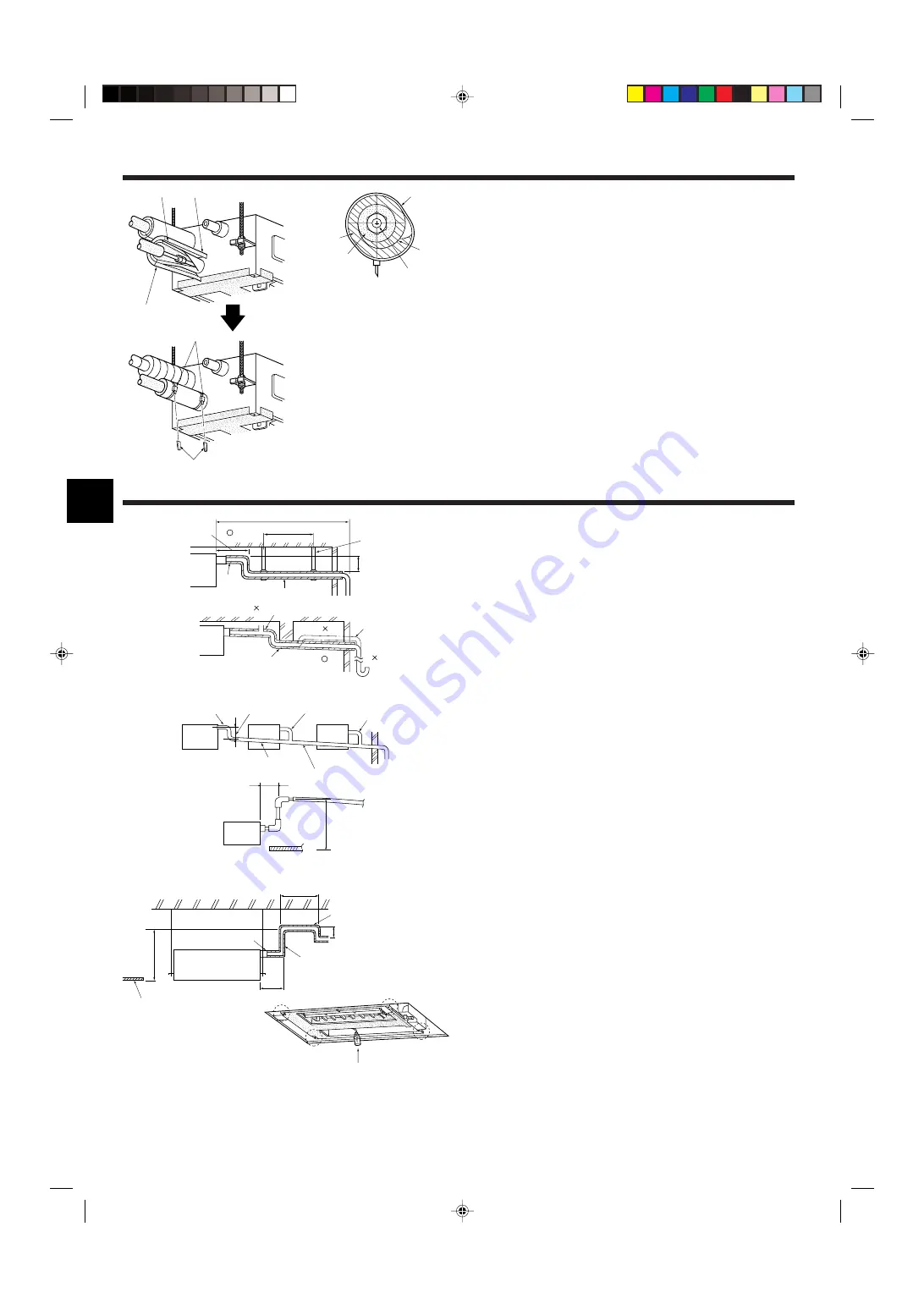
6
4. Drainage piping work
B
M
L
K
D
E
D
H
I
G
D
F
F
F
Max. 15cm
J
F
1
2
Max. 20m
0.75–1.5m
N
O
A
B
C
H
A
C
D
G
F
E
B
I
4.1. Drainage piping work
• Use O.D. ø26 PVC TUBE for drain piping and provide 1/100 or more downward
slope.
• Be sure to connect the piping joints using adhesive of polyvinyl chloride family.
• Observe the figure for piping work.
• Use attached drain hose to change the pipe extraction direction. (Fig. 4-1)
1
Correct piping
2
Wrong piping
A
Insulation (9 mm or more)
B
Downward slope (1/100 or more)
C
Support metal
K
Air bleeder
L
Raised
M
Odor trap
N
Make as little as possible
O
Make as great as possible (approx. 10 cm)
Grouped piping (Fig. 4-2)
D
VP20 (O.D. ø26 PVC TUBE)
E
Make it as large as possible
F
Indoor unit
G
Make the piping size large for grouped piping.
H
Downward slope (1/100 or more)
I
O.D. ø38 PVC TUBE for grouped piping.
(9 mm or more insulation)
J
Up to 50 cm
In cases of upward drainage
• The largest dimension possible for the vertical section at
B
is 60 cm from the lower
surface of the ceiling. Make this vertical section as short as possible.
Water drainage check
1. Fill the drainage pan with about 0.5 liters of water. (Don’t pour water directly into
the drain pump.)
2. Make a test run of the unit (in Cooling mode).
3. Check for water drainage at the transparent check window and the outlet of the
drainage pipe.
4. Stop the test run. (Don’t forget to turn off the power.) (Fig. 4-3)
Fig. 4-1
Fig. 4-2
A
Ceiling panel
B
Max. 60 cm
C
Position of drain outlet
D
Make as short as possible (Max. 15 cm)
E
Make as small as possible
F
Downward slope (1/100 or more)
G
Make as great as possible (Min. 10 cm)
H
Drainage pipe vertical section
I
Water bottle (procure locally)
Fig. 4-3
F
E
D
C
I
C
H
A
·
B
G
D
3.3. Refrigerant piping
1) Indoor unit
Installing procedures (Fig. 3-2)
1. Remove the flare nuts and caps from the indoor unit.
2. Flare-cut the liquid and gas pipes then apply refrigerating machine oil (to be lo-
cally procured) over the flare-cut seat surface.
3. Quickly connect the refrigerant piping.
∗
Remember to tighten the flare nuts with a double spanner.
4. Slide the supplied pipe cover
3
over the gas piping until it is pressed against the
sheet metal inside the unit.
5. Slide the provided pipe cover
3
over the liquid piping until it is pressed against
the sheet metal inside the unit.
6. Tighten the pipe cover
3
at the both ends (15 - 20 mm) with the supplied bands
4
.
A
Gas piping
B
Liquid piping
C
Band
4
D
Pipe cover
3
E
Turn the seam upward.
F
Press the pipe cover against the
sheet metal.
G
Refrigerant piping heat insulating ma-
terial
H
Wrap tightly
I
Cut off excess length of band.
Fig. 3-2
3. Installing the refrigerant piping