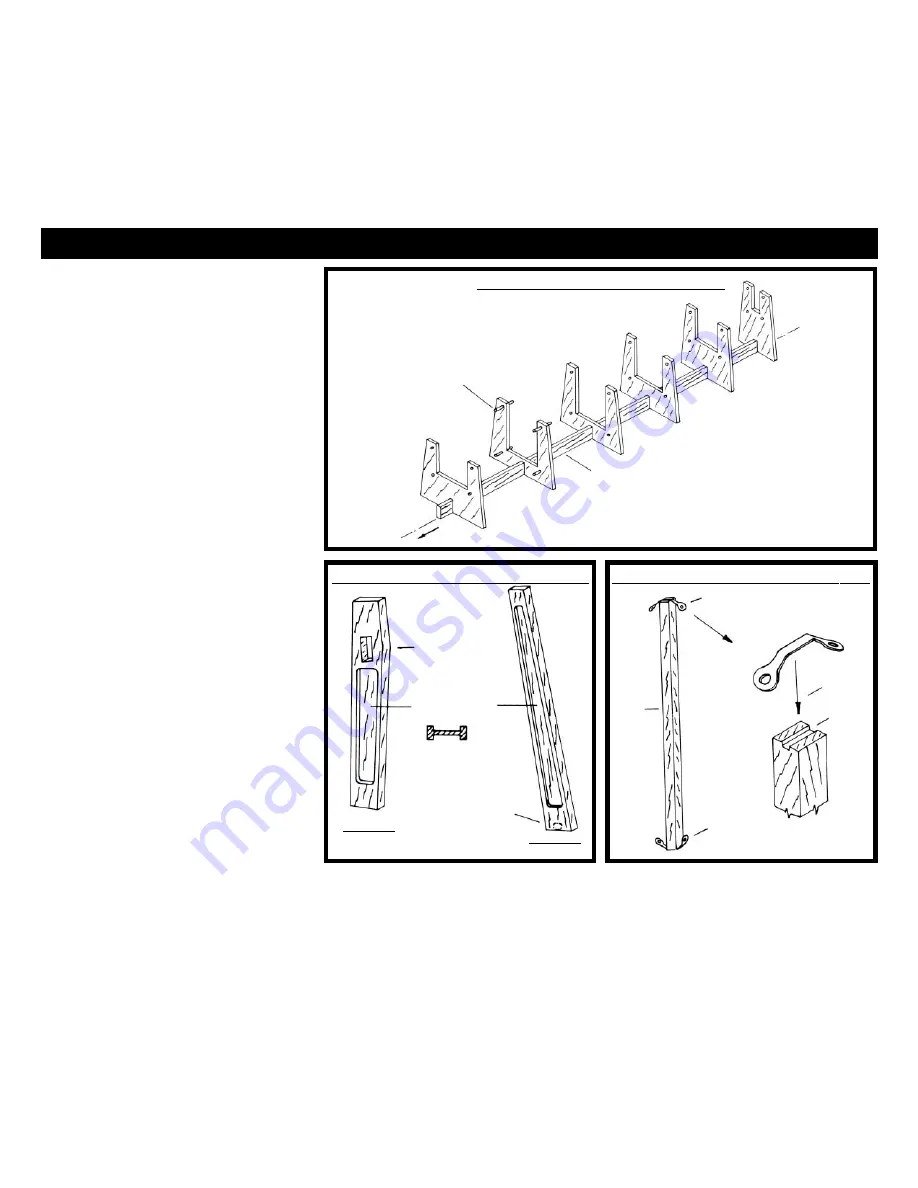
16
Plan Sheet 3 shows all the details for construct-
ing the basic fuselage. The plan also shows the
cross bracing wires for the fuselage and the alu-
minum cockpit cowl. However, do not install
the cockpit cowl or any brace wires that would
interfere with installing cockpit controls. The
cowl and some wires would get in the way
when installing cockpit controls, seats, etc. The
instrument panel fittings should be installed
during this stage, as it is easier to place these in
the instrument panel formers before the form-
ers are installed. The landing gear, remaining
cockpit controls, and engine installation will
also be discussed in later stages. The following
parts are required for this stage:
Laser-Cut Wood Parts
Forward instrument panel former – 1 of F1
Aft instrument panel former– 1 of F2
Turtleback formers – 1 each of F3 through
F10
Fuselage building jig center piece – 1 of F26
Fuselage building jig formers – 1 each of
F27 through F32
Britannia Castings
Oil pressure gauges – 2 of E1
Altimeters – 2 of E2
Ignition Switch – 1 of E3
Air speed indicator – 1 of E4
Tachometer – 1 of E5
Water temperature gauge – 1 of E6
Photo-Etched Copper Parts
Double eye cross brace wire fitting – 24
of F11
Triple eye cross brace wire fitting – 18
of F12
Strut clips Station 6 thru11 – 24 of F13
Nose plate front piece – 1 of F14
Nose plate side pieces – 2 of F15
Upper strut clip Station 2 – 2 of F16
Lower strut clip at Station 2 – 2 of F17
Upper strut clip at Station 3 – 2 of F18
Lower strut clip at Station 3 – 2 of F19
Upper strut clip at Station 4 & 5 – 4 of F20
Lower strut clip at Station 4 and 5 – 4 of F21
Step plate – 1 of F22
Single eye rig fitting – 32 of R1
Turnbuckles – 82 of R3A (short)
Steel Rod
Tail skid support rods – 1/32"-dia. rod
Wood Strips
(cut to length as required)
Turtleback stringers – 1/32" x 3/64"
Floor boards and shelf behind the rear
cockpit – 1/32" x 1/2"
Vertical and horizontal struts and vertical
longitudinal seat rail struts – 1/16" x 1/16"
STAGE 3:
BUILDING THE BASIC FUSELAGE
FIG. 3-1 FUSELAGE BUILDING JIG
F26 – CENTER PIECE
F27
TYPICAL 1/8"
DOWEL AT
EACH FORMER
F28
F29 – FORMERS
F30
F31
F32
FRONT
FIG. 3-3 STRUTS AT STATIONS 6 TO 11
1/16"
SQUARE
USE
SUPER
GLUE
FILE
GROOVE
F11
F11
top and bottom of the ribs like the stringers
of the wing ribs. These notches are not
laser-cut into the elevator ribs for fear the
rib may break between the upper and lower
notches before assembly.
