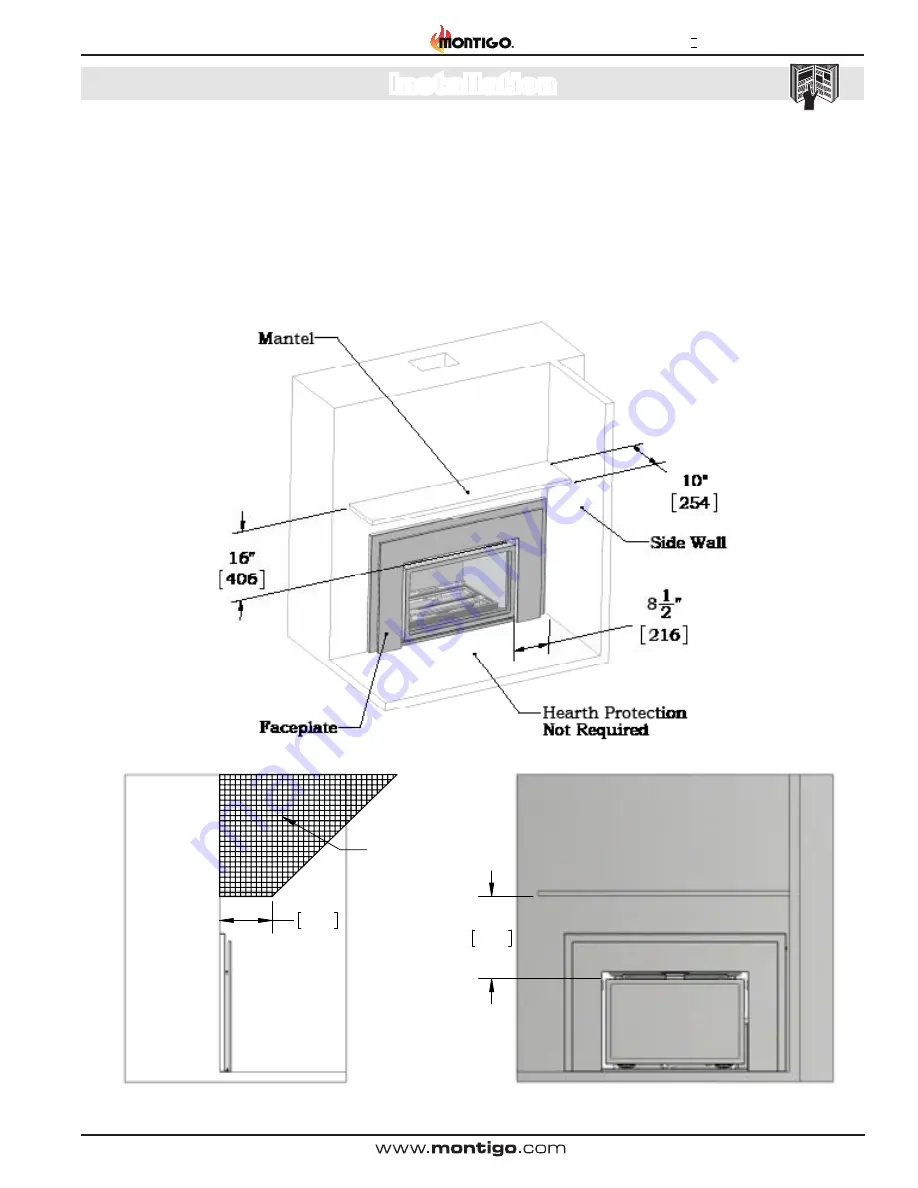
Page 11
XG00516-060614
I-Series Indoor Gas Fireplace
Installation
Figure 2 Sec.2
30DFIDV-LGS
clearances
10"
254
Max
Allowable
Mantel
Area
30"
32"
34"
36"
38"
16"
406
Min
16"
18"
20"
22"
24"
26"
28"
32"
28"
24"
20"
16"
12"
8"
4"
Figure 3 Sec.2
30DFIDV-LGS mantel
clearances
Min
Clearances:
The 30DFIDV-LGS
Insert is designed and built to be installed into
masonry or manufactured fireplaces. There is no requirement to
have a non-combustible hearth in front of the unit. Clearances
to the underside of the mantel or sidewall are measured from
the edge of the door/screen front. The Mantel is shown as 10”
maximum at a distance of 16” minimum from the door edge top.
The mantel can be extended further providing that you increase
the height proportionately. For instance, if you want a mantel that
is 2” beyond the 10” minimum, you have to install it 2” above the
16” minimum.