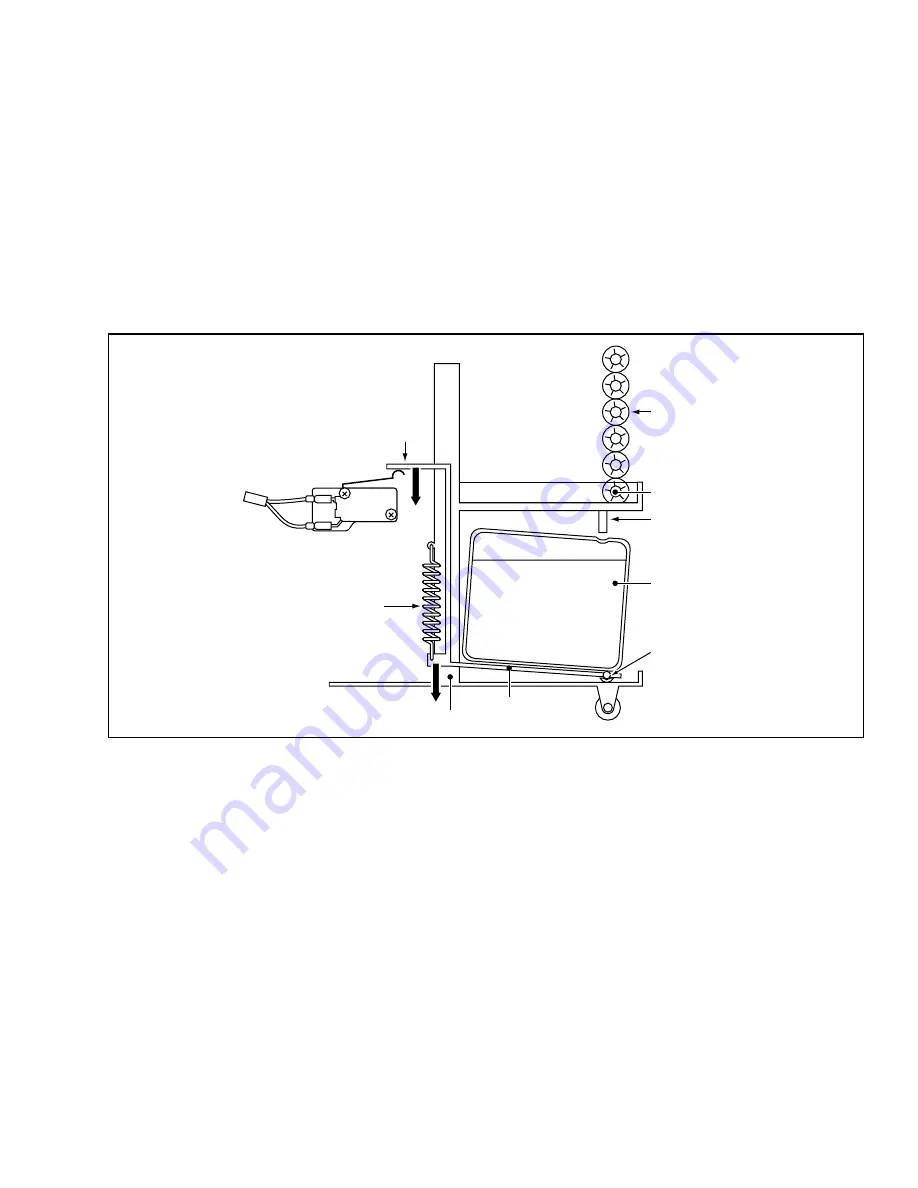
ELECTRICAL SYSTEM
17
Operation of Drain Switch
6.
Drain Switch
The Classic Plus 14 is equipped with a drain tank switch. When the drain tank accumulates approxi-
mately 4.0 gallons (15 liters) of condensate (water) in the drain tank, the drain tank switch sends a signal
to the microprocessor. The microprocessor stops all operation of the unit and flashes the "Tank Full"
LED.
This system utilizes a .1 AMP, 250 VAC micro-switch for this function. When drain water accumulates
approximately 4.0 gallons (15 liters) in the drain tank, the drain tank base plate, which is supported at its
fulcrum, is pushed down in the direction of the arrow as shown in the figure below. When the drain tank
base plate is forced down, the top of the drain tank base plate turns off the contacts (1) – (2) of the micro
switch. This causes the ground signal at the J103 connector of the control panel assembly to go open.
When the microprocessor detects this event, it turns the unit off and flashes the "Tank Full" LED.
When the drain tank is removed (or the drain tank is emptied), the top of the drain tank base plate
returns to its original position by the tension of the coil spring. Then contacts (1) – (2) of the drain tank
switch close. This provides a ground to the microprocessor through the J103 connector. To re-start the
unit, press one of the fan mode buttons or the “Cool On/Off” button. The unit will return to the previous
Temperature Set Point.
7.
Condensate Pump Kit (optional)
The Classic Plus 14 model comes standard with a drain tank, which collects the water that forms on the
evaporator during normal cooling operation. If the unit is required to operate continuously without
periodic emptying of this tank, a condensate pump may be needed. A condensate pump kit (CPK-3) is
available for the Classic Plus 14 model.
;;;
yyy
;;;
;;;
yyy
yyy
2
NC
C
1
DS2
DS1
To J103
DRAIN
SWITCH
DRAIN W
DRAIN WATER
BASE
PLATE
BASE
SPRING
DRAIN TUBE
EVAPORATOR
DRAIN TANK
FULCRUM
DRAIN PAN
TOP OF
BASE
PLATE
Summary of Contents for Classic Plus 14
Page 1: ...SERVICE MANUAL CLASSIC PLUS 14 ...
Page 3: ...ii ...
Page 5: ...iv ...
Page 7: ...GENERAL DESCRIPTION 2 ...
Page 46: ...DSCA P N LA990009 0379 ...