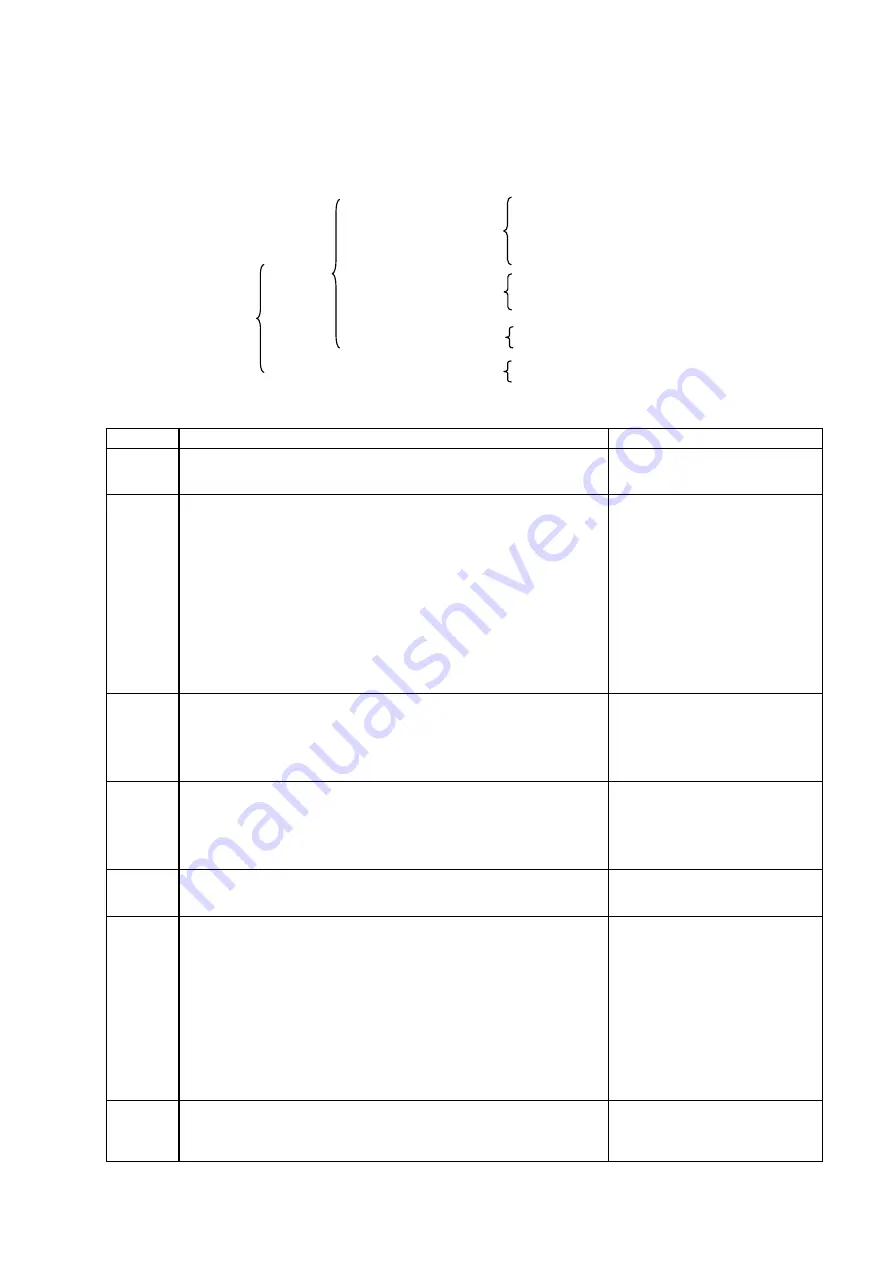
- 15 -
(6) Bearing noise
The easiest way to check a bearing is to listen to the noise it generates. Listen to the bearing noise
during operation so that abnormalities can be found at an early stage.
Note that the final diagnosis of the bearing also involves the vibration, temperature and discharged
grease. Thus, make sure not to miss a faulty part before the application is obstructed.
Bearing
noise
Intricate noise
Race noise
(All bearings
Single row deep groove radial ball bearings are
the main bearings)
Squeaking noise (Roller bearings)
Noise related
to rolling
bearing
Noise related to bearing
manufacture
Retainer noise (Ball bearings)
Roller dropping noise (Roller bearings)
Chatter noise (All bearings)
Noise related to incorrect
handling of bearings
Scratch noise (All bearings)
Dirt noise (All bearings)
Noise when bearings are assembled
Motor groaning noise
(Ball bearings, ball bearings and roller bearings)
Table 13
Cause of noise
Measures
Race noise
(normal
noise)
This noise is characteristic of the rolling bearing and occurs in every bearing.
The noise is generated when the roller rolls over the locus due to rotation of the
bearings. This should be a smooth and continuous noise.
Normal noise
Squeaking
noise
This is a "squeaking" noise generated by almost all roller bearings. It is a
metallic sound, and is caused by the non-uniform movement of the rolling
element in a no-load area. This noise has the following characteristics.
1) This noise is heard when grease lubrication is used, and is rarely heard when
oil is used.
2) This noise occurs easily when the lubrication performance (especially oil) is
poor.
3) This noise occurs easily during the winter.
4) This noise occurs easily when only a radial load is applied and the radial
clearance of the bearings is large.
5) This noise occurs at a certain rotating speed range, and the range differs
according to the size of the bearings.
(If this noise is heard, try replenishing a small amount of the designated grease.
This noise may be heard rarely in ball bearings.)
1) As long as the noise is not caused
by a heavy load, and is only due to
vibration or temperature, use can
be continued.
2) Replenish the grease.
3) Use bearings with a small radial
clearance.
4) Use grease that is soft and that has
a good oil performance.
5) Use a bearing for squeaking noise
measures.
Retainer
noise
This noise is heard when the retainer vibrates during bearing rotation and
collides with the rolling element. The noise is cyclic and has the following
characteristics.
1) This noise is heard in both grease lubrication and oil lubrication.
2) This noise occurs easily in ball bearings having a large radial clearance.
3) This noise occurs easily when a moment is applied to the outer bearing ring.
1) when using ball bearings, decrease
the radial clearance or apply a
pre-load.
2) Use a lubricant with good
lubrication performance.
3) Replenish the grease.
Roller
dropping
noise
This noise is generated due to the radial clearance and the relation of the
clearance between the retainer and rolling element. If the bearing is being used
in a horizontal rotor, this noise is generated when the balls drop faster than the
retainer due to the gravity of the rolling element when in a no-load area near the
top, and collide with the retainer. This noise is not heard during low speed
operation or normal operation, and often occurs just before stopping.
1) This is not an abnormal noise.
2) Decrease the radial clearance if
necessary.
Chatter
noise
The bearings vibrate when there is a circular spiral having a relatively large
crest on the inner/outer race raceway surface or rolling surface. If the speed is
constant, this sound will have a constant frequency.
1) Replace the bearings.
Scratch
noise
A cyclic noise sounding like a riveter and vibration will occur if the raceway
surface or rolling surface has scratches (scratches, indentation, rust). The cycle
will be constant if the speed is constant, and the cycle will lengthen as the
speed drops. In ball bearings, if the scratch is on the raceway surface, the
sound will be continuous. However, if the scratch is on the ball, the sound may
not be heard. There will still be a cycle to the noise. This noise may change if
grease is replenished.
1) Vibration of another device while stopped causes the ball pitch to scratch the
rolling surface.
2) Fretting (peeling) occurs on the rolling surface because of a large radial load
or large vibration.
3) Stripped patterns are formed on the rolling surface because of electrolytic
corrosion during inverter operation.
1) Replace the bearings.
2) Check the cause of the scratches.
3) Make sure that impact is not
applied on the bearings during
assembly or transportation, etc.
Provide insulation against vibration
between the device and motor.
4) Reduce the radial load and
vibration.
5) Lower the carrier frequency of the
inverter.
6) Install a filter.
Dirt noise
A non-cyclic noise is heard when there is dirt in the bearings.
1) When the bearings were not completely washed.
2) When foreign matter entered the lubricant.
3) When dirt entered the bearings during rotation.
1) Wash the bearings.
2) Replace the bearings.
Summary of Contents for HR Series
Page 2: ......
Page 33: ...MEMO ...