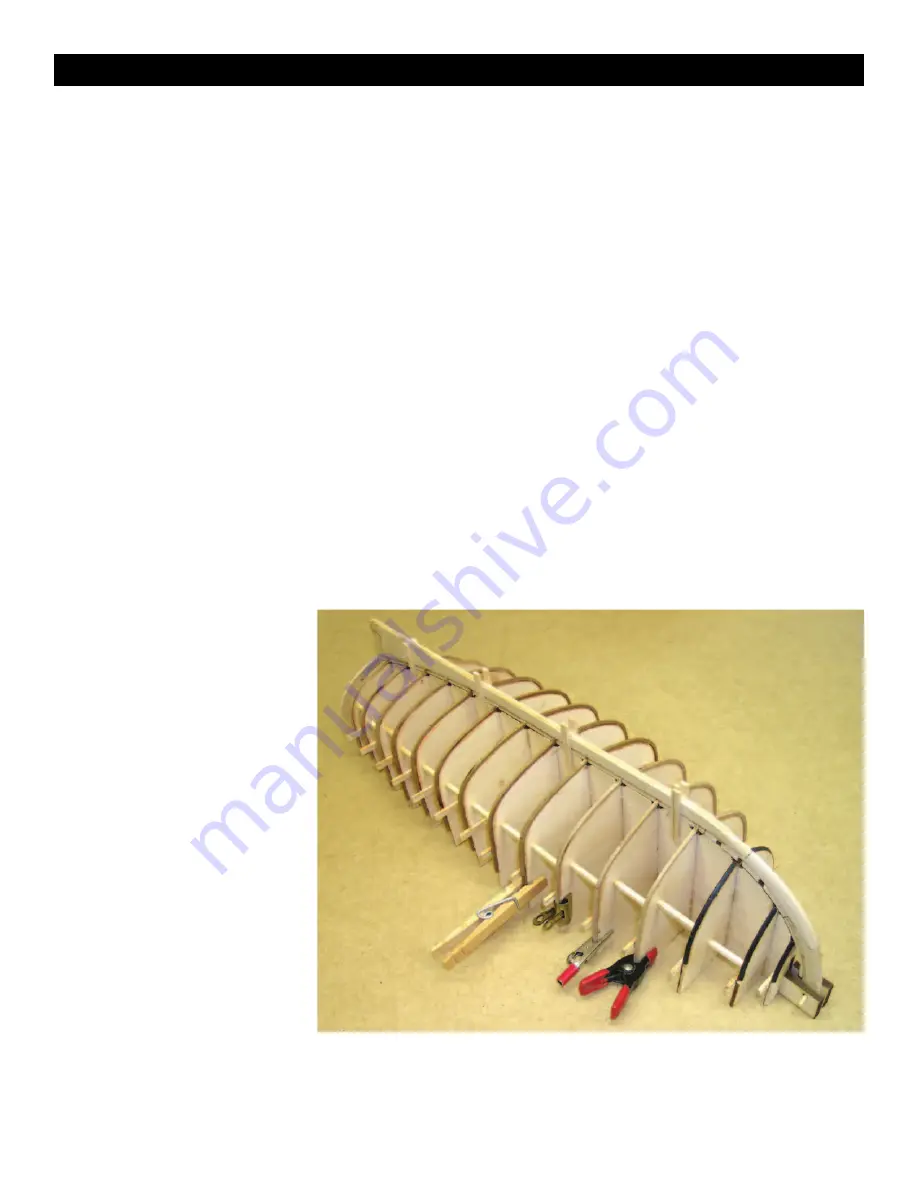
10
STAGE 2:
BENDING ON THE FRAMES
Now we are going to have some fun bending on the frames. As
previously noted this method of boat building is as in full size
practice for this size and type of boat hull. Molds were set up at
stations just as we have for the model and frames were steam bent
around them. This is a good time to note that our building jig is
not part of the boat! A word of caution, we do not want any part of
the boat to end up glued to the building jig. Therefore it is a good
idea to wax the edges of the molds lest a drop of glue later run down
and wick in between a frame and a mold. You can use paste wax,
beeswax, a candle or any other suitable wax you have around. For
the prototype a paste furniture wax applied with a brush was used.
