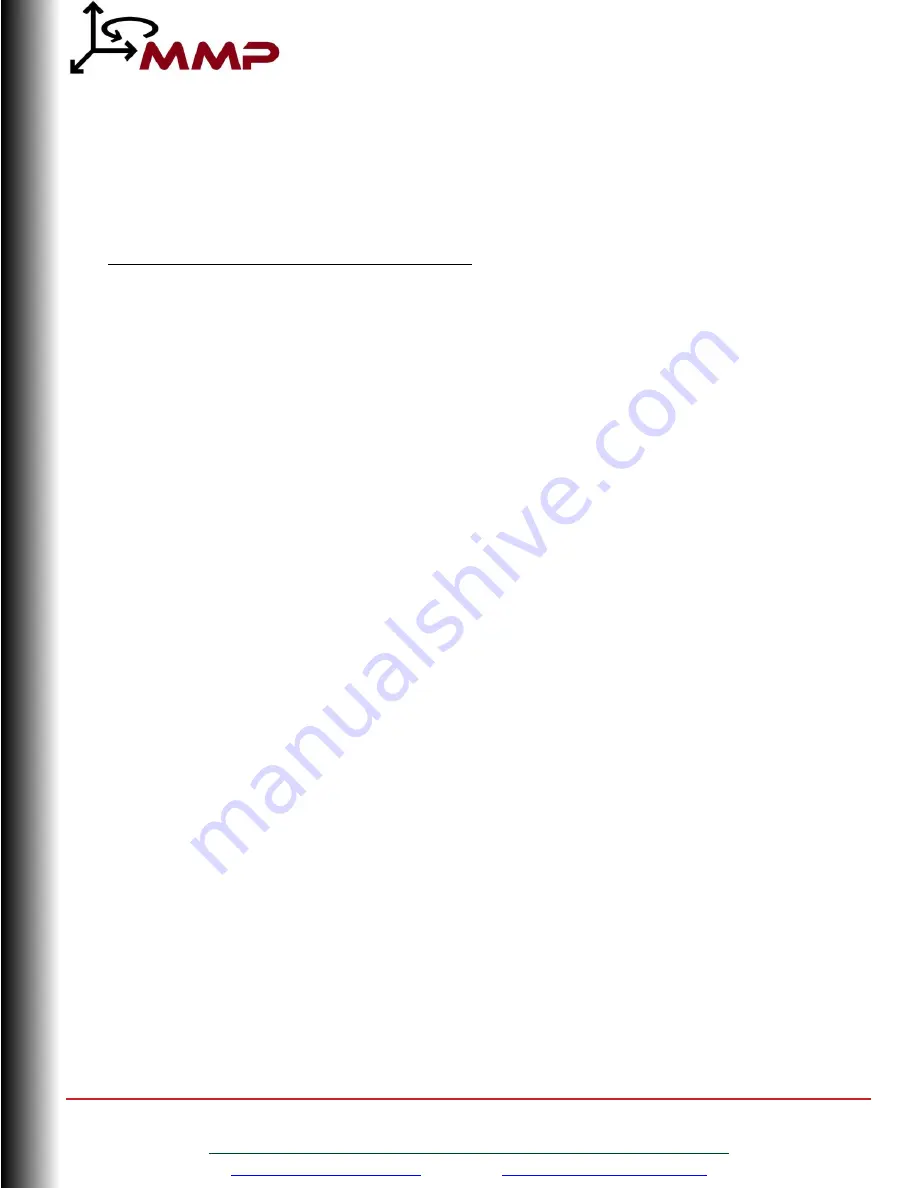
MMP SA-2550A
Page 19 of
24
Midwest Motion Products
DESIGN, MANUFACTURING & DISTRIBUTION - MOTION CONTROL EQUIPMENT
email:
TROUBLESHOOTING GUIDE
Below are covered common questions and issues related to the SA-2550A servo amplifier.
1.
What a red LED indicator means and how to fix it.
2.
How to perform current loop tuning on the SA-2550A.
3.
Adjusting the Command Signal Curve using the built in potentiometers of the SA-2550A servo amplifier.
1.
Red LED indicator meaning and methods of correction
A red LED can indicate any of the following fault conditions:
Over-voltage
Under-voltage
Invalid Hall State
Drive Inhibited
Over-temperature
Short circuit
Over-current
Power-on Reset
Fault conditions are non-latching, meaning that when the fault condition is removed, the drive will enable (green LED).
Troubleshooting Instructions
1.
Remove all connections from the drive. This includes the voltage supply, motor power cables, feedback and any controller I/O.
2.
For a brushed drive, configure the amplifier for voltage mode. For a brushless drive, configure the amplifier for open loop
mode. The switch settings for each mode can be found on the drive datasheet.
3.
If using a brushless drive, set the 60 / 120 phasing switch to 60 degrees, which is the OFF position.
4.
Apply power to the drive. If the drive has inverted inhibits, short the master inhibit pin to signal ground (for more information
on inverted inhibits, see Drive Inhibited section). The LED should be green. The drive will fault if too much or too little
voltage is applied to the drive. See Over-voltage and Under-Voltage section for details on this fault condition.
5.
Remove power from the drive. If using a brushless motor, connect Hall sensor inputs and set the 60 / 120 phasing switch to
the correct position according to the motor. Apply power to the drive and rotate the motor by hand. If the LED is red or
changing between red and green, this could indicate an issue with the Hall sensor inputs. See Invalid Hall State section for
details on this fault condition. Note: Most motors have 120 degree Hall sensors.
6.
Remove power from the drive and connect motor power cables. Set the Test/Offset switch to the OFF position and set POT4,
the Test/Offset pot, 7 turns from the full clockwise direction.
7.
Apply power. If the LED is red, it could be an indication of a short circuit fault. See Short Circuit section for details on this
fault condition.
8.
Remove power and connect the controller. Remove any command from the controller to avoid unexpected motion in the motor.
9.
Apply power. If the LED is red, check if the controller is disabling the drive. See Drive Inhibited section for more information
about the inhibit input.
Fault Conditions Explained
Over-voltage and Under-voltage
An over-voltage fault occurs when the bus voltage exceeds the over-voltage limit of the drive. An under-voltage can occur if too
little voltage is applied to the drive. The voltage rating can be found on the drive datasheet.
For DC input drives, verify that the DC input voltage is within the spec of the drive.
For AC input drives, verify that the AC input voltage is within the spec of the drive.
Regeneration
If the drive faults during a deceleration or when lowering a vertical load, it could be due to regeneration energy raising the bus
voltage beyond its over-voltage limit.
During these types of moves, the system’s mechanical energy gets converted into electrical energy that flows back onto the DC
bus. This charges the capacitors in the power supply and raises the DC bus voltage.
MIDWEST M
O
TION
P
RODUCTS