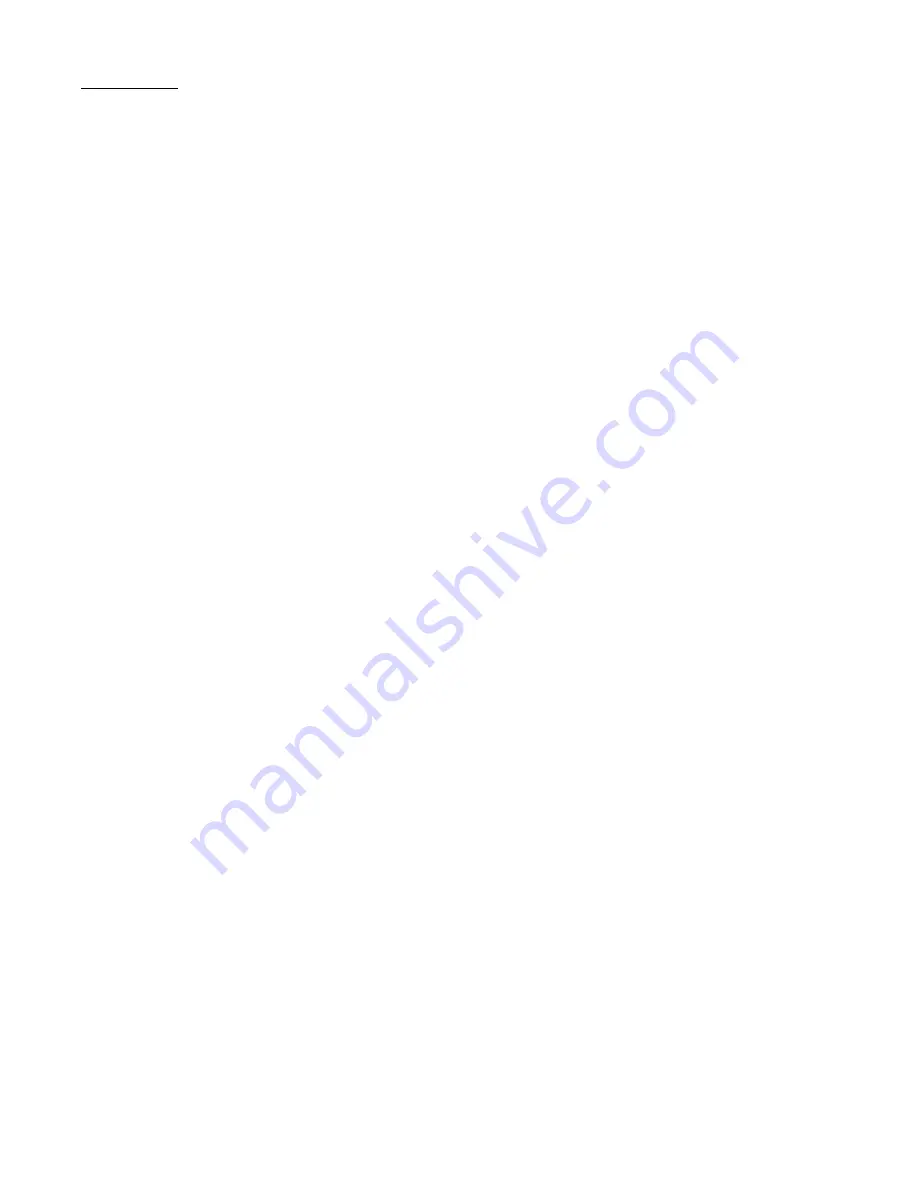
16
Reassembly:
Caution: The mechanical seal is a precision product and should be handled accordingly.
Use care when handling lapped running surfaces of the mechanical seal to ensure they
remain clean and are free of chips or scratches.
Clean gasket and flange faces, seal seat cavity and shaft, in particular, shaft shoulder fitting
against impeller.
Lubricate the seal seat cavity of the cover and the rubber cup or O-ring of stationary seal
seat with the lubricating fluid that comes with the mechanical seal or repair kit. Press the
stationary seat in seal seat cavity in the cover squarely and evenly using an arbor press (if
possible) and the cardboard disc supplied with the seal. Be certain that the lapped face
(shiny side) is facing you.
Position the cover (Ref 11) so that the convex side with the lapped seal seat is facing you.
Place the cover on the motor disc and align the holes in the disc with the holes in the cover.
(Note: There isn’t any hardware required to attach the cover to the motor disc.)
Apply the lubricating fluid that comes with the mechanical seal or repair kit to the motor
shaft and the rubber bellows of the rotary seal. Slide the seal head on the shaft; press the
rubber drive band on the rotary head until the lapped face on the head seats firmly against
the lapped face of the stationary seat. Install seal spring on head and seal spring retainer on
spring. Do not chip or scratch faces during installation. Take extra care to make sure the
lapped faces are clean.
Hold shaft against rotation as described in step 8 of disassembly procedure, then thread
impeller on shaft until it is tight against the shaft shoulder. The impeller will compress the
seal spring to the proper length assuring correct pressure on lapped faces.
Replace D-washer (Ref 30) and impeller nut (Ref 24) holding impeller against rotation as
indicated in step 7 of disassembly procedure.
Remove any burrs caused by screwdriver on the vane of impeller in waterway passages.
Replace motor and rotating element in casing. Be sure that any damaged O-rings are
replaced.
- or -
If whole assembly was removed install O-ring on cover. Be sure that any damaged O-ring is
replaced.
Position case (Ref 1), cover (Ref 11), and motor disc (Ref 71) so the holes line up. Install
socket head cap screws through the case and cover and thread into motor disc. Tighten all
cap screws alternately and evenly until finger tight.
- or -
When whole assembly is removed place pump casing against pump cover. Ensure that
impeller eye is centered in pump case and position case, cover and motor disc so that the
holes line up. Install socket head cap screws through the case and cover, thread into motor
disc. Tighten all cap screws alternately and evenly until finger tight.
Finish tightening the cap screws alternately and evenly to approximately 6 ft. lbs. torque.
Note: It is imperative that screws be tightened alternately and evenly, as this action centers
the cover in the casing, assuring proper alignment. Binding of the impeller in the case and
adaptor may occur if the cap screws are not tightened as listed above.
Replace hold-down bolts.
Check for free rotation after assembly is completed.
Replace motor shaft end cap.
Seal all drain openings using pipe sealant on threads.
Re-prime before starting. Do not start until pump is completely filled with water.