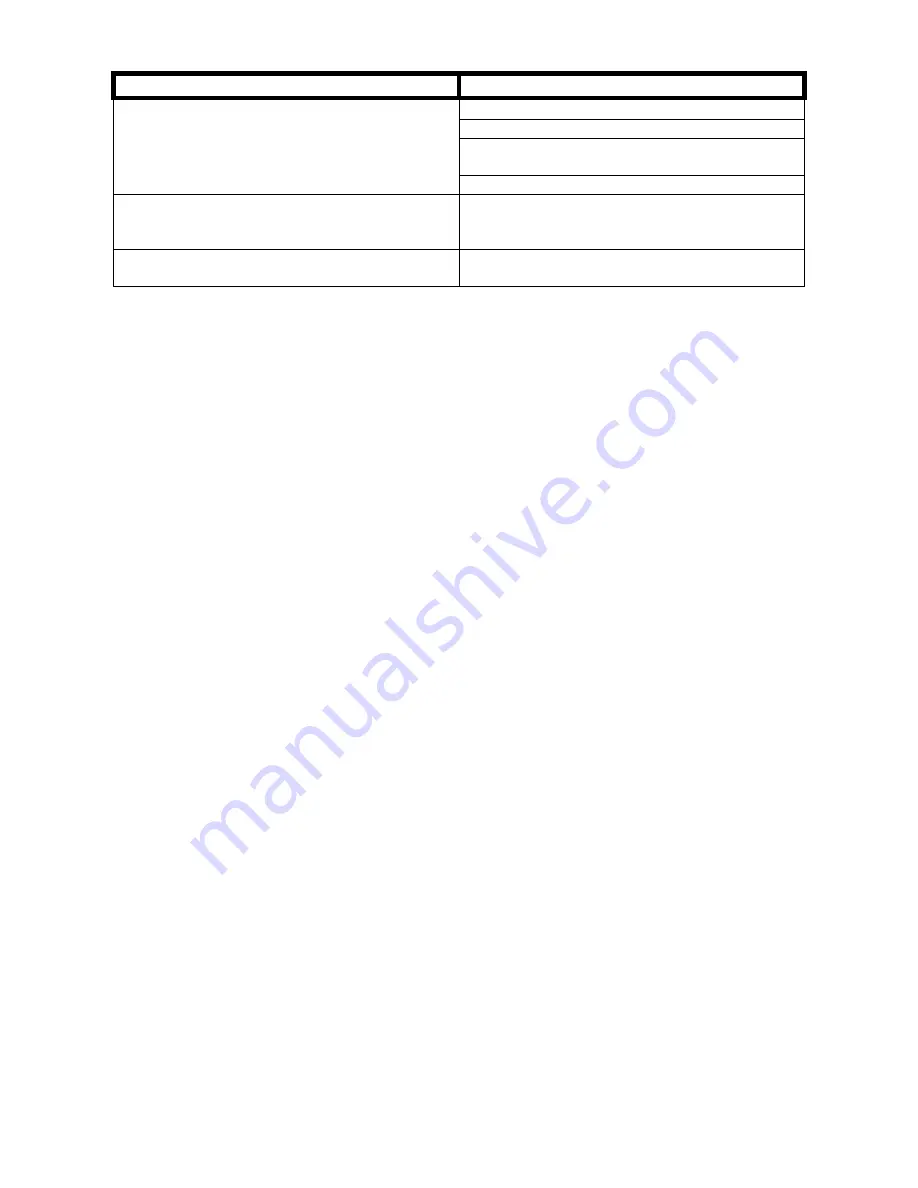
12
Monthly Checks
Corrective Procedures
Check that the heater current draw
matches the serial tag rating
Verify heater wiring stake-on is secured
Correct heater wiring
Verify customer supply voltage is balanced
and fluctuations are within 15% of nominal
Replace elements if necessary
Check that the "Warning," "High Voltage,"
"Caution," and lamicoid labeling are
adhering to the correct locations
Replace torn, damaged or missing labels
Check screen in optional pressure regulator
for debris
Remove screen and clean