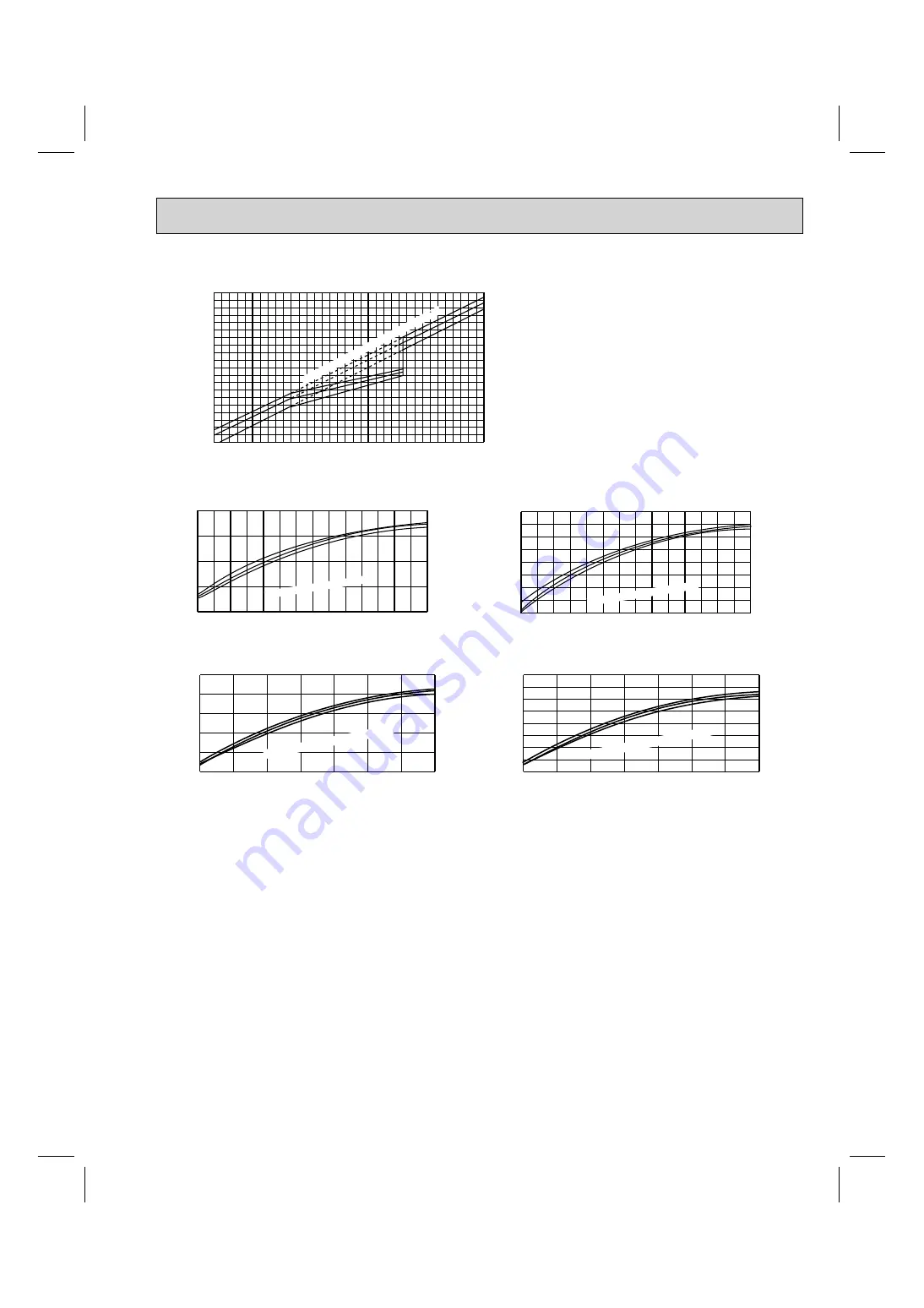
17
Heating
Indoor air Dry-bulb temperature
difference (°F)
Outdoor intake air WB temperature (°F)
-4
5
14
23
32
41
50
59
0.4
0.5
0.6
0.7
0.8
0.9
1.0
1.1
1.2
1.3
Heating capacity
(at Rated frequency)
Capacity correction factor
59
68
79
Indoor intake air Dry-bulb temperature ( F)
MUZ-WR24NA
This value of frequency is not the same as the actual frequency in operating. Refer to 7-5 and 7-6 for the relationships
between frequency and capacity.
75
70
65
-5
5
15
25
35
45
55
65
0.8
1.1
1.4
1.7
2.0
2.3
2.6
2.9
3.2
Indoor intake air DB temperature (°F)
= 702 CFM
Airflow
Outdoor intake air WB temperature (°F)
Total power consumption
(kW)
MUZ-WR09NA
MUZ-WR12NA
0
10
20
30
40
50
60
70
0.3
0.5
0.7
0.9
1.1
Indoor intake air DB temperature (°F)
= 406 CFM
Airflow
Outdoor intake air WB temperature (°F)
Total power consumption
(kW)
75
70
65
75
70
65
0
10
20
30
40
50
60
70
0.4
0.5
0.6
0.7
0.8
0.9
1.0
1.1
1.2
Indoor intake air DB temperature (°F)
= 406 CFM
Airflow
Outdoor intake air WB temperature (°F)
Total power consumption
(kW)
MUZ-WR18NA
75
70
65
-5
5
15
25
35
45
55
65
0.5
0.8
1.1
1.4
1.7
2.0
Indoor intake air DB temperature (°F)
= 625 CFM
Airflow
Outdoor intake air WB temperature (°F)
Total power consumption
(kW)
OBH819A
Summary of Contents for MSZ-WR NA Series
Page 9: ...9 5 WIRING DIAGRAM MUZ WR09NA MUZ WR12NA MUZ WR18NA OBH819A ...
Page 10: ...10 MUZ WR24NA OBH819A ...
Page 57: ...57 OBH819A ...