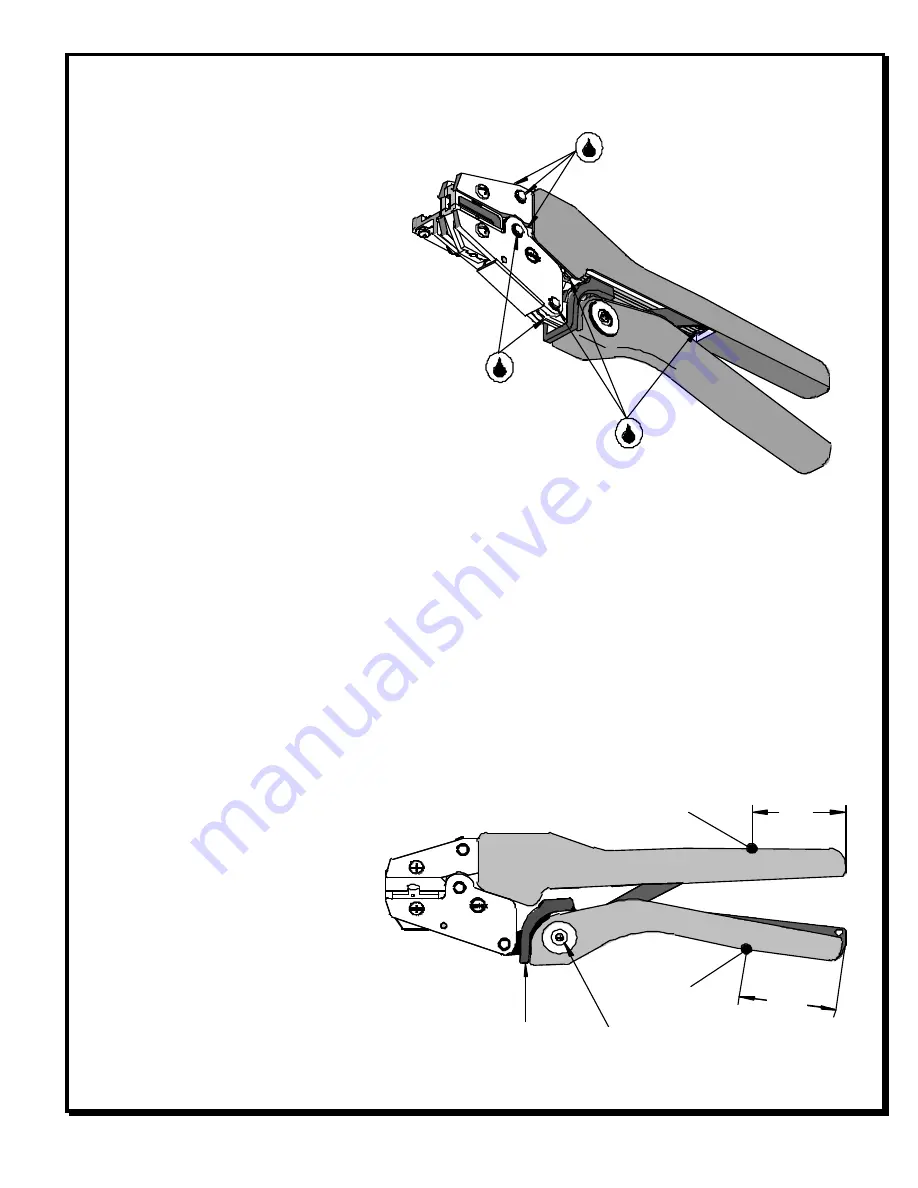
RHT5758-CC Hand Crimp Tool
Doc No. 64001-1000
Release Date: 12-11-02
UNCONTROLLED COPY
Page 3 of 6
Revision: B
Revision Date: 09-02-03
Maintenance
It is recommended that each operator of the tool be
made aware of, and responsible for, the following
maintenance steps:
1. Remove dust, moisture and other contaminants
with a clean brush, or soft, lint-free cloth.
2. Do not use any abrasive materials that could
damage the tool.
3. Make certain all pin, pivot points and bearing
surfaces are protected with a thin coat of high
quality machine oil. Do not oil excessively. The
64001-1000 (RHT-5758-CC) was engineered for
durability, but like any fine piece of equipment
it needs cleaning and lubrication for a maximum
service life of trouble-free crimping. A light oil,
such as 30 weight automotive oil used at the oil
points shown in Figure 4, every 5,000 crimps or
3 months will significantly enhance the tool life and ensure a stable calibration.
4. When tool is not in use, keep the handles closed to prevent objects from becoming lodged in the crimping dies, and store the tool
in a clean, dry area.
Miscrimps or Jams
Should this tool ever become stuck or jammed in a partially closed position,
Do Not
force the handles
open or closed
. The tool will
open easily by pressing the ratchet release lever (See Figure 5).
How To Adjust Tool Preload
(See Figure 5)
Over the life of the tool, it may be necessary to adjust tool handle preload force. Listed below are the steps required to adjust the
crimping force of the hand tool to obtain proper crimp conditions:
1. Remove the screw and plastic cover washer.
Note the setting wheel position.
2. Lift the setting wheel off the axle. Turn the
eccentric axle with a screwdriver.
3. Turning the eccentric axle counter-clockwise
will increase handle force.
4. Replace the setting wheel to the axle,
aligning the nearest notch in the setting
wheel to the dowel pin.
5. Replace the plastic cover washer and screw.
6. Check the crimp specifications after tool
crimp force is adjusted.
Figure 4
LUBRICATION POINTS (BOTH SIDES)
LIGHT OIL (EVERY 3 MONTHS OR 5,000
CRIMPS)
Figure 5
PRELOAD
ADJUSTMENT
LOCKING SCREW
1.00
1.00
PRELOAD
TEST POINT
PRELOAD
TEST POINT
RATCHET
RELEASE LEVER
PUSH UP