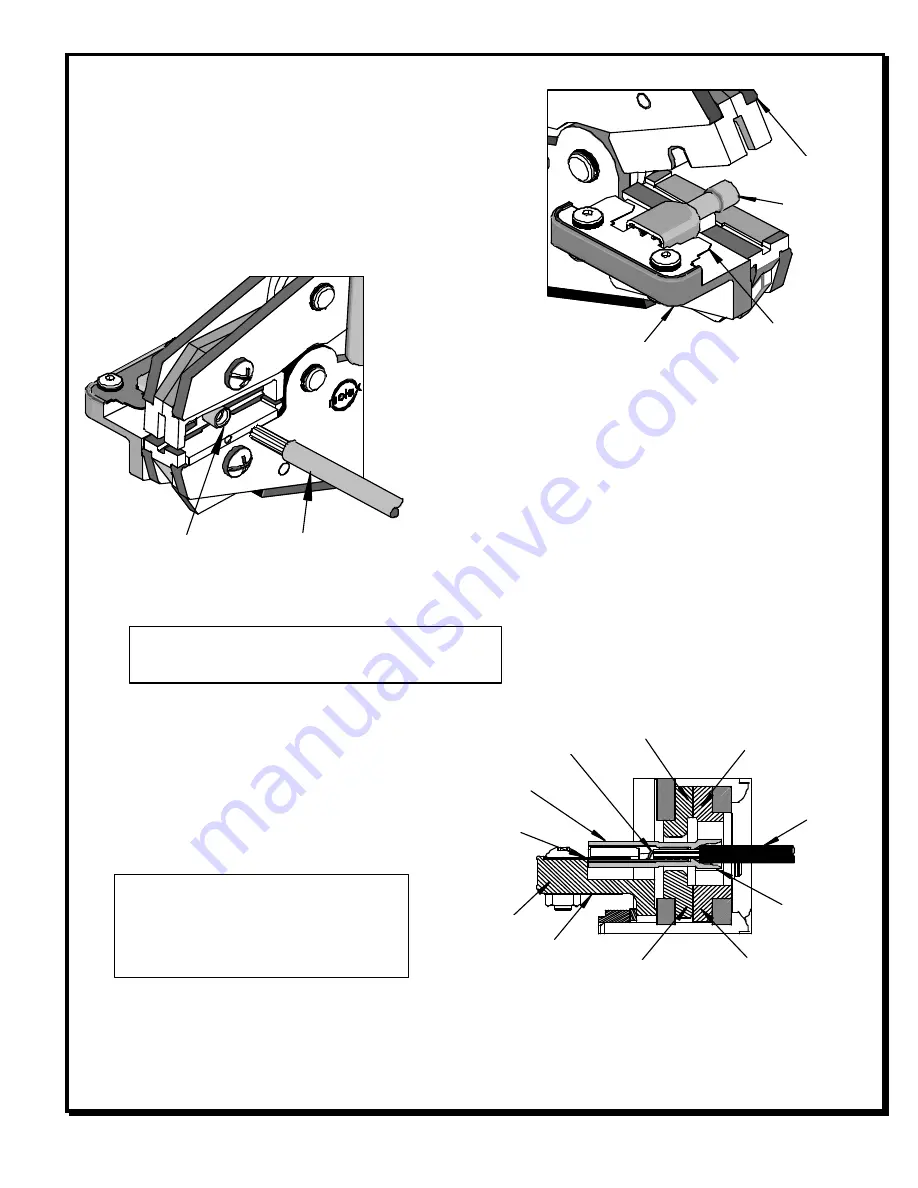
RHT5758-CC Hand Crimp Tool
Doc No. 64001-1000
Release Date: 12-11-02
UNCONTROLLED COPY
Page 2 of 6
Revision: B
Revision Date: 09-02-03
Note:
The tamper proof ratchet action will not release the tool
until it has been fully closed.
Note
: Whenever crimping without the locator,
make sure the seam of the terminal is oriented
up or down in the tool if using unbrazed product,
as this will provide higher pull force values.
Crimping Terminals
1. There are 2 tab locator blades supplied with the tool. One is for .187
and .250 tabs; the other is for .205 tabs and .110 tabs. Make sure the
proper blade is installed on the top of the locator and the other is stored
on the bottom of the locator.
2. Push the terminal onto the tab locator all the way to the stop in the
color-coded nest. The barrel of the terminal should be up (See
Figure 1).
3. Partially close the tool to hold the terminal in place (See Figure 2).
4. Insert the properly stripped wire into the terminal barrel (See Figure
2 and 3). Cycle the tool.
5. Remove the crimp and inspect for proper crimp
location. Molex offers a Crimp Inspection Handbook
for closed barrel industrial product. See our website
or contact your sales engineer.
WIRE
TERMINAL
Figure 2
LOCATOR
JAWS OPEN
TAB LOCATOR
Figure 1
TERMINAL
Figure 3
2
ND
TAB LOCATOR
WIRE
TERMINAL
BARREL
PUNCH
INSERT
CONDUCTOR
ANVIL
TERMINAL
LOCATOR
CONDUCTOR
PUNCH
ANVIL
INSERT
1
ST
TAB
LOCATOR
WIRE STOP BUILT
INTO TERMINAL