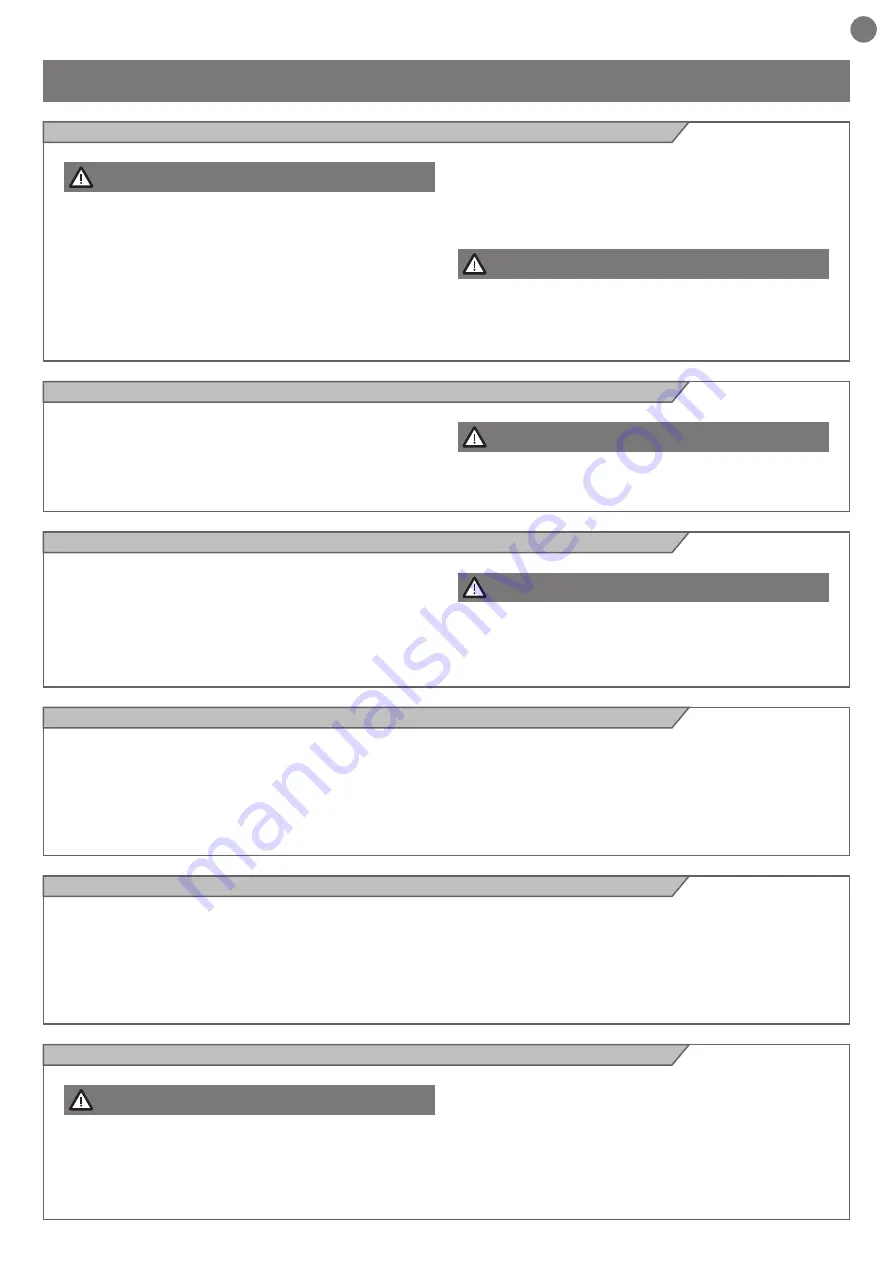
EN
23
The installer shall check that the temperature range marked on
the drive is suitable for the location.
Before proceeding with the installation, check the integrity of the
product and that all components are present in the package.
Check that the gate weight respects the limit of the table (paragraph
2.2) and dimensions of the gear motor are met (Fig. 1).
Fig.2 shows a typical installation:
Gear motor (1)
Verify the orientation and the overall dimensions of the base plate,
fix to ground the base-plate through 4 sturdy screw-anchors or
drown it into the concrete (Fig.3).
Provide one or more corrugated duct tubes for routing the electric
cables.
To release the gearmotor remove the cap on the side (Fig.4.1)
and turn the pin with the release key (Fig.4.2). Then turn the lever
(Fig.5).
Open the cover by applying leverage with a screwdriver on the
recesses at the sides (Fig.6).
Place the gearmotor on the plate and fix the 4 nuts (Fig.8a). If the
permitted adjustment of the rack is not sufficient, before tightening
the nuts the height of the gearmotor can be corrected using the four
regulator stud bolts (Fig.8b).
Open entirely the gate.
Put a rack element on the pinion gear and fasten it to the gate with
screw and spacing bars (Fig.10).
Move the gate manually bringing the pinion gear into line with the
last spacing bar.
Fasten the rack element for good.
After the adjustment, it is important to fully tighten the nuts, making
sure that the gearmotor is firmly anchored to the ground throughout
the gate’s travel stroke.
The screws should be tightened again after the gearmotor has been
operated a few times. Replace the cover so that the light is pointed
in the required direction (Fig.9), such as towards the passage.
For a correct positioning of the other elements and to assure their
straightness, it is necessary to employ a rack element using it as
support and reference. It is besides necessary to assure an aperture
of 2 mm between rack and pinion gear, so that the gate weight
doesn’t rest on the gearmotor pinion gear.
Photocells (2)
Columns for photocells (3)
Flashing light with antenna (4)
Key switch or digital keypad (5)
Pressure-sensitive edge (6)
The automation system must be equipped with a pressure-
sensitive edge protecting all possible crushing points
(hands, feet, etc.) in accordance with the requirements of the
EN 13241-1 standard.
The exact dimensions of the rack must be known to allow
precise calculation of the fixing plate position.
The gate has to be equipped with stop locks at the opening
and closing, which prevent the gate derailment.
With motors with integrated night lights make sure not to
rip off the cable that connects the leds on the cover with the
control board. If necessary, disconnect the connector shown
in figure 7.
The stop lock position must assure that the limit switch brackets
don’t collide with the pinion gear. (Fig.11)
Haul the gate manually at the opening leaving, depending on the
gate weight, a leaving a gap from 30 to 50 mm between the main
gate and mechanical stop.
Fasten the limit switch bracket through the dowels so that the limit
switch is pressed (Fig.11).
4 - PRODUCT INSTALLATION
4.1 - Installation
4.2 - Installing the foundation plate
4.3 - Motor unlock
4.4 - Fixing the plate
4.5 - Rack assembling
4.6 - Limit switch fixing
ATTENTION !
ATTENTION !
ATTENTION !
ATTENTION !
ATTENTION !
Summary of Contents for SLIDER SLD400
Page 42: ...42 INSTALLER DATA INSTALLER DATA DATE SIGNATURE...
Page 43: ...43...