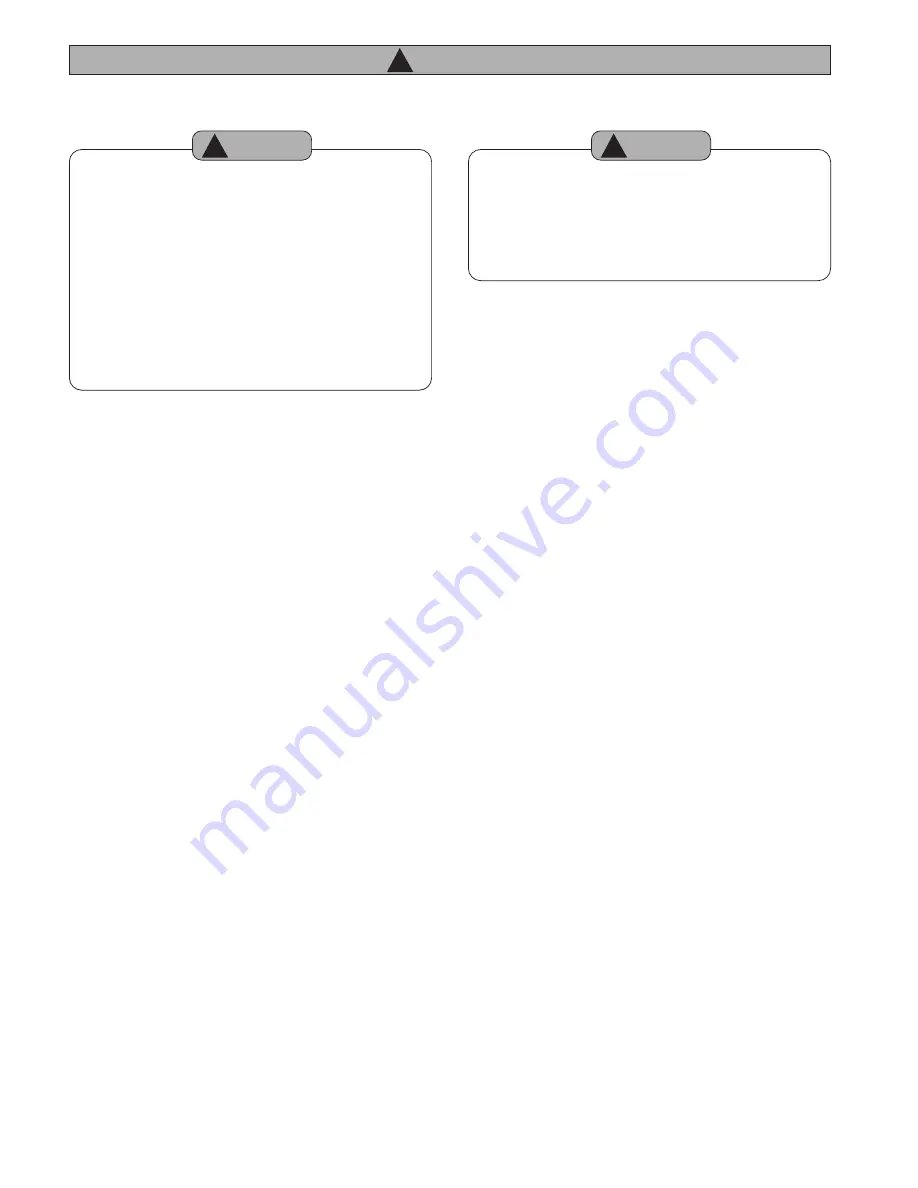
The serviceman or mechanic may be unfamiliar with
many of the systems on this truck. This makes it
important to use caution when performing service
work. A knowledge of the system and/or components
is important before the removal or disassembly of any
component.
Because of the size of some of the truck components,
the serviceman or mechanic should check the weights
noted in this Manual. Use proper lifting procedures
when removing any components.
Following is a list of basic precautions that should
always be observed.
1.
Read and understand all warning plates and decals
on the truck before operating, lubricating or
repairing the product.
2.
Always wear protective glasses and protective
shoes when working around trucks. In particular,
wear protective glasses when pounding on any part
of the truck or its attachments with a hammer or
sledge. Use welders gloves, hood/goggles, apron
and other protective clothing appropriate to the
welding job being performed. Do not wear loose-
fitting or torn clothing. Remove all rings from
fingers when working on machinery.
3.
Do not work on any truck that is supported only by
lift jacks or a hoist. Always use blocks or jack
stands to support the truck before performing any
disassembly.
4.
Lower the forks or other implements to the ground
before performing any work on the truck. If this
cannot be done, make sure the forks or other
implements are blocked correctly to prevent them
from dropping unexpectedly.
5.
Use steps and grab handles (if applicable) when
mounting or dismounting a truck. Clean any mud
or debris from steps, walkways or work platforms
before using. Always face truck when using steps,
ladders and walkways. When it is not possible to
use the designed access system, provide ladders,
scaffolds, or work platforms to perform safe repair
operations.
6.
To avoid back injury, use a hoist when lifting
components which weigh 23 kg (50 lb.) or more.
Make sure all chains, hooks, slings, etc., are in
good condition and are of the correct capacity. Be
sure hooks are positioned correctly. Lifting eyes
are not to be side loaded during a lifting operation.
7.
To avoid burns, be alert for hot parts on trucks
which have just been stopped and hot fluids in
lines, tubes and compartments.
8.
Be careful when removing cover plates. Gradually
back off the last two bolts or nuts located at
opposite ends of the cover or device and pry cover
loose to relieve any spring or other pressure, before
removing the last two bolts or nuts completely.
9.
Be careful when removing filler caps, breathers and
plugs on the truck. Hold a rag over the cap or plug
to prevent being sprayed or splashed by liquids
under pressure. The danger is even greater if the
truck has just been stopped because fluids can be
hot.
SAFETY
The proper and safe lubrication and maintenance
for this forklift truck, recommended by Mitsubishi
forklift truck, are outlined in the OPERATION &
MAINTENANCE MANUAL for these trucks.
Improper performance of lubrication or maintenance
procedures is dangerous and could result in injury or
death. Read and understand the OPERATION &
MAINTENANCE MANUAL before performing any
lubrication or maintenance.
WARNING
!
Do not operate this truck unless you have read
a n d u n d e r s t a n d t h e i n s t r u c t i o n s i n t h e
O P E R AT I O N & M A I N T E N A N C E M A N U A L .
Improper truck operation is dangerous and could
result in injury or death.
WARNING
!
WARNING
!