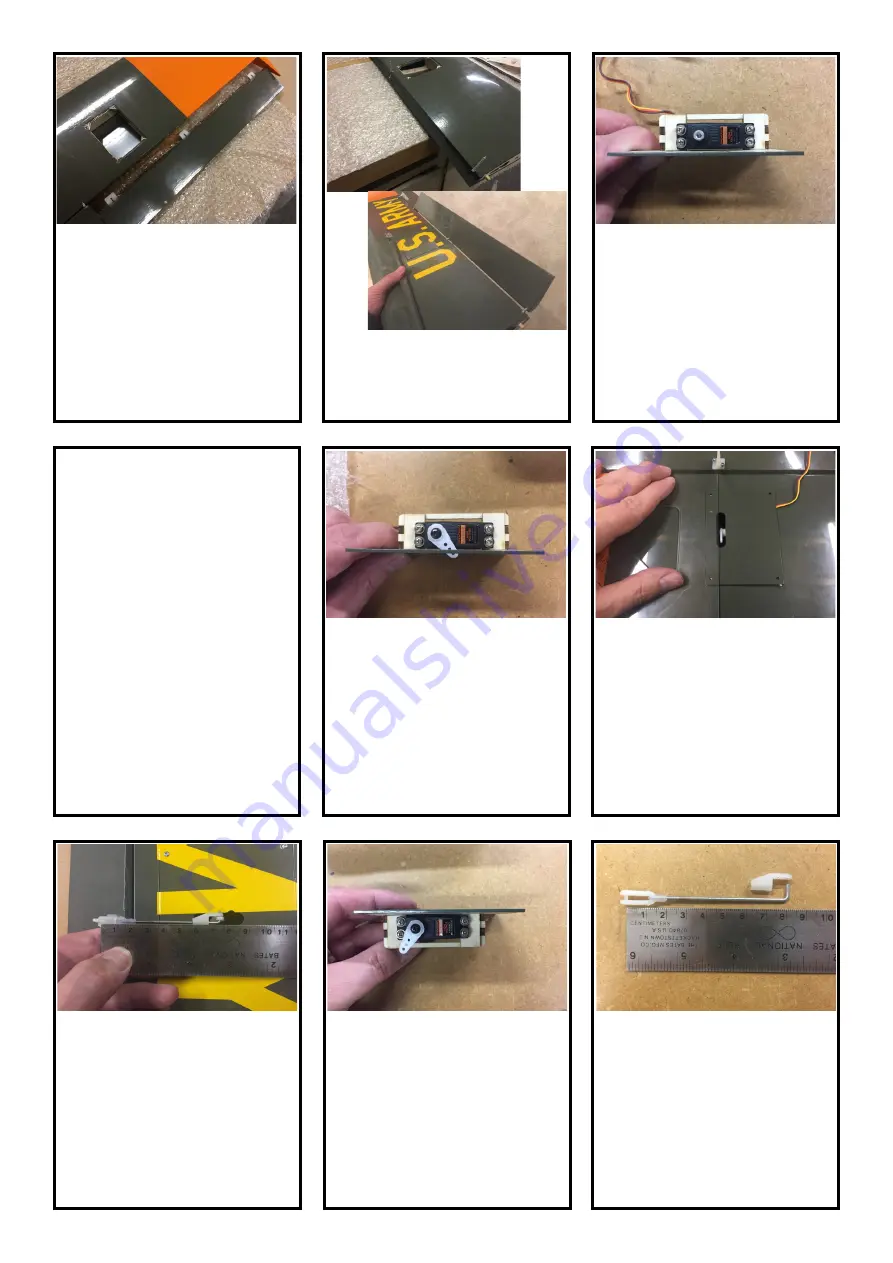
©2019 Moustache Model Works, LLC
31
20cc DHC
-
2 Beaver Instruction Manual
64.
Install the 2mm pushrods using nylon
clevises at the control horns and snap
connectors at the servo arms. Pushrod
length will be about 2
7/8”
(73mm) from
the clevis pin to the bend.
65.
As with the ailerons, prepare and install
matching servo arms of 1/2 (13mm)
length to the flap servos. In the
“
flaps
up
”
position, the servo arms should bias
forward about 30°.
60.
Attach an 18
-
inch (45cm) servo exten-
sion to each aileron servo lead and
secure using connector clips such as
Spektrum part number SPMA3054 or
dental floss wrapped around the con-
nectors.
61.
Select matching servo arms for the
aileron servos with an arm length about
1/2”
(13mm) from the center to the
outermost hole. Cut off all the remain-
ing arms, and drill the outermost hole, if
necessary, to fit the 2mm pushrods.
No Photo
62.
Ensure the aileron servos are centered
by connecting them to the receiver,
binding and powering
-
up. Install the
servo arms with a significant forward
bias to the front to provide mechanical
differential throw (more up deflection
than down).
63.
Attach the aileron control horns to the
ailerons using the supplied screws. Drill
pilot holes in the plywood using a
1/16”
(1.5mm) drill.
66.
Prepare the flap pushrods for installa-
tion using 2mm pushrods, nylon clevis-
es and snap connectors. The pushrod
length will be about 3
3/16”
(80mm)
from the clevis pin to the bend.
56.
Cover the wings, ailerons, flaps, and
hatches using your favorite covering
film. Hint: a hot soldering iron works
great to melt the holes for the round
hinges, and for the cutouts in the aileron
hatches.
57.
Attach the ailerons to the wings using
the supplied CA hinges.
58.
Attach the flaps to the wings using the
round hinges and epoxy. Apply a bit of
petroleum jelly to the hinge pin area to
prevent their getting frozen stuck by
some stray epoxy.
59.
Install the aileron and flap servos to the
hatch mounts using the hardware that
came with your servos. Space the ser-
vos away from the hatch surface using
a scrap piece of 1.0mm or 1.5mm ply-
wood. Note the flap servo output shaft
should be toward the forward edge of
the hatch.