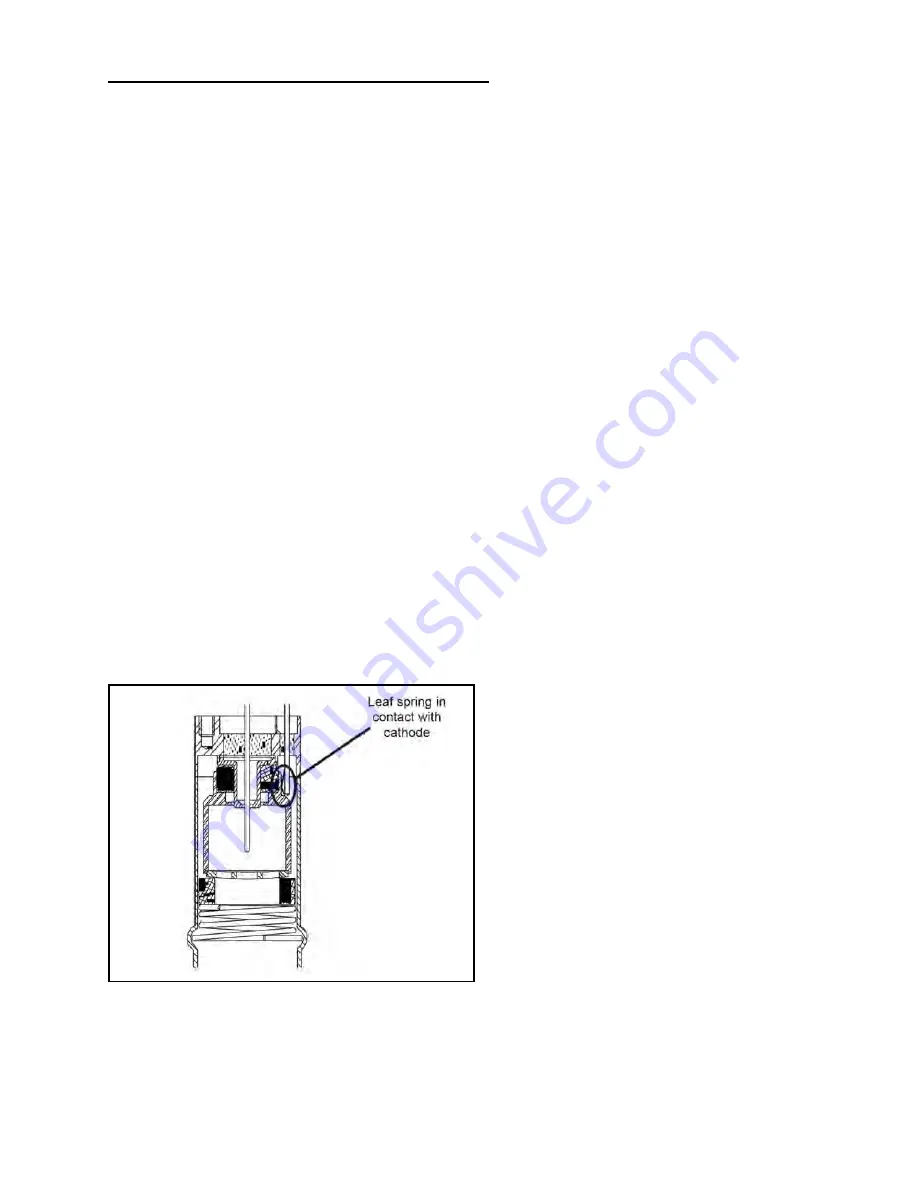
6
Service & Maintenance
40
Series 943 Cold Cathode Vacuum Sensor
Instruction Manual - #100009887
6.5.3 Reassemble the Sensor
1.
Check the anode (8). It should be straight and centered with the sensor body (7) for proper
operation.
2.
Roll the sensor body on a flat surface and look for any radial run out motion.
3.
Install the ground shield 6 using tweezers. Make sure that at the groove of its larger diameter,
the ground shield interlocks with the locating collar 11.
4.
Slide the small ceramic spacer 5 over the small end of the ground shield 6. Check that the leaf
spring 9 will contact the base of the cathode 4 as shown to the right. If not, remove the small
ceramic spacer and the ground shield. Gently bend the leaf spring towards the anode and
ceramic spacer.
5.
Slide the cathode 4, the grid washer 3, and the large ceramic spacer 2 into place. The grid
washer has a concave shape. Refer to the figure to see its installation orientation.
6.
Insert the small end of the compression spring 1 into the sensor body 7. Using your thumbs,
push the larger end of the spring into the sensor body until it is contained within the tube's
inside diameter. Using the smooth-jaw, needle-nose pliers, work the compression spring down
into the sensor body until it is fully seated in the formed groove.
7.
Inspect the ground shield 6 and the grid washer 3 to verify they are centered with respect to
the anode 8. If adjustment is needed, gently reposition the grid washer/cathode assembly,
taking care not to scratch the grid washer.
8.
Measure the resistance between the ion current feed through pin 13 and the grid washer 3 to
verify that the leaf spring 9 is in contact with the cathode 4. The measurement should indicate
a short circuit between them. There should be an open circuit between the ion current feed
through pin 13 and both the high voltage feed through pin 10 and sensor body 7.
9.
The Sensor is ready for installation. If it is not immediately installed, cover the flange with a
clean vacuum grade cap / flange protector.
Figure 6-2: Proper Installation of Leaf Spring and Cathode (Step 8)