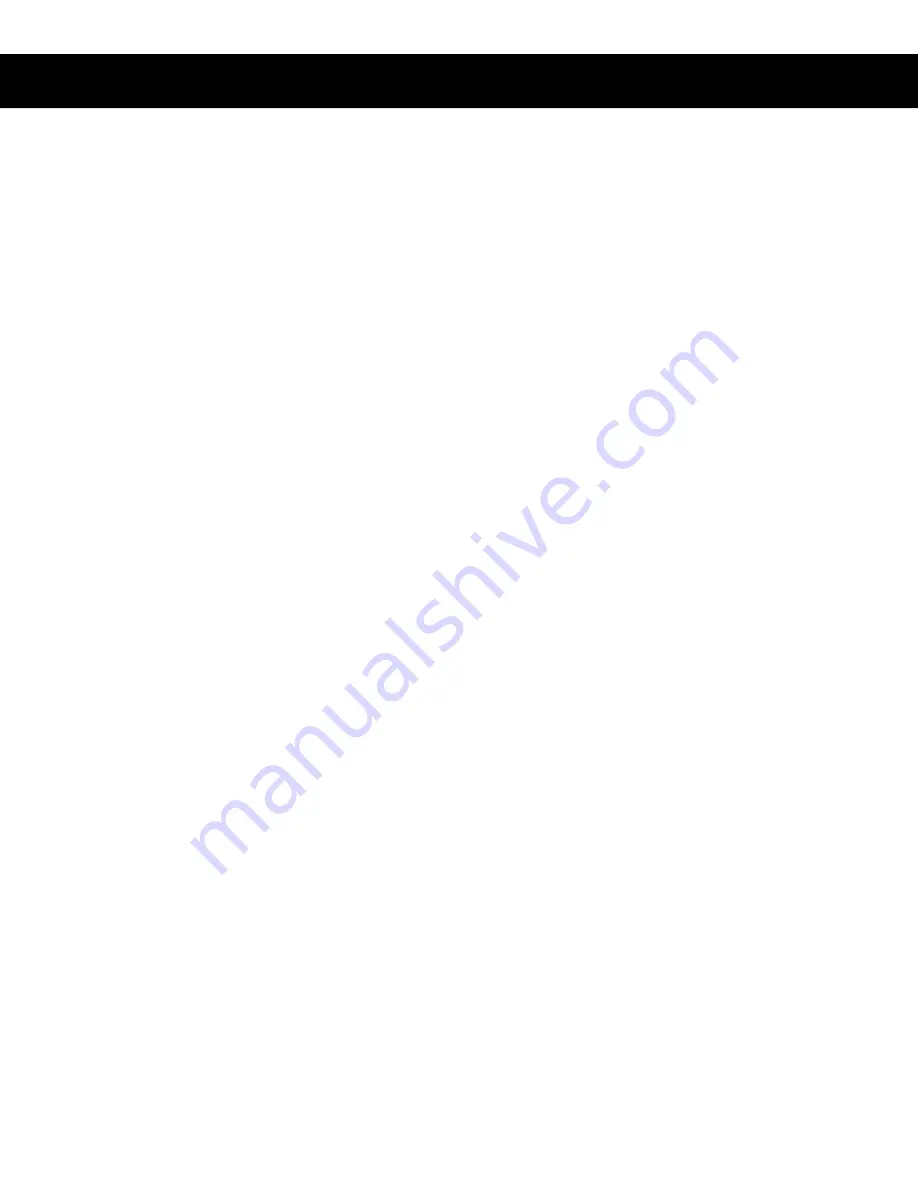
How to Work With the Plans & Parts
6
Before starting the model, carefully
examine the kit and study the plans.
First, determine if all the listed parts are
present. Handling them will quickly give
you a better understanding of the kit’s
requirements. Try to visualize how every
piece will look on the completed model.
Also, determine ahead of time what
must be done first. The instructions will
help, but a thorough knowledge of the
plans at the outset is essential.
To avoid losing small fittings and hard-
ware, sort them into labeled boxes or
compartments. These should have lids
to keep out dirt.
1. The Plans
Six plan sheets are provided:
1. Laser-Cut Wood Patterns
2. Plank-on-Bulkhead Hull
Construction
3. Hull Plan and Profiles
4. Hull and Spar Details
5. Rigging and Sails
6. Rigging Sections and Details
Sketches appear throughout the
manual to illustrate various construc-
tion techniques.
The
Charles W. Morgan
kit is manufac-
tured to a scale of 3/16” = 1’ 0” (1:64).
Each plan sheet is drawn to that scale,
except areas enlarged to show detail.
Most dimensions can be lifted directly
off the plans by using draftsman
dividers or a “tick” strip (piece of paper
such as an adding machine roll). Lay the
paper strip over the plan, carefully mark
the item’s length with a sharp pencil,
then transfer the marks to the wood.
A 3/16” architect’s scale or metric ruler
is a handy tool. Measuring and cutting
parts using the scale gives a better feel
for real sizes. Because these are model-
building plans, actual measurements
have been converted to the nearest
1/64” (0.4mm) or 1” full scale. Sheet 5
contains a table for converting imperial
numbers to metric.
2. Making Allowances
Along the Way
Try to be exact when following the
plans, but use common sense.
Adjustments may be necessary to com-
pensate for small differences in how
your model is shaping up; perhaps one
mast has too much rake (the angle at
which it sits). Lines should not drape
over fittings or conflict with other lines
when belayed (secured). If necessary,
move a belaying point or fairlead. Put
yourself on the ship, imagine perform-
ing the task, and use logic.
3. Understanding Hull Lines
Beginners may not be familiar with the
following hull lines.
Buttock
lines are
vertical longitudinal planes that cut
through the hull.
Waterlines
are horizon-
tal planes,
diagonals
are diagonal planes,
and
sections
are transverse vertical
planes. These lines define the hull’s
shape and are used by the draftsman to
fair it (create even curves).
A complete set of hull lines is not need-
ed for this model, because laser-cut
bulkheads and the center keel define the
hull’s shape. Sheet 2 shows the bulkhead
lines. They are similar to a ship’s body
plan or sections, and illustrate how the
hull curves from top to bottom. Consult
these lines when installing the bulwarks,
since the bulwark stanchions are built
separately from the lower bulkheads.
4. Using Basswood
Basswood comes in 1/32”, 3/64”, 1/16”,
3/32”, 1/8”, 5/32”, 3/16”, 1/4”, and
1/2” thick sheets and strips. Strip widths
are in the same increments, while sheets
may be 1”, 2”, 3”, or 4” wide.
Note:
Model Shipways occasionally sub-
stitutes lime (Tilia vulgaris), a European
wood, for basswood (Tilia americana) in
its kits. Both have a fine, uniform texture
and straight grain. Lime, however, has
superior steam-bending qualities. It is
often called basswood in Europe.
Based on
Morgan’s
3/16” = 1’ 0” scale,
1/64” equals 1” on the real ship, 1/32”
equals 2”, and so on. Generally, bass-
wood strips or sheets can be used as is.
Occasionally, a strip must be thinner
than the supplied size. To maintain scale,
sand the strip to the required thickness
before making the part. One way is with
a sanding block. Another is with a hobby
sanding thickness planer (sold commer-
cially). If you don’t own one, chuck a
sanding drum into your drill press, then
clamp a block alongside the drum to act
as a fence. This makeshift tool works
quite well. Sorting the wood in the kit by
thickness will save time. After selecting
and cutting what you need, return the
remaining stock to the proper thickness
pile. Don’t worry about using a piece for
one item intended for another. Model
Shipways supplies enough extra wood to
complete the model.
5. Britannia Metal Fittings
Britannia metal is a great improvement
over the white metal castings found in
older kits. Unlike white metal and
pewter, Britannia doesn’t contain lead
(it’s a tin, copper, and antimony alloy)
and won’t corrode. These fittings will
require final finishing before mounting
on the model. First, remove mold joint
flash with a No. 11 hobby blade, then
file or sand with fine sandpaper.
Second, wash fittings in dishwashing
liquid and warm water to remove traces
of mold release agent and the body oils
your fingers have deposited. Allow to
dry thoroughly before applying primer
and painting.
6. Soldering and Working
with Brass
Charles W. Morgan
sailed during a time
when iron fittings were used. To accu-
rately portray this, some soldering is
necessary. Although paper or brass
strips could be glued together as a sub-
stitute, soldering will maintain the
model’s integrity. Here are a few tips on
soldering brass strips and wires, or
scratch building with them:
Cut brass sheets and strips with a small
pair of tin snips or heavy scissors. Thicker
brass will require a jeweler’s saw. After
cutting, smooth the edges with needle
files followed by wet-or-dry fine sandpa-
per used dry. Cutting slivers from brass
sheet curls and bends it sideways. To
straighten, grip the ends with a pair of
small pliers and pull in opposite direc-
tions. Thin brass sheets can be scored
with a utility knife and metal straight-
edge, then snapped off. Use two or three
light passes, cutting against a maple chop-
ping block, birch board, or glass backing.
Drilling holes in brass with a pin vise is a
slow process. The solution is to mount a
handpiece for flex-shaft machines in a
hobby drill press. Several companies
manufacturer this tool and it is worth the
cost. When working with brass, use a
1/4” or thicker piece of maple or birch