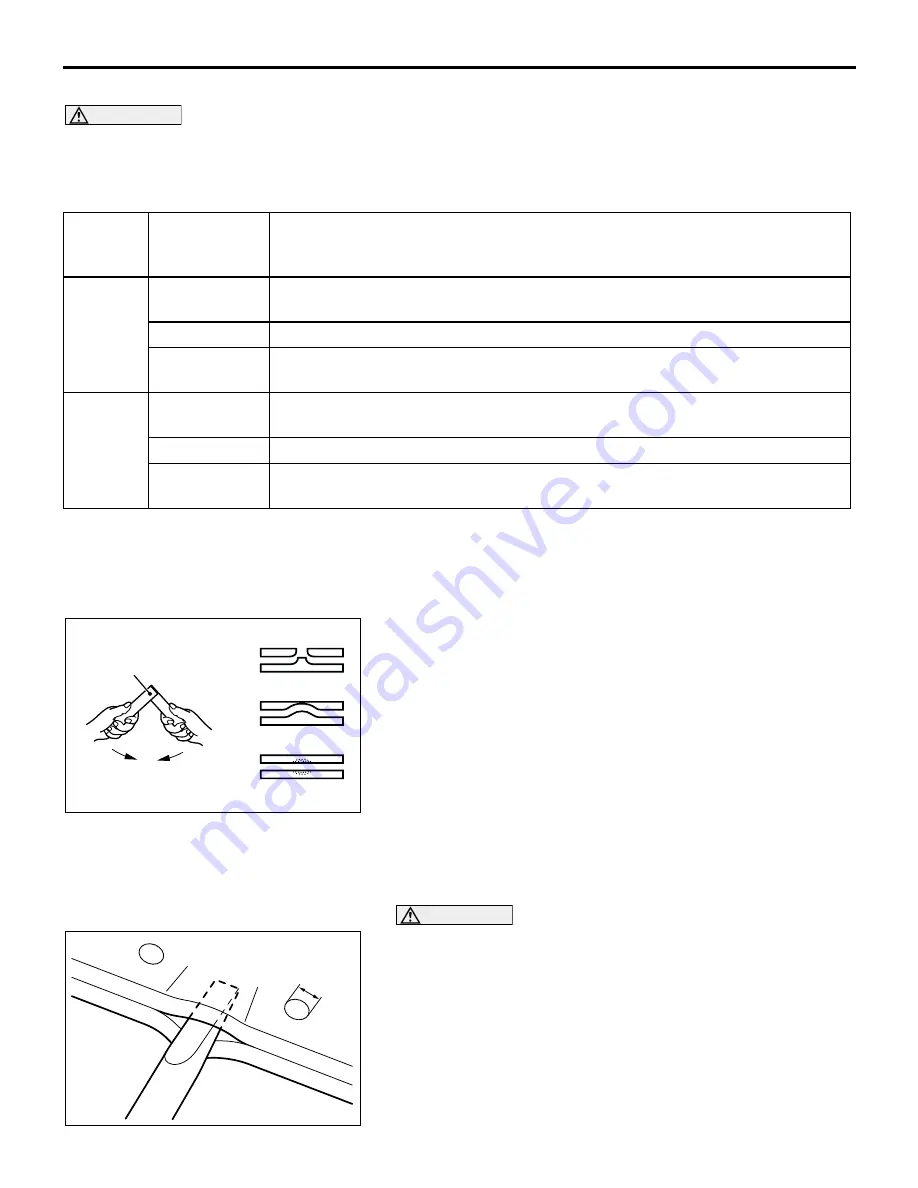
WELDING
BASE OF BODY REPAIR
9-7
Galvanized steel plate (SECC)
CAUTION
If the total thickness of the plates at the weld
places is 3 mm (0.1 inch) or more, use plug weld-
ing, because spot welding will not provide suffi-
cient welded strength.
*: For welding steel plates of different thicknesses,
conform to the welding conditions for the thinner
plate.
.
USING A TEST PIECE TO CHECK NUGGET FORMATION
Weld a test piece of the same type of steel plate as the panels
to be welded. Try to twist the piece, and also check the nugget
diameter.
Using the weld point as an axis, apply force in the direction indi-
cated by the arrows in the illustration, and determine the
strength of the weld.
1. Good (The welded part remains at one side.)
2. and 3.
The weld conditions are unsatisfactory; adjust the welding
current, the current application time, and/or the applied
pressure.
.
