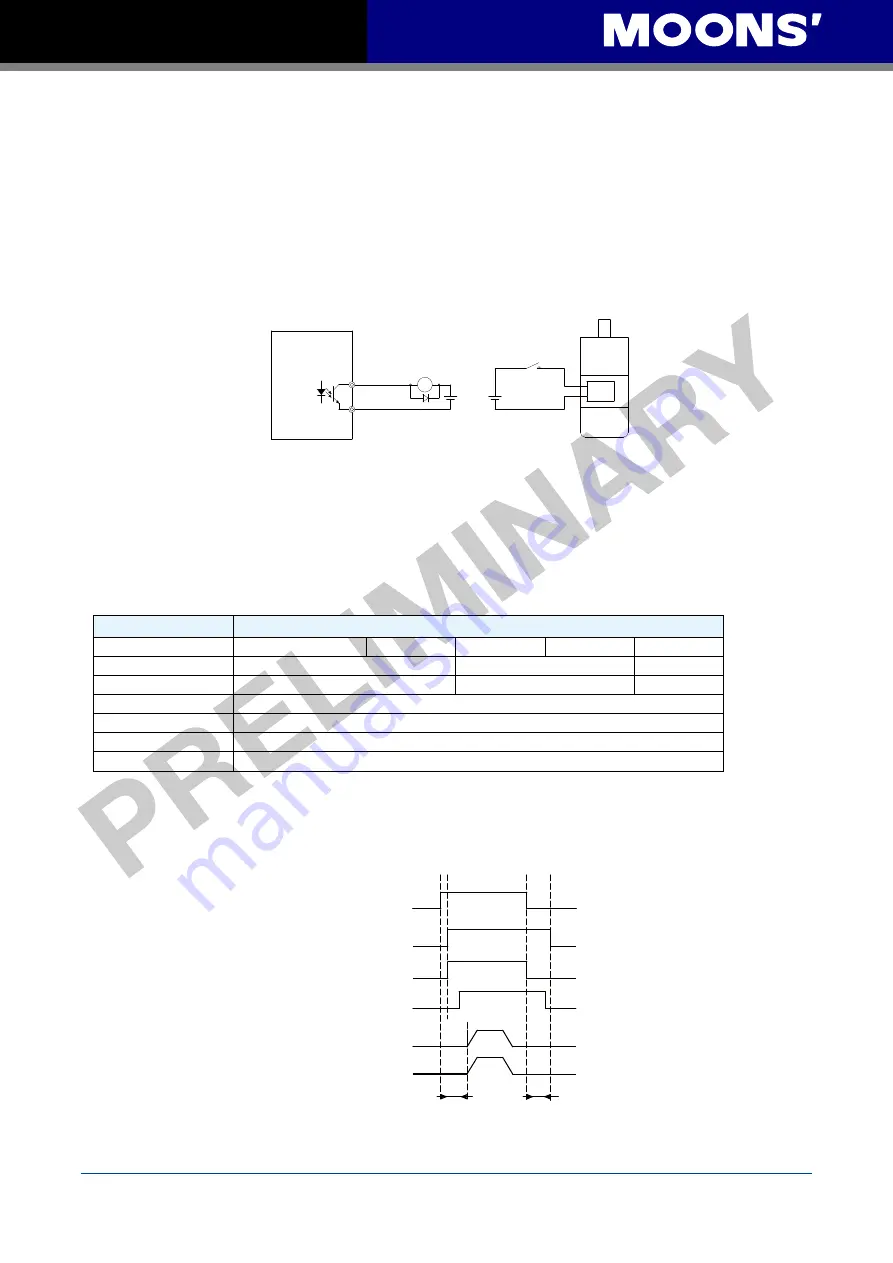
14
Rev. 1.0
4/29/2016
M2 Quick Setup Guide Manaul
3.4 Electromagnetic Brake
When motor drives the vertical axis, brake should be used to hold and prevent the work (moving
load) from falling by gravity while the power to servo is shut off.
NOTE: only use servo motor brake for hold the stalling status, i.e.. motor is in disable or
power off.
Never use this for “brake” purpose to stop the load in motion. Wrong use might cause
servo motor damage.
3.4.1 Wiring Diagram
24V
DC
Relay
Brake+
Brake-
R
Servo Drive
Relay
Brake
24V
DC
3.4.2 Notice for the Brake Motor
◆
When no power is applied to the electromagnetic brake, it is in locked position. Therefore, the
motor shaft will not be able to rotate.
◆
The brake coil has no polarity.
◆
During the brake/release action, there might be
“
Ka-Da
”
sounds occurring, this does not
effect the use of brake.
◆
Speci
fi
cation of brakes are as follows:
Motor Power
Type
50W
100W
200W
400W
750W
Holding Torque(N
•
m)
0.35
2
4.5
Working Current(A)
0.25
0.38
0.61
Rated Voltage(V)
24V
±
10%
Release Time
<25ms
Engage Time
<25ms
Release Voltage(V)
Release Voltage18.5VDC
3.4.3 The timing charts of the electromagnetic brake
In order to prevent damage to the brake, there are delay sequences during the brake operation.
Please be cautious with brake operation sequence.
Servo-on In Put
OFF
ON
Motor Active
OFF
ON
Brake Action
OFF
ON
Brake Signal
OFF
ON
Motion Command
OFF
ON
Actual Motion
OFF
ON
Brake Release Delay
P-68 Setting
Brake Engage Delay
P-69 Setting
Brake/release delay time can be set via M servo suite software, or on the drive itself through P
function: P-68(BD) or P-69(BE) .