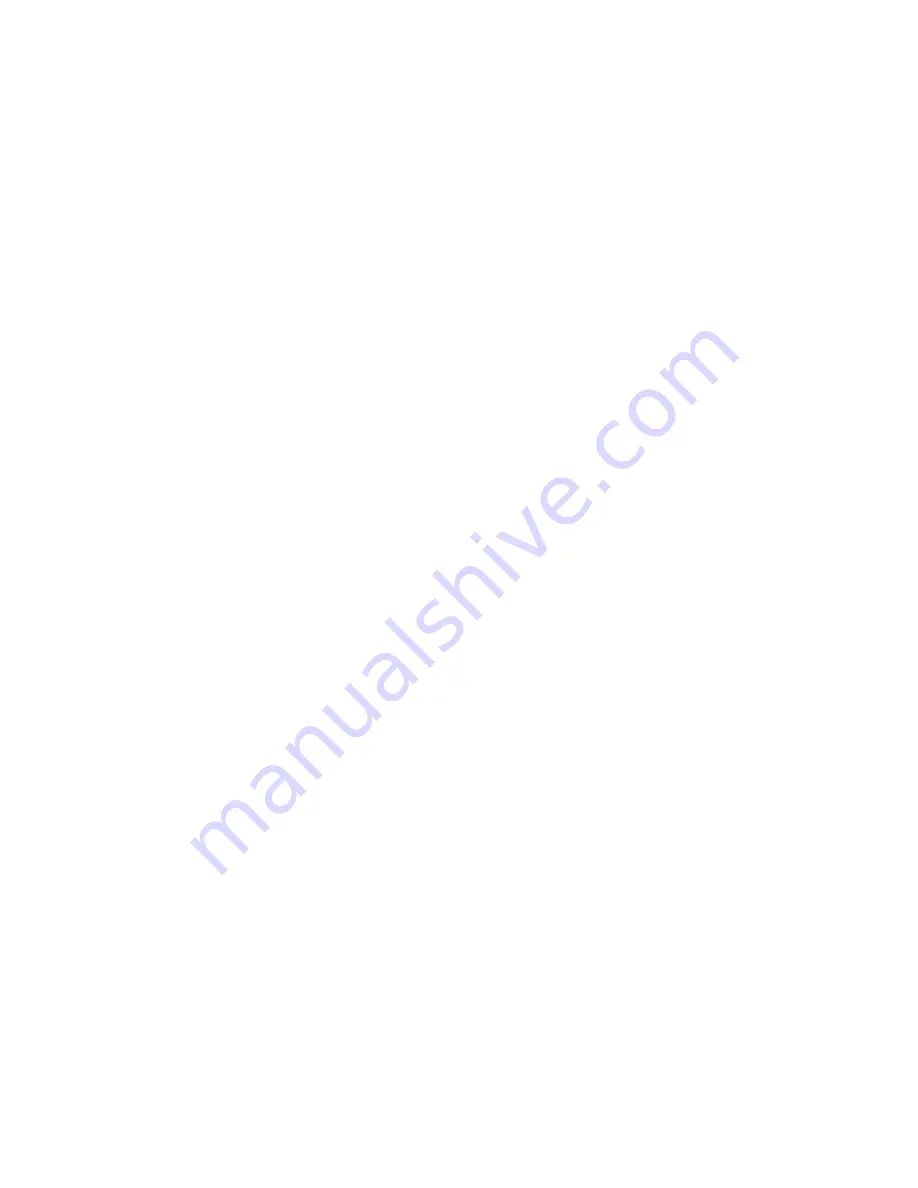
CSD Series
Variable Frequency AC Drive
MOTORTRONICS
- 3 -
The
CSD Series
unit offers an optional function called dynamic braking.
Dynamic braking, in adjustable frequency drives, allows the motor to
produce 100% braking torque for a 10% duty cycle for four-quadrant
operation (like DC regenerative drives). With dynamic braking, the
regenerative energy from the motor is dissipated by switching the
dynamic braking transistor to shunt the regenerative current from the
DC bus capacitors through the braking resistor (See Figure 1 - 3).
This circuit is optional in the CSD drive line, please contact the factory
if your application requires dynamic braking.
1.4.3 Logic Section
The heart of the drive’s control section is the Central Processing Unit
(CPU). This component handles the logic functions, including output
waveform generation, monitoring of commands, and self-diagnostics.
The CPU also simplifies troubleshooting and setup by displaying and
storing very specific, alpha-numeric fault codes displayed on the
keypad. For example, you can immediately determine if an overcurrent
(OC) trip occurred during start, acceleration, deceleration or constant
speed operation by the unique fault code corresponding to each of
these conditions.
The output waveform is “sine-coded, Pulse Width Modulation (PWM)”,
which gained wide acceptance because of its high starting torque and
smooth low speed motor rotation capabilities. In addition, the motor’s
“torque per amp” ratio is good, implying a very efficient output current
waveform. The drive can accept control commands (run or frequency
reference inputs) from either the terminal strip or the integral keypad.
The terminal frequency reference command can be either 0-10 VDC,
0-5 VDC or 4-20 mA. The drive’s actual output frequency can be
monitored directly from the keypad or from a remote meter connected
to the drive’s analog meter output (0-10VDC, current regulated).
1.4.4 Motor Rating for Variable Speed Application
Motortronics recommends, whenever possible, the use of “drive duty”
motors to prevent premature motor failures that may occur in some
variable frequency drive applications. “Drive duty” motors have increased
insulation on the first few turns of the motor, preventing failures from
“punch through” of the insulation in 400-600 volt class, low horsepower
motors. “Punch through” is caused by a proportionally higher amount
of the dv/dt output of the drive being dropped across the first few turns
of the motor. “Drive duty” motors also provide rated cooling during all
speed ratings. This feature prevents failure due to reduced cooling
capabilities when a TEFC (totally enclosed fan cooled) motor is being
run at reduced speed and in constant torque applications. Motortronics
recommends that the motor manufacturer be consulted in all variable
frequency drive applications to ensure that the motor will be able to
perform the application requirements.
Summary of Contents for CSD Series
Page 2: ...CSD Series Variable Frequency AC Drive MOTORTRONICS 74 ...
Page 4: ...CSD Series Variable Frequency AC Drive MOTORTRONICS 76 ...
Page 30: ...CSD Series Variable Frequency AC Drive MOTORTRONICS 26 ...
Page 32: ...CSD Series Variable Frequency AC Drive MOTORTRONICS 28 ...
Page 65: ...CSD Series Variable Frequency AC Drive MOTORTRONICS 61 ...