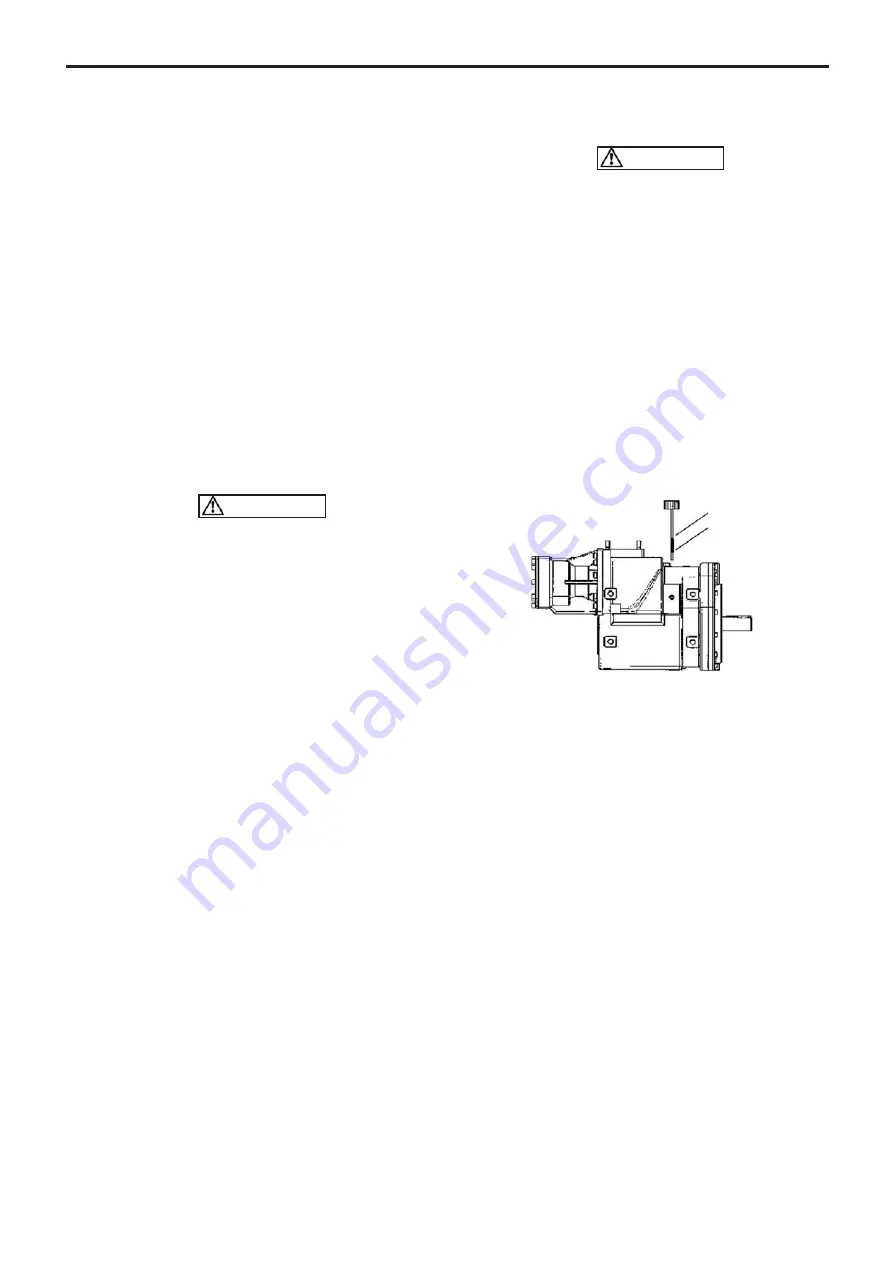
14/16
NT 1401-G00 10 18 TYPHON II e
The operator should remain nearby the equipment throughout
the use to ensure the proper functioning of the system.
4.1 Lubricant recommendations
MOUVEX BSC3 oil is recommended for 20R and 30R
configuration, whereas it is imperative for 13R/15L and
19R/22L.
A start up oil change has to be made after one week or
10 working hours. Not performing this oil change will void
the warranty.
For the first week or 10 working hours, you can choose
a standard mineral oil.The standard mineral oil grade will
be selected according to the ambient temperature under
which the compressor will be operated :
- Below -10°C. . . . . . . . . . . . . . SAE 10 W 40
- Between -10°C and 30°C . . . SAE 15 W 40
- Above 30°C . . . . . . . . . . . . . . SAE 15 W 50
With BSC3 oil, oil change is recommended every year or
600 working hours that the compressor is equipped with
or without a multiplier.
I
n case of operations done
under minus 25°C
, BSC3 oil
viscosity sharply increases and can generate starting
troubles. It will be necessary, in that case, to preheat the
compressor body.
It is also allowed to use oil SAE 5W40 temporarily allowing
to tolerate -35°C.
That implies the following constraints :
• Oil must be replaced every 100 operating hours.
• Imperative return to the BSC3 when the temperature
becomes again positive.
Oils BSC and SAE are miscible; the passage of the one
with the other thus does not imply particular procedure of
cleaning.
Compressors can be used with an external oil cooler in
case of intensive applications (see Instructions 1401-AC00
O
IL
COOLER
SCREW
COMPRESSORS
MISTRAL B600
TYPHON II).
4.2 Filling of lubricant
Our packages are delivered without oil. The use of a
compressor with an oil level that is not located
between the two limits indicated by the gauge can lead
to important property damage and serious injuries.
The quantity of oil for each compressor is approximately :
• TYPHON II 20R - 30R . . . . . . . . .
6
l
• TYPHON II 13R/15L . . . . . . . . . .
7
l
• TYPHON II 19R/22L . . . . . . . . . .
7
l
Before starting the system, fill the casing with oil so that
the oil level is set between the min and max value of the
gauge.
NB : A residual volume of 0,5 l of oil may be present inside
the compressor when it leaves the factory.
After filling, the level must under no circumstances
exceed the maximum marker on the oil gauge (the level
is taken after the gauge has been completely screwed
onto the filling tube).
Max level
Min. level
CAUTION
CAUTION
4. USE OF COMPRESSOR