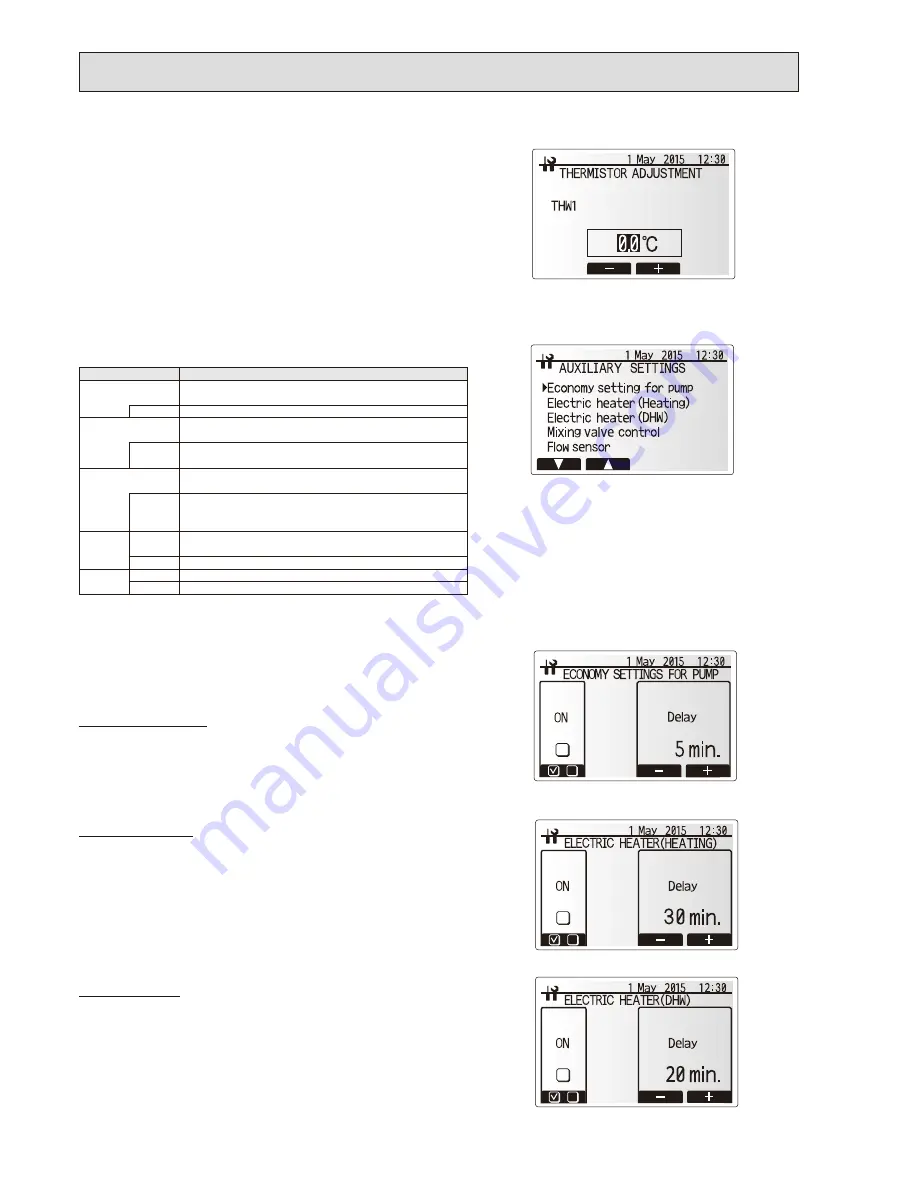
▼
▲
26
<Thermistor adjustment>
This function allows adjustments to be made to the thermistor readings from
−10 to 10°C in 0.5°C intervals.
THW1: Thermistor (Flow water temp.)
THW2: Thermistor (Return water temp.)
THW5: Thermistor (DHW tank water temp.)(Option)
THW6: Thermistor (Zone1 flow temp.)(Option)
THW7: Thermistor (Zone1 return temp.)(Option)
THW8: Thermistor (Zone2 flow temp.)(Option)
THW9: Thermistor (Zone2 return temp.)(Option)
THWB1: Thermistor (Boiler flow temp.)(Option)
THWB2: Thermistor (Boiler return temp.)(Option)
<Auxiliary settings>
This function is used to set the parameters for any auxiliary parts used in the system
Menu subtitle
Function/Description
Economy settings for
pump
Water pump stops automatically in certain period of time from
when operation is finished.
Delay
Time before pump switched off *
1
Electric heater
(Heating)
To select “WITH booster heater (ON)” or “WITHOUT booster
heater (OFF)” in Heating mode.
Delay
The minimum time required for the booster heater to turn ON
from after Heating mode has started.
Electric heater (DHW) To select "WITH (ON)" or "WITHOUT (OFF)" booster heater or
immersion heater individually in DHW mode.
Delay
The minimum time required for the booster heater or immersion
heater to turn ON from after DHW mode has started. (This
setting is applied for both booster and immersion heater.)
Mixing
valve
control *
2
Running
Period from valve fully open (at a hot water mixing ratio of 100%)
to valve fully closed (at a cold water mixing ratio of 100%)
Interval
Interval (min) to control the Mixing valve.
Flow
sensor *
3
Minimum
The minimum flow rate to be detected at Flow sensor.
Maximum
The maximum flow rate to be detected at Flow sensor.
*
1
Decreasing "time before pump switched off" may increase the duration of stand-by in
Heating/Cooling mode.
*
2
Set the Running time according to the specifications of the actuator of each mixing valve.
It is recommended to set the interval to 2 minutes that is a default value. With the interval
set longer, it could take longer to warm up a room.
*
3
Do not change the setting since it is set according to the specification of Flow sensor
attached to the hydrobox.
Economy settings for pump
1. From the Auxiliary settings menu highlight Economy Settings for water circulation pump.
2. Press CONFIRM.
3. The economy settings for water circulation pump screen is displayed.
4. Use button F1 to switch the economy settings ON/OFF.
5. Use buttons F3 and F4 to adjust the time the water circulation pump will run. (3 to 60
minutes)
Auxiliary settings menu screen
Electric heater (Heating) screen
Electric heater (DHW) screen
Electric heater (Heating)
1. From the Auxiliary setting menu highlight Electric heater (Heating).
2. Press CONFIRM.
3. The Electric heater (Heating) screen is displayed.
4. Press F1 button to switch the function ON/OFF.
5. Use F3 and F4 buttons to adjust the time period of heat pump only operation
before the booster heater will assist in space heating. (5 to 180 minutes)
Electric heater (DHW)
1. From the Auxiliary settings menu highlight Electric heater (DHW).
2. Press CONFIRM.
3. The Electric heater (DHW) screen is displayed.
4. Press F1 button to switch the function ON/OFF.
5. Use F3 and F4 buttons to adjust the time period of heat pump only operation
before the booster heater and the immersion heater (if present) will assist in
DHW heating. (15 to 30 minutes)
Economy settings for pump screen
OCH590B