CHECKING NUGGET STRENGTH FOLLOWING SPOT
WELDING
CAUTION
•
Stop wedging the tip or the chisel or flat-tipped screw-
driver as soon as the size of the nuggets can be deter-
mined; do not wedge it in more than 30 mm (1.2
inches).
•
After checking the nugget diameter, correct the place
where the checking was done.
Wedge the tip of a chisel or flat-tipped (-) screwdriver into the
space between two weld points.
•
The nuggets should not break apart.
•
The nugget diameter should be 3 mm (0.1 inch) or more.
PANEL
THICKNESS*
[mm (in.)]
NUMBER OF REPAIR WELD (PERCENTAGE OF FACTORY WELD)
SAFETY
EQUIPM
ENT
AREA
0.9 (0.04) or
less
100% Same number as factory welds
1.0 (0.04)
200% Maintain pitch of at least 18 mm (0.7 inch); if not possible, plug weld.
1.2 (0.05) or
more
100% Same number as factory welds; plug welding
OTHER
AREA
0.9 (0.04) or
less
100% Same number as factory welds
1.0 (0.04)
140% Maintain pitch of at least 18 mm (0.7 inch); if not possible, plug weld.
1.2 (0.05) or
more
100% Same number as factory welds; plug welding
AB200032AB
WELD POINT
1
2
3
AB200033AB
3 mm (0.1 in)
Summary of Contents for Lancer Evolution VIII 2003
Page 14: ...36 1 GROUP 36 PARKING BRAKE CONTENTS GENERAL INFORMATION 36 2 ...
Page 27: ...NOTES ...
Page 34: ...34 1 GROUP 34 REAR SUSPENSION CONTENTS GENERAL DESCRIPTION 34 2 ...
Page 37: ...NOTES ...
Page 43: ...NOTES ...
Page 57: ...NOTES ...
Page 58: ...31 1 GROUP 31 WHEEL AND TIRE CONTENTS GENERAL INFORMATION 31 2 ...
Page 60: ...21 1 GROUP 21 CLUTCH CONTENTS GENERAL DESCRIPTION 21 2 ...
Page 70: ...27 1 GROUP 27 REAR AXLE CONTENTS REAR AXLE 27 2 DIFFERENTIAL 27 3 ...
Page 75: ...NOTES ...
Page 85: ...NOTES ...
Page 94: ...26 1 GROUP 26 FRONT AXLE CONTENTS GENERAL DESCRIPTION 26 2 ...
Page 114: ...11A 1 GROUP 11A ENGINE CONTENTS GENERAL SPECIFICATIONS 11A 2 BASE ENGINE 11A 3 ...
Page 119: ...NOTES ...
Page 126: ...13B 1 GROUP 13B FUEL SUPPLY CONTENTS GENERAL DESCRIPTION 13B 2 FUEL TANK 13B 3 ...
Page 129: ...NOTES ...
Page 130: ...25 1 GROUP 25 PROPELLER SHAFT CONTENTS GENERAL DESCRIPTION 25 2 ...
Page 132: ...16 1 GROUP 16 ENGINE ELECTRICAL CONTENTS CAMSHAFT POSITION SENSOR 16 2 ...
Page 134: ...12 1 GROUP 12 ENGINE LUBRICATION CONTENTS GENERAL DESCRIPTION 12 2 ...
Page 142: ...32 1 GROUP 32 POWER PLANT MOUNT CONTENTS GENERAL DESCRIPTION 32 2 ...
Page 144: ...14 1 GROUP 14 ENGINE COOLING CONTENTS GENERAL DESCRIPTION 14 2 ...
Page 147: ...NOTES ...
Page 161: ...NOTES ...
Page 162: ...13 1 GROUP 13 FUEL CONTENTS MULTIPORT FUEL SYSTEM MFI 13A FUEL SUPPLY 13B ...
Page 163: ...NOTES ...
Page 177: ...NOTES ...
Page 183: ...NOTES ...
Page 203: ...7 1 GROUP 7 WIRING AND PIPING DIAGRAM CONTENTS PIPING DIAGRAM 7 2 ...
Page 246: ...NOTES ...
Page 260: ...NOTES ...
Page 264: ...NOTES ...
Page 265: ...5 1 GROUP 5 SYNTHETIC RESIN PARTS CONTENTS LOCATION OF SYNTHETIC RESIN PARTS 5 2 ...
Page 268: ...NOTES ...
Page 276: ...NOTES ...
Page 283: ...FENDER SHIELD WELDED PANEL REPLACEMENT 3 7 NOTES ...
Page 368: ...NOTES ...