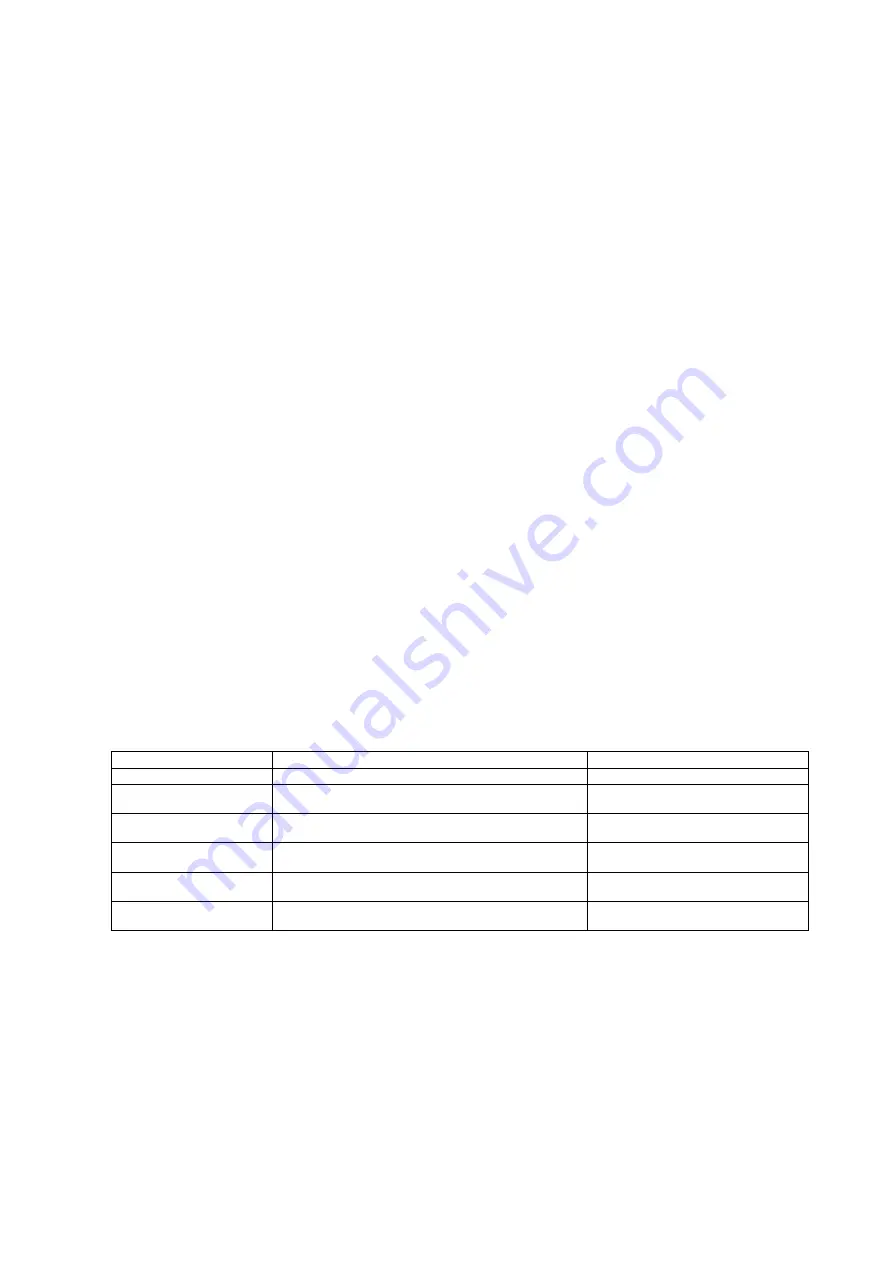
– 12 –
12
. SERVICING OF COILS AND INSULATION
(1) When coil has absorbed moisture
Measure the insulation resistance with a megger tester when the coil has absorbed moisture during shipment,
storage or when the motor has been stopped for a long time, and at the times specified in the maintenance plan. If
this measurement value drops suddenly, dry the coil. It is recommended to use the motor at 100M
Ω
or more. If the
insulation resistance is lower than the following value, do not use the motor.
Low voltage motor : 500V megger for one min., 1 (M
Ω
) at 40°C
Space heater
: 500V megger for one min., 1 (M
Ω
) at room temperature (before charging)
To dry the coil, disassemble the motor, and use the following method until the insulation resistance is restored.
a. Place the coil in an oven that does not exceed 90°C.
b. Cover the motor with a piece of canvas or equivalent material, open a hole at the top so the moisture can
escape, and dry by blowing hot air, or using a heating device or lamp. Adjust the temperature so that it does not
exceed 90°C and cause partial heating.
(2) When coil is dirty
If the coil is dirty or if the insulation resistance cannot be restored even when the coil is dry, clean the coil with the
following method.
a. Wipe dust on the coil off, or wash the coil with a cleaning solvent using hot water or low pressure steam. After
cleaning, rinse the coil with clean water.
b.
If the dust cannot be removed with the solvent, wash the coil with a cloth or brush and volatile oil,
gasoline or carbon tetrachloride.
Take care to prevent poisoning in this case.
c. Dry the coil with the method described in section (1).
d. Apply high-grade varnish with a brush, by spraying or by dipping while the coil is dry and still warm if possible.
e. Always check the insulation resistance before starting the motor.
13
. MAINTENANCE OF BEARING AND LUBRICATION
The changes in the grease's lubricating performance differ mainly on the type of grease, size and type of bearing,
operation speed, operation state and ambient atmosphere (dust and moisture).
The consumption of grease used to lubricate the bearings is very low, but special care must be taken to the lubrication
to prevent remarkable wear or accidents.
(1) Bearing lubrication and maintenance procedures
Table 10 Bearing lubrication and maintenance procedures
Shielded ball bearings
Ball bearings, roller bearings
Motor application range
According to Table 11
According to Table 11
Grease replenishment
Not required
*3
Use a grease gun to lubricate. Refer to
Section (2) for the lubrication method.
Applicable grease
Multemp SRL (Kyodo Yushi)
or urea grease (NTN: MP-1, NSK: EAM, JTEKT: KVC)
*1
Multemp SRL (Kyodo Yush)
*1
Frequency of grease
replenishment
−
According to Section (4)
Frequency of changing
whole grease
−
According to Section (4)
*2
Grease replenishment
mount, initial charge amount
−
According to Section (5)
(*1) The allowable limit of temperature rise is 65K (at an ambient temperature of 40°C) for the Multemp SRL and urea grease.
(*2) If unable to follow this lubrication frequency for some reasons, be absolutely sure to carry out the overhaul as described in "11. MAINTENANCE".
(*3) The recommended replacement frequencies for shielded ball bearings are as follows: Every 10,000 hours for 2-pole motors and every 20,000
hours for 4-pole motors and above (when lubricating with Multemp SRL grease).
(*4) The thermal service life of the urea grease is about 2.5 times longer than that of the Multemp SRL. Note, however, that using the urea grease will
not contribute to increasing the fatigue service life of the bearing.
Be sure to use the grease of specified trade names. If the type of grease is of the same soap base (same lithium
base, for example) and of the same oil base (diester oil, for example) or only the consistency is different between
the two, it could be practically all right. However, do not mix different kinds of grease of different soap bases (lithium
base and urea base, for example) or different kinds of grease of different oil bases (synthetic oil and mineral oil).
If you have to switch to grease of a different trade name, disassemble and thoroughly clean the concerned parts
before stuffing the new grease.