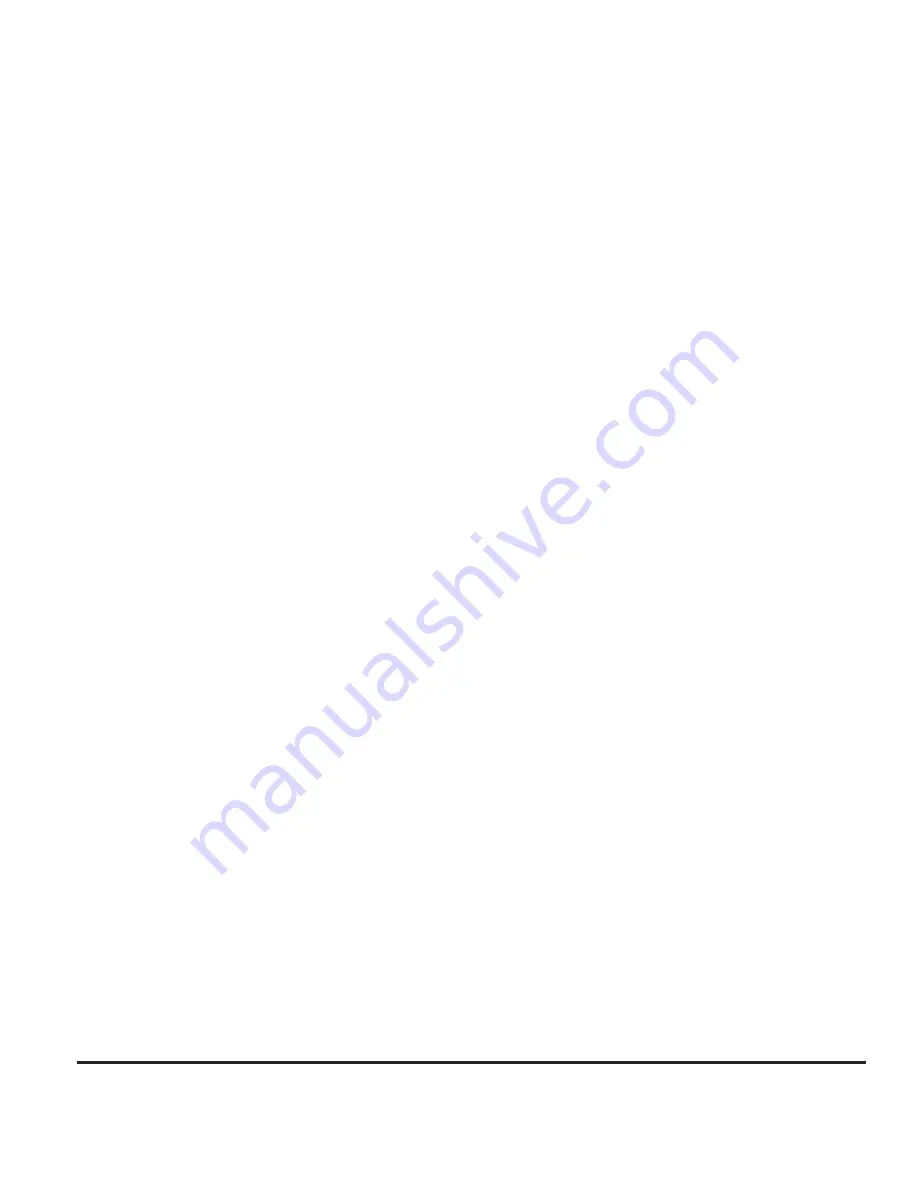
875DP/500DP/500HV DUAL PULSE
RESISTANCE WELDING POWER SUPPLIES
990-290
INDEX-1
Index
-A-
Accessory port ...................................... A-21
Air actuated weld head:
Adjustments ....................................
4-1
Connections ....................................
2-5
Excessive air pressure results ......... 4-5
Air valve driver connections................. 2-6, A-15
Air valve driver specifications.............. A-15
Alarms
.......................................
A-15
Application of system ........................... 1-1
Audible buzzer...................................... A-14
-B-
Basic weld function .............................. 6-5
Binary Schedule Selection Code........... A-19
Buzzer, audible ..................................... A-14
-C-
Calibration .......................................
7-1,
7-8
Capacitor bank:
Specifications..................................
A-1
Caution, definition of............................ iv
Chain schedules feature ........................ A-13
Charge inhibit ....................................... A-18
Circuit breakers..................................... 2-3, A-22
Components:
Front
panel ......................................
3-1
Rear
panel .......................................
2-3
Connections:
3-wire firing switch......................... 2-4
Air actuated weld heads.................. 2-5, 2-7
Air valve driver............................... 2-6, A-15
Control
signals ................................
A-16
Footswitch
.......................................
2-7
Mechanical firing switch ................ 2-4
Non Unitek Peco air actuated
weld
heads..........................
2-7
-C- (continued)
Optical firing switch ....................... 2-4
Second air head............................... 2-7
Controls, front panel ............................. 3-1
CONTROL SIGNALS connector......... A-16
Cool time definition.............................. A-9
Cooling, 875DP .................................... A-24
Cover removal ...................................... 7-1
CPU, microprocessor............................ A-23
-D-
Debounce time, switch.......................... A-11
Declaration of Conformity.................... following
CE Operator Guide
Default parameters, system................... A-8
Destructive testing ................................ 5-8
Dimensions ........................................... A-25
Display.................................................. A-23
Display screen flowchart ...................... 3-4
Display screen formats ......................... 3-3
-E-
Electrode force considerations.............. 5-7
Electrode maintenance.......................... 5-9
Electrode materials, recommended....... 5-3
Electrode sticking ................................. 5-6
Emergency stop .................................... A-17
End of cycle buzzer .............................. A-14
Excessive air pressure in weld head ..... 4-5
-F-
Factory repair service ........................... 7-11
Features of system ................................ 1-2
FIRE state ............................................. 6-4
Firing switch connections:
3-wire
......................................
2-4,
A-11
Mechanical......................................
2-4,
A-11