Also a reminder that molds 1, 2, and 3, do not take frames. These
only provide shape to the bow of the boat and are lofted to the
inside of the planking, not the inside of the frames. Note in photo
10 these molds have been colored to remind the builder that planks
are not to be glued to these molds.
Some comments on bending wood. Building the launch requires
quite a lot of wood bending. Namely, the frames, planks, sheer
clamps, thwart risers, and floorboards. What we are after is to
pre-bend each piece of wood so that it will lie in it’s intended place
without undue force and/or distortion, and with a minimal amount
of persuasion. Not doing so stresses glue joints and makes the
pieces difficult to install and clamp. Wood is bent by:
Steam bending:
Hold the plank over a kettle of boiling water and
bend. Hold the wood in position until it cools. Although the plank
should remain in that shape, it may spring back slightly. Gloves are
desirable, hot steam can severely burn.
Microwave steaming:
Wrap the planks in a
wet paper towel before heating. Since
microwaves differ in wattage, experiment to
determine what power level to use and for
how long. Experiment with scrap pieces first
as it is quite possible to start a fire in your
microwave:
Soaking:
Submerge the plank in warm
water for several hours. Try adding a little
household or pure ammonia. This speeds up
the process, making the fibers slippery so the
wood bends more easily. After soaking, and
bending, clamp the plank in its intended
position until completely dry.
Soldering iron:
Large soldering irons with a
tubular end are ideal. Clamp the iron
upright in a vise. While the iron heats, soak
the strip of wood in tap water. Some model-
ers prefer bending around the tube near the
handle (it’s not as hot), while others use the
shank. Move the strip back and forth against
the iron. Its heat turns water into steam and
drives it into the wood. The trick is to wait
until you feel the wood wanting to yield
before starting the bend. Begin too soon or
apply too much pressure and the strip will break. The wood dries
rapidly, so care must be taken to avoid scorching. Re-soak and reap-
ply it to the iron until the desired shape is achieved. Once the piece
is formed, it can go directly on the model. Because the wood’s
memory has been permanently altered, it will never spring back to
its former shape, meaning no stress on any timber or fasteners.
Spend some time acquainting yourself with this method and you’ll
never bother with fixtures again.
Another soldering iron approach is to lathe-turn a tip from hard
aluminum, then file a 45° angle on one end. Insert the tip in a
20- or 30-watt soldering iron and heat it. Soak the wood for five
minutes, then let dry for five minutes. (Woods take on water faster
than they can release it.) Hold the tip against the wood to heat it.
When supple, bend the plank over a form, or simply lift the end as
heat is applied and bend by hand.
Commercial plank benders:
Model Expo sells an electric plank
bender designed for controlled heat, item no. MS7205. Another
tool (Amati’s FormAStrip available from Model Expo) bends planks
without soaking or heating. It looks like a pair of pliers with one flat
jaw and a chisel for the other. When squeezed on a plank, the chisel
depresses one side of the wood, causing it to bend. Repeat the
process along the plank until it assumes the correct curve. However,
squeezing too hard will cut the wood in half. This tool bends planks
in only one direction, so it’s good for bow planks, but not those at
the stern that are concave. This treatment is not recommended for
the launch since unlike a plank on bulkhead hull, our planks are
visible on the interior of the hull.
The frame stock supplied in the kit is 3/32 square cherry. Cherry
bends much more readily when hot and wet than does basswood.
The prototype model was built by soaking each frame in boiling
water for about 5 minutes. This can be as simple as a coffee can of
water boiling on the kitchen stove. What ever method you use it is
useful to begin bending and shaping a frame in your fingers before
Photo 10, frames 4 through 15 bent and installed