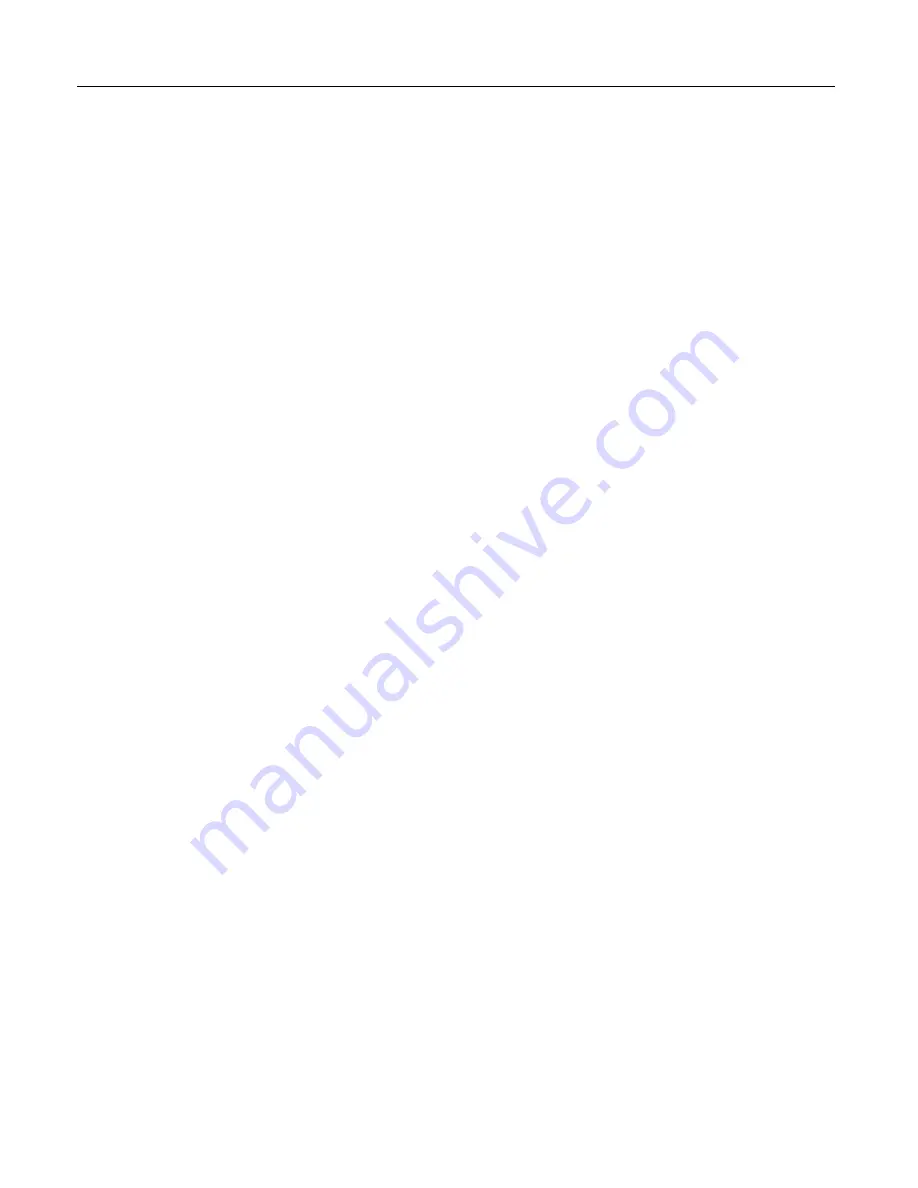
Table of Contents
iv
Table of Contents
Important Safety Information ....................................................................... i
Introduction ................................................................................................. ii
Definition of Terms ..................................................................................... iii
SECTION 1
SAFETY ..................................................................... 1
1.
Safety Regulations ............................................................................... 1
2.
Safety-related Knowledge and Expertise ............................................. 1
3.
Protective Equipment ........................................................................... 1
4.
Prohibition of Unapproved Modification ............................................... 1
5.
Warning Labels on the Product Main Unit ............................................ 2
6.
Safety Precautions ............................................................................... 3
6.1
Safety Precautions for Installation .................................................................. 3
6.2
Safety Precautions for Use of the Equipment ................................................. 4
6.3
Safety Precautions for Relocation or Resale (excerpt from page 51- of the text)
4
SECTION 2
OVERVIEW ................................................................ 5
1.
Product Overview ................................................................................. 5
1.1
Features and Functions .................................................................................. 5
1.2
Configuration .................................................................................................. 6
1.3
Specifications.................................................................................................. 7
1.3.1
Common Specifications .......................................................................... 7
1.3.2
Pressure Controller MP1-200 ................................................................. 8
2.
Component Names and Functions ....................................................... 9
2.1
Pressure Controller MP1-200 ......................................................................... 9
2.1.1
Control Panel ......................................................................................... 9
2.1.2
Internal Structure .................................................................................. 10
2.2
MI Terminal MT1-200 .................................................................................... 11
2.2.1
Control Panel ....................................................................................... 11
2.2.2
Internal Structure .................................................................................. 12
Summary of Contents for MP1-200
Page 2: ...Date of preparation May 2012...
Page 62: ...SECTION 7 APPENDIX 54 MEMO...
Page 63: ...MEMO...