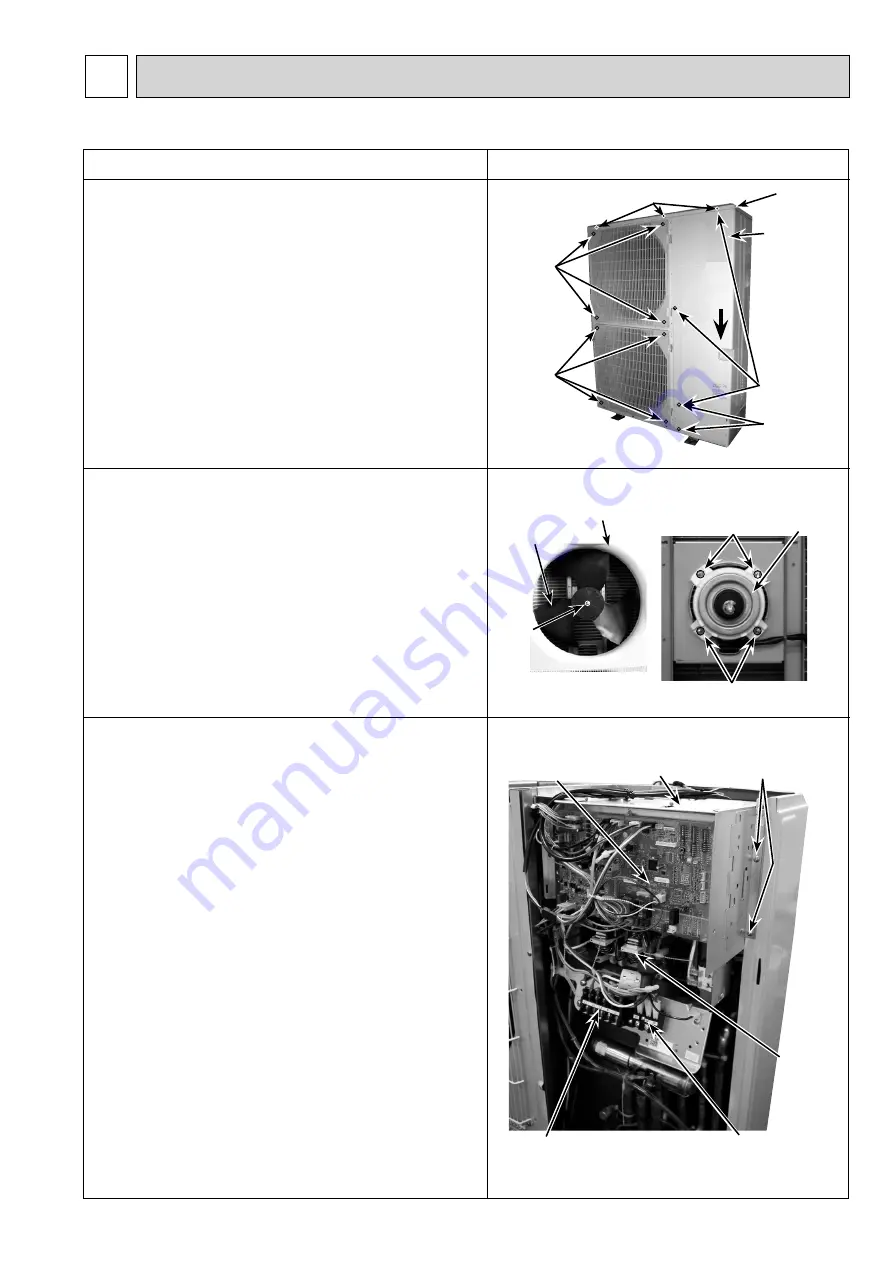
47
PUHZ-SHW230YKA
DISASSEMBLY PROCEDURE
9
Photo 4
3. Removing the electrical parts box
(1) Remove the service panel. (See Photo 1)
(2) Remove the top panel. (See Photo 1)
(3)
Disconnect the indoor/outdoor connecting wires from
terminal block.
(4)
Disconnect the connector CNF1, CNF2, LEV-A, LEV-B
and LEV-C on the controller circuit board.
<Symbols on the board>
• CNF1, CNF2 : Fan motor
• LEV-A, LEV-B, LEV-C : LEV
(5) Disconnect the pipe-side connections of the following parts.
• Thermistor <Liquid>(TH3)
• Thermistor <Discharge>(TH4)
• Thermistor <2-phase pipe>(TH6)
• Thermistor <Ambient>(TH7)
• Thermistor <Suction> (TH32)
• Thermistor <Comp. surface> (TH34)
• High pressure switch (63H)
• Low pressure switch (63L)
• High pressure sensor (63HS)
• 4-way valve coil (21S4)
(6) Remove the terminal cover and disconnect the
compressor lead wire.
(7) Remove 2 electrical parts box fixing screws (4 × 10) and
detach the electrical parts box by pulling it upward. The
electrical parts box is fixed with 2 hooks on the left and 1
hook on the right.
Noise filter
circuit board
(N.F.)
Terminal
block (TB2)
Controller circuit
board (C.B.)
Terminal
block (TB1)
Electrical parts box
fixing screws
Electrical parts box
1. Removing the service panel and top panel
(1) Remove 3 service panel fixing screws (5 × 12) and slide
the hook on the right downward to remove the service
panel.
(2) Remove screws (3 for front, 3 for rear/5 × 12) of the top
panel and remove it.
2. Removing the fan motor (MF1, MF2)
(1) Remove the service panel. (See Photo 1)
(2) Remove the top panel. (See Photo 1)
(3) Remove 4 fan grille fixing screws (5 × 12) to detach the
fan grille. (See Photo 1)
(4) Remove a nut (for right handed screw of M6) to detach the
propeller. (See Photo 2)
(5) Disconnect the connectors, CNF1, CNF2 on controller
circuit board in electrical parts box.
(6) Remove 4 fan motor fixing screws (5 × 20) to detach the
fan motor. (See Photo 3)
Photo 2
Photo 3
Fan motor
fixing screws
Fan motor
Fan motor
fixing screws
Front panel
Propeller
Nut
Photo 1
Top panel fixing screws
Top panel
Service panel
fixing screws
Service panel
Grille
fixing
screws
Grille
fixing
screws
Slide
Cover panel
fixing screws
OPERATING PROCEDURE
PHOTOS & ILLUSTRATION
OCH534