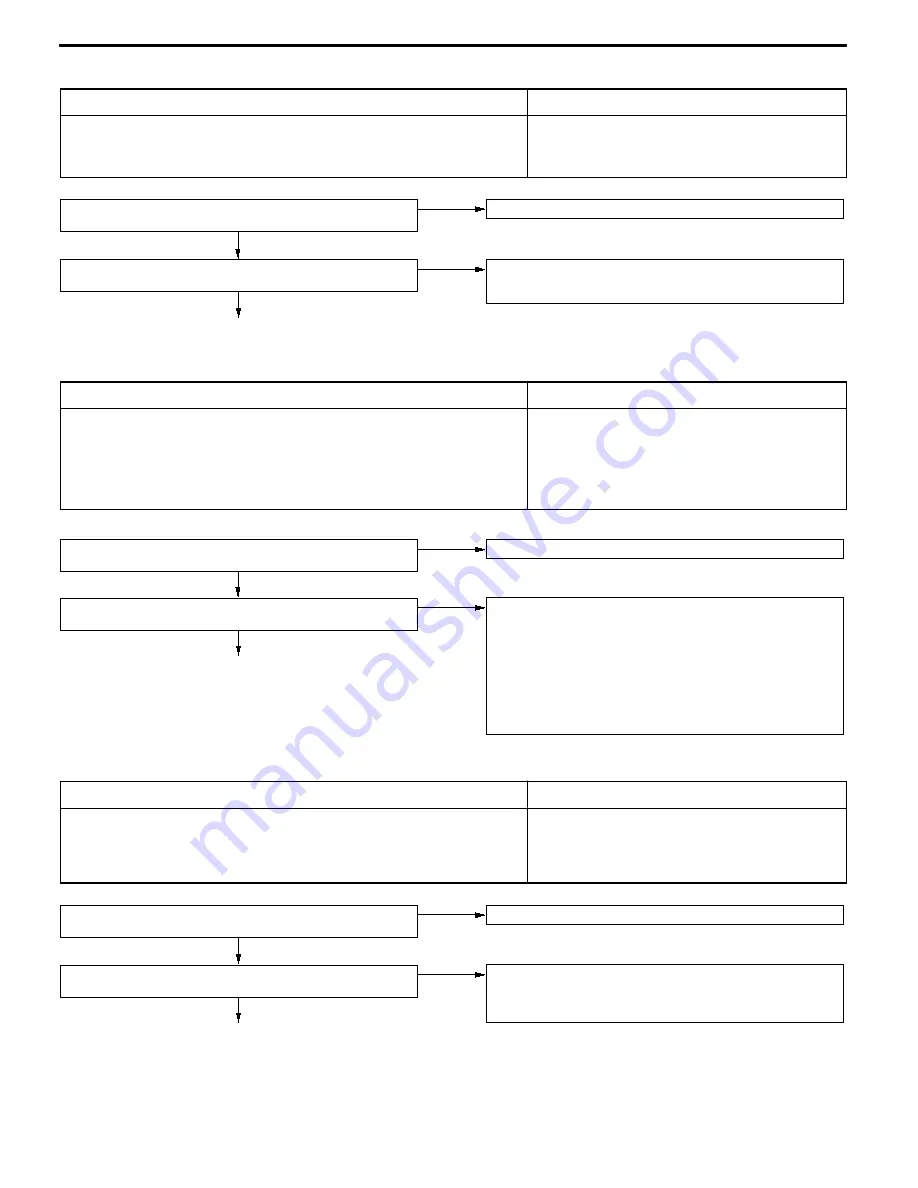
FUEL SYSTEM <4D5-step
III
> -
Troubleshooting
13-34
INSPECTION PROCEDURE 10
Low idling speed (improper idling speed)
Probable cause
Probable causes can be found in troubles with control system, injection pump,
and fuel.
D
Control system inoperative
D
Injection pump inoperative
D
Fuel system inoperative
D
Engine-ECU inoperative
NG
Repair
MUT-
II
Self-Diag code
Is a diagnosis code output?
YES
Inspection chart for diagnosis codes (Refer to P.13-9.)
NO
Conduct MUT-
II
Data list check and an actuator test.
(Refer to P.13-42, 46.)
OK
Inspect the following items in order:
D
Injection nozzle
D
Injection pump
INSPECTION PROCEDURE 11
Idling instable (rough idling, hunting)
Probable cause
Probable causes can be found in troubles with control system, injection pump,
fuel system, glow system, intake system, and EGR system.
D
Control system inoperative
D
Injection pump inoperative
D
Fuel system inoperative
D
Intake system inoperative
D
Glow system inoperative
D
EGR system inoperative
D
Engine-ECU inoperative
NG
Repair
MUT-
II
Self-Diag code
Is a diagnosis code output?
YES
Inspection chart for diagnosis codes (Refer to P.13-9.)
NO
Conduct MUT-
II
Data list check and an actuator test.
(Refer to P.13-42, 46.)
OK
Inspect the following items in order:
D
Glow plug, glow plug relay
D
EGR system
D
Injection nozzle
D
Compression pressure
D
Valve clearance
D
Throttle body assembly
D
Injection timing
D
Fuel line bleeding
D
Injection pump
INSPECTION PROCEDURE 12
The engine stalls after running for a while.
Probable cause
Probable causes can be found in troubles with control system, injection pump,
fuel system, and intake system.
D
Control system inoperative
D
Injection pump inoperative
D
Fuel system inoperative
D
Intake system inoperative
D
Engine-ECU inoperative
NG
Repair
MUT-
II
Self-Diag code
Is a diagnosis code output?
YES
Inspection chart for diagnosis codes (Refer to P.13-9.)
NO
Conduct MUT-
II
Data list check and an actuator test.
(Refer to P.13-42, 46.)
OK
Inspect the following items in order:
D
Throttle body assembly
D
Fuel filter
D
Injection pump