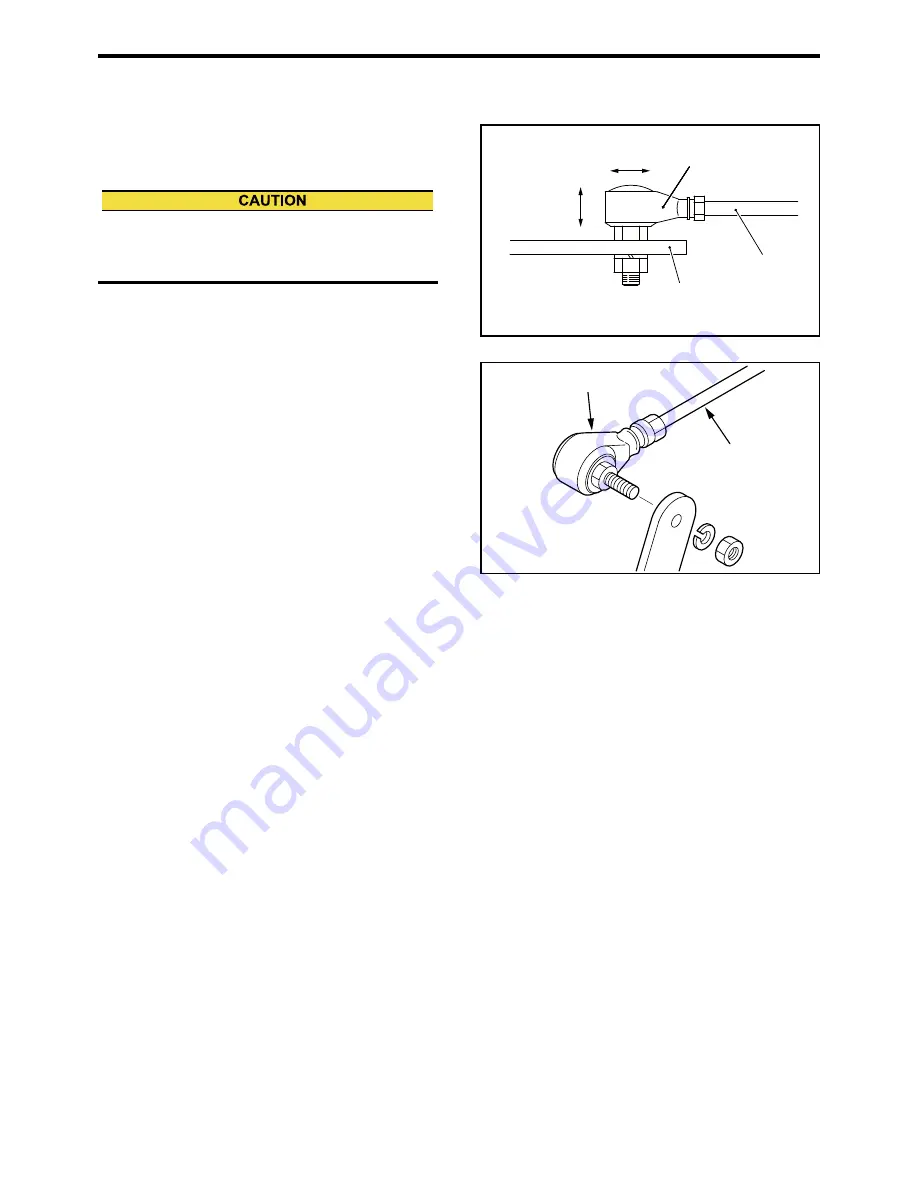
8-11
Chapter 8 PERIODIC INSPECTION AND MAINTENANCE PROCEDURES
Fuel Control Link Ball Joint - Inspect
Check ball joint in the fuel control link for play. If the
amount of play is 0.1 mm [0.004 in.] or more, replace
the ball joint with the new one.
If the ball joints are integrated in the control link,
replace the control link when the ball joints have loos-
ened. When installing ball joints, be sure to tighten the
nuts firmly.
Fig. 8-12 Ball Joints For Looseness - Inspect
Fig. 8-13 Fuel Control Link - Remove
If the sealed ball joints are found loosened, contact a
dealer of Mitsubishi Heavy Industries, Ltd. If the seal
on the ball joint is broken, the warranty is invalidated.
Ball joint
Rod
Lever
0.1 mm
[0.004 in.]
0.1 mm
[0.004 in.]
Ball joint
Control link