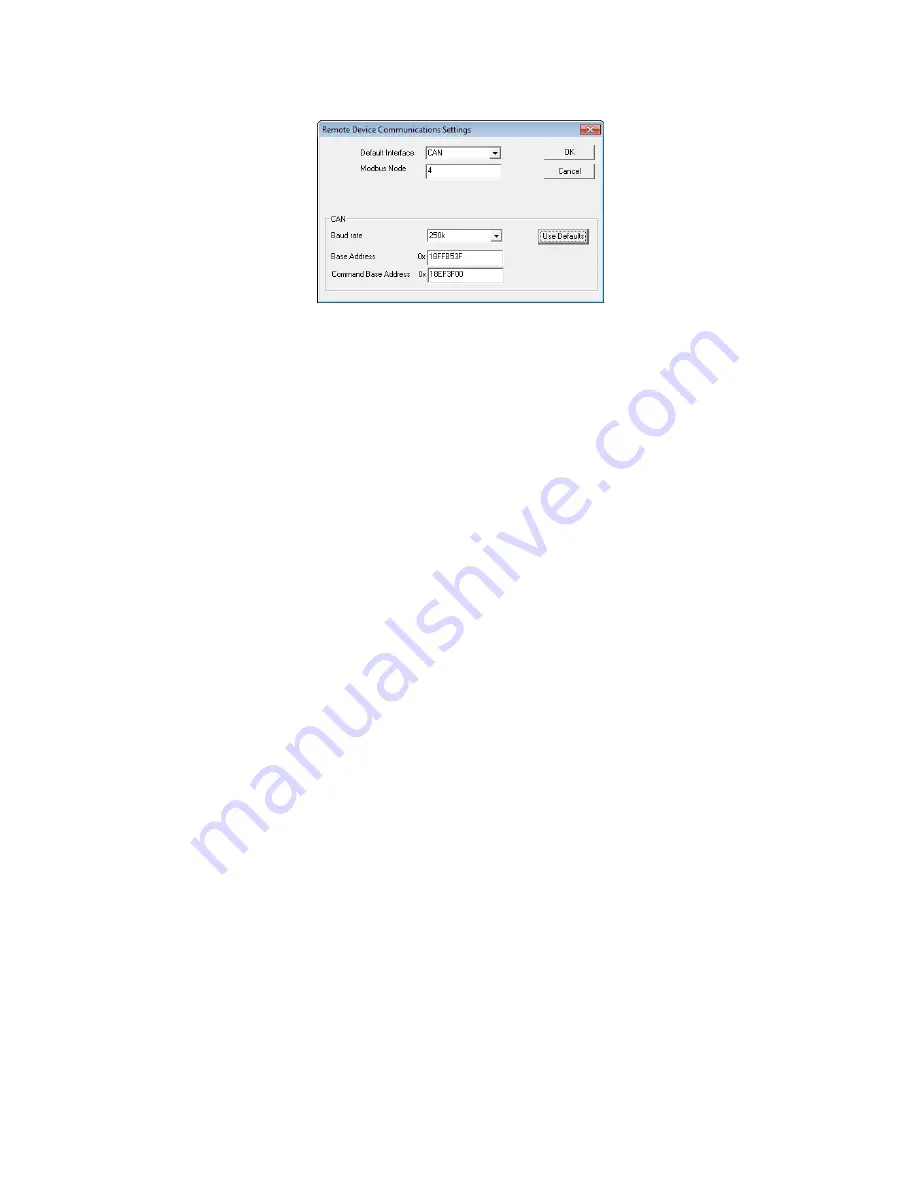
Appendix A
14
Example Walk-through
Figure IV
Communication Settings
Select the Interface, Node Number and Baud Rate as shown, then press ``Use De-
faults’’ to assign the ``base address’’. This will define the start of the block of CAN
message identifiers used by the software (using a value compatible with the J1939
standard).
Press the OK button on the ``Communications Settings’’ and ``Remote Device
Settings’’ dialogues. Leave the Remote Control dialogue open.
Now check that the ICM is now set to automatically perform tests:
•
Unplug the ICM circular connector
•
Plug it back in
•
You should see the connection re-established on the Remote Control dialogue
within a few seconds.
•
A test should have been automatically started
•
The tests should repeat every 10 seconds
•
You should see a test result that starts high and decreases with each further test.
Close the Remote Control dialogue and quit the program. Unplug the ICM at the
circular connector.