After removing the elevator from the build-
ing board, add copper tape and the fittings
for the control cable brace wires (R2) at the
trailing edge in way of the ribs. Mount the
control horns (C2), then add the lower cap
strips to the ribs. Cut slots for the fake
hinges in the leading edge, then assemble
the elevator to the horizontal stabilizer using
brass strip as fake hinges.
Figure 2-4
illustrates the elevator assembly.
5. Mounting the Vertical Stabilizer
Now is a good time to mount the vertical
stabilizer on top of the horizontal stabilizer.
Simply glue this on top of the center hori-
zontal stabilizer rib cap strip. Make sure it
is vertical. On the real aircraft the vertical
stabilizer is bolted on.
You can install the brace wires at this time
using the 0.010" gray nylon cord. Short turn-
buckles (R3A) are located at the horizontal
stabilizer end.
Like the wings, store the completed tail sur-
faces and struts in a safe place until they are
ready to be installed on the fuselage.
FIG. 3-2 STRUTS AT STATIONS 3, 4 & 5
HOLE FOR
ENGINE BEARER
SUPPORT BEAM
STATION 3
STATION 4
(5 SIMILAR)
HOLE FOR FAKE LOWER
WING HINGES –
DRILL LATER TO
MATCH WING
MORTISE BOTH
SIDES
Longerons – 1/16" x 3/32"
Engine support beam – 3/32" x 3/16"
Engine bearers – 1/8" x 3/16"
Longitudinal and transverse seat rails
and strut between rails – 1/16" x 1/8"
Floor board supports, large vertical struts
(Stations 4 & 5) and tailpost – 1/16" x 3/16"
Large vertical struts (Station 3) – 1/16"
x 1/4"
Wood Dowels
(cut to length as required)
Fuselage building jig dowel pins –
1/8"-diameter
Rigging Cord
(cut to length as required)
Fuselage cross bracing wires – 0.010"-
diameter gray nylon cord
Wrapping cord for splices – 0.008"-diam-
eter black nylon cord
1. Building the Fuselage Jig
The fuselage sides can be assembled directly
on the plan like the wings. Then, the sides
will be transferred to a building jig. The jig
will hold the sides in the correct shape so the
top and bottom struts can be added, result-
ing in a correctly shaped fuselage.
Start by assembling the laser-cut building
jig. Assemble the jig on a rigid board like a
plywood board or particle board (not sup-
plied in the kit). First, draw a straight guide
line on the board. Tack or glue (or both) the
jig center piece (F26) to the board, using the
drawn line to get it straight. Next, insert a
1/2" long piece of 1/8" dowel through each of
the round holes in all the laser-cut formers