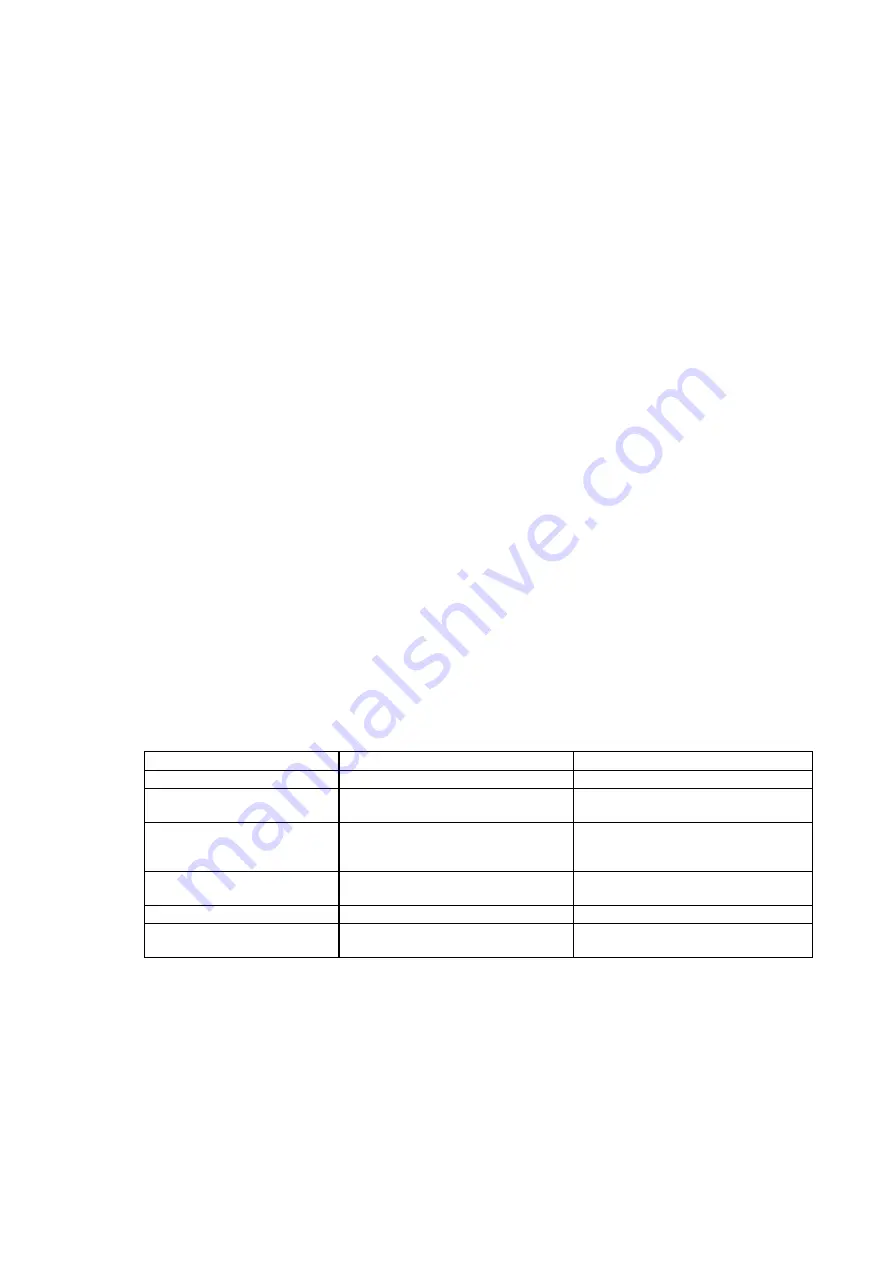
- 12 -
12. SERVICING OF COILS AND INSULATION
(1) When coil has absorbed moisture
Measure the insulation resistance with a megger tester when the coil has absorbed moisture
during shipment, storage or when the motor has been stopped for a long time, and at the times
specified in the maintenance plan. Always dry the coil when the measured value is lower than the
following values. It is recommended to use the motor at 100 M
Ω
or more. If the insulation
resistance is lower than the following value, do not use the motor.
Low voltage motor : 500V megger for one min., 1 (M
) at 40°C
To dry the coil, disassemble the motor, and use the following method until the insulation resistance
is restored.
a. Place the coil in an oven that does not exceed 90°C.
b. Cover the motor with a piece of canvas or equivalent material, open a hole at the top so the
moisture can escape, and dry by blowing hot air, or using a heating device or lamp. Adjust the
temperature so that it does not exceed 90°C and cause partial heating.
(2) When coil is dirty
If the coil is dirty or if the insulation resistance cannot be restored even when the coil is dry, clean
the coil with the following method.
a. Wipe dust on the coil off, or wash the coil with a cleaning solvent using hot water or low
pressure steam. After cleaning, rinse the coil with clean water.
b. If the dust cannot be removed with the solvent, wash the coil with a cloth or brush and volatile
oil, gasoline or carbon tetrachloride. Take care to prevent poisoning in this case.
c. Dry the coil with the method described in section (1).
d. Apply high-grade varnish with a brush, by spraying or by dipping while the coil is dry and still warm.
e. Always check the insulation resistance before starting the motor.
13. MAINTENANCE OF BEARING AND LUBRICATION
The changes in the grease's lubricating performance differ mainly on the type of grease, size and type
of bearing, operation speed, operation state and ambient atmosphere (dust and moisture).
The consumption of grease used to lubricate the bearings is very low, but special care must be taken to
the lubrication to prevent remarkable wear or accidents.
(1) Bearing lubrication and maintenance procedures
Table 10 Bearing lubrication and maintenance procedures
Shielded ball bearings
Ball bearings and roller bearings
Motor application range
According to Table 11
According to Table 11
Grease replenishment
Not required *3
Replenish with grease gun using
method given in (2).
Applicable grease
Multemp SRL (Kyodo Yushi Co., Ltd.)
or UREA Grease (NTN:MP-1,
NSK:EAM, JTEKT:KVC)
Multemp SRL (Kyodo Yushi Co., Ltd.) *1
Grease replenishment
frequency
–
According to item (4).
Grease replacement frequency
–
According to item (4). *2
Grease replenishment and
initial charge amount
–
According to item (5).
(*1)
The tolerable max. temperature rise of Multemp SRL or UREA grease is 65K (at ambient temperature of 40°C).
(*2)
If the above frequency cannot be observed for any reason, always replenish the grease during the overhaul explained in Section 11.
"MAINTENANCE".
(*3)
The recommended time to replace the shielded ball bearings is 10,000 hours on 2 pole motor, and 20,000 hours on 4 or more pole
motor (when Multemp SRL Grease is used).
Always use the designated brand of grease. There is no particular problem if the grease has the
same soap-base (ex. same lithium base), the same base oil (ex., diester oil) or if only the viscosity
differs. However, greases with differing soap bases (ex., lithium and urea base) or different types
of base oils (ex., compound oil and mineral oil) must not be used together. Overhaul the motor and
then change the brand if necessary.
Summary of Contents for HR Series
Page 2: ......
Page 33: ...MEMO ...