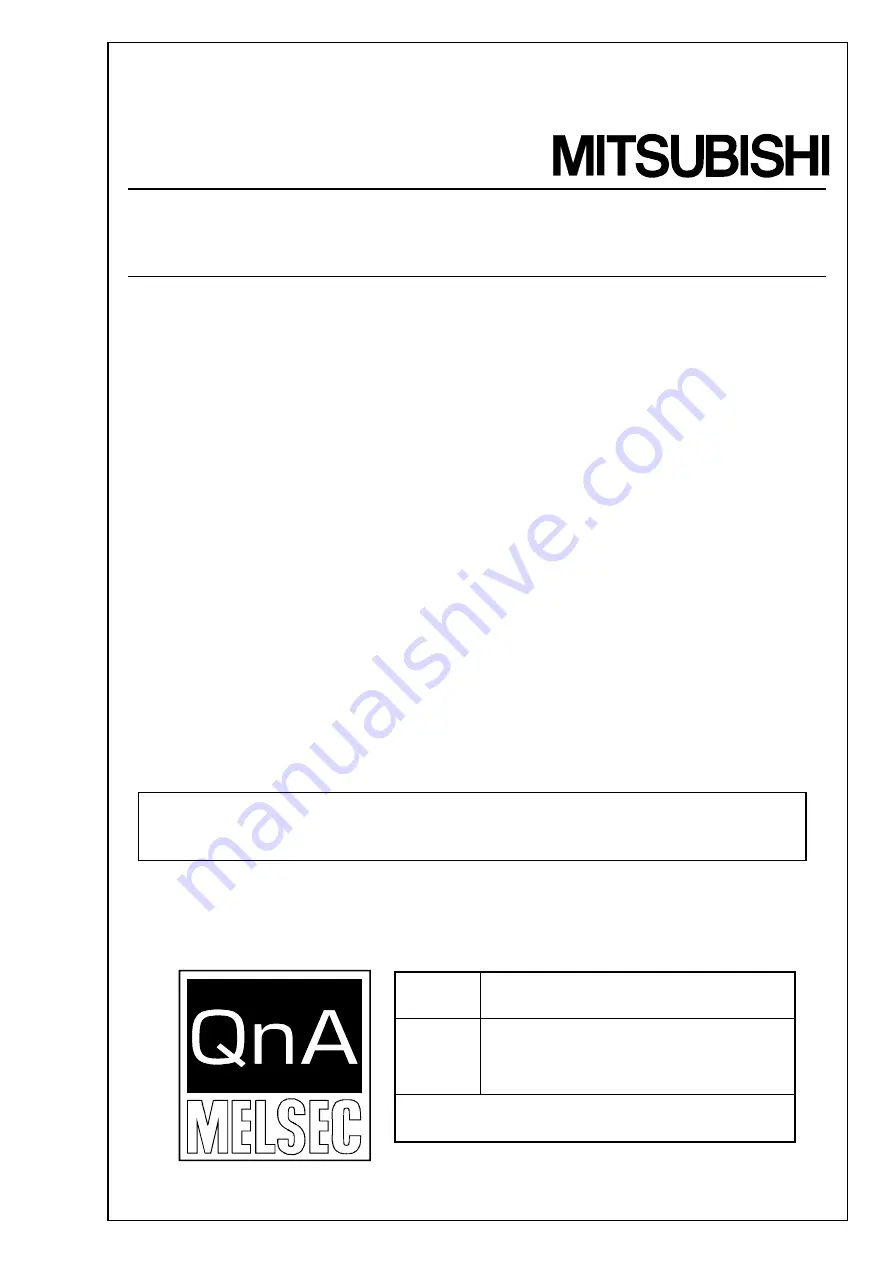
Q4ARCPU
Mitsubishi Programmable Logic
Controller
User's Manual
(Hardware)
Thank you for purchasing the Mitsubishi programmable logic controller
MELSEC-QnA Series.
Prior to use, please read both this and relevant manuals
thoroughly to fully understand the product.
MODEL
Q4ARCPU-U(H/W)-E
MODEL
CODE
13J851
IB(NA)-66684-G(0705)MEE
©1996 MITSUBISHI ELECTRIC CORPORATION
Summary of Contents for 13J851
Page 2: ......
Page 95: ...82 MEMO...
Page 101: ...88 MEMO...
Page 268: ...255 MEMO...
Page 269